Question 27: What are the Best Practices around minimizing risk of catalyst or equipment damage during turndown operation of a steam methane reformer hydrogen plant?
OHMES (KBC Advanced Technologies, Inc.)
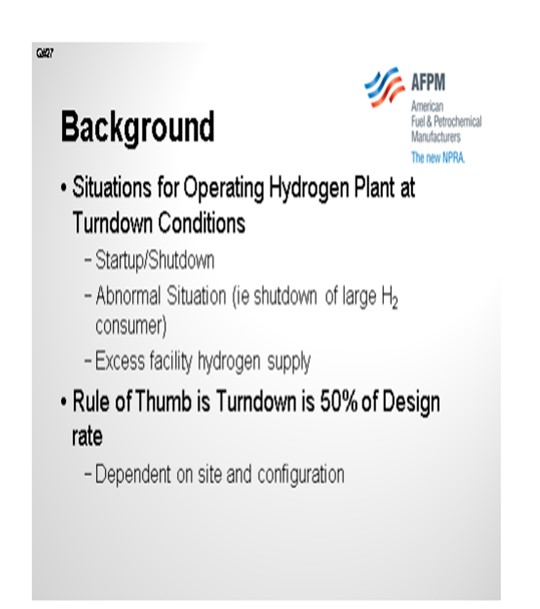
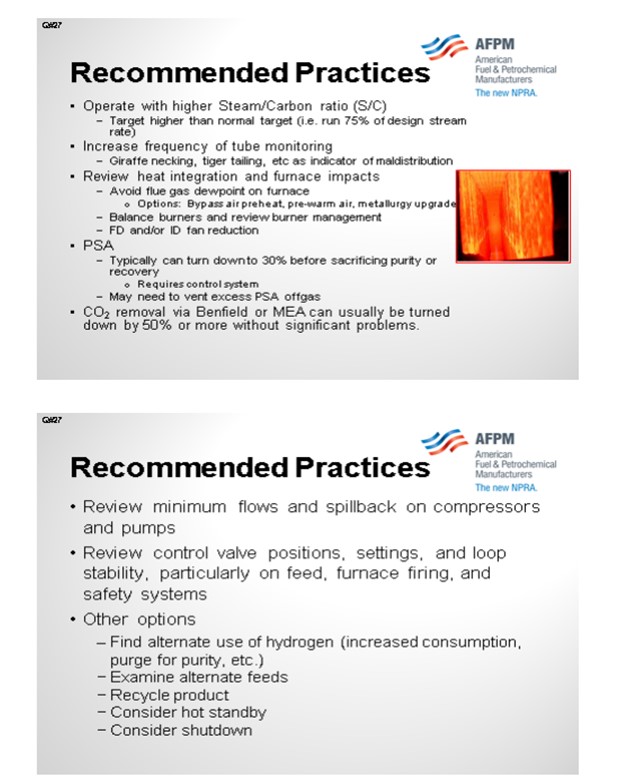
OHMES (KBC Advanced Technologies, Inc.) and ROSS BRUNSON, III (Süd-Chemie, Inc.)
First, there are several scenarios where operating at a turndown condition is required:
• Start-up/shutdown
• Abnormal situations (i.e., when a large H2 consumer is off-line or shut down)
• Excess facility hydrogen supply (becoming more typical)
As with any non-standard operating scenario, the unit’s operation should be carefully reviewed, and clear operating procedures and guidelines developed.
The general rule-of-thumb is that most hydrogen plants are designed to operate continuously at 50% of original design capacity. A review of select hydrogen plant vendor’s experience on PSA plants resulted in the following (in no particular order):
• Foster Wheeler (FW) o Turndown to 50% is generally managed without significant changes in process conditions or equipment.
o Design changes and operator attention can achieve 30% turndown.
o The primary areas of focus are feed preheat, burner turndown, temperature distribution in the furnace radiant section, flow measurement, and PSA cycle time.
o With a FW Terrace Wall™ reformer, one level of burners can be turned off at low turndown to maintain burner control.
• CB&I
o The majority of plants designed to achieve 50% turndown.
o Plants can be designed for lower turndown ratio, typically to 30%.
o Primary focal areas are flow distribution and operating ranges of control valves.
o Increased steam/carbon ratios are recommended to maintain distribution.
o Parallel control valves can be utilized for stable operation at low turndown.
• Technip Stone & Webster
o They can typically achieve a 35% to 40% turndown.
o They have provided plants with a turndown capability of 20% to 25% of original design.
o Their primary focal areas are burner management, flame stability, and distribution.
A review of the original design criteria can clarify what the immediate minimum operation involves. As part of this review, or for those facilities that need to further reduce capacity, the following recommended practices should be considered:
1. Operation with high steam/carbon (S/C) ratio: Depending on the feedstock and configuration, most units operate with an S/C ratio between 3 and 7. However, during a turndown situation, the operator should target a higher S/C ratio and run at least 75% of the design steam rate. Doing so helps maintain adequate mass flux in the tubes to achieve good distribution, avoid hot tubes, and minimize catalyst damage. Proper steam rate is the key issue when operating at turndown conditions. Maldistribution especially becomes a concern when the tube pressure drop reaches 10 psi.
2. Increase frequency of tube monitoring: Normal practice is to complete visual and pyrometer temperature measurement of Reformer tubes once per shift. During turndown conditions, monitoring frequency should increase. In particular, look out of tubes that are operating hotter (i.e., whiter) than other tubes, hot spots (giraffe necking), or hot bands (tiger tailing).
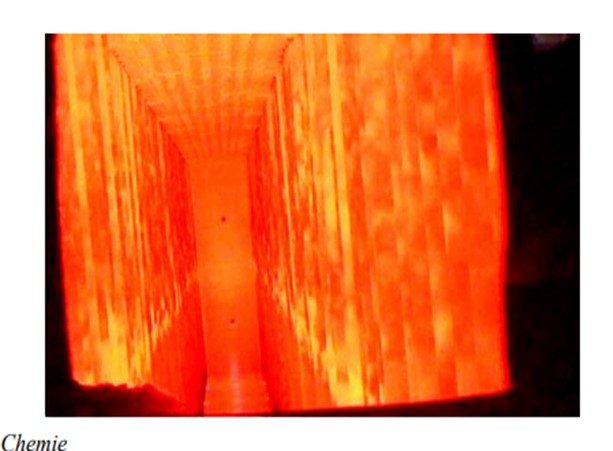
3. Review heat integration and furnace impacts: Several aspects require review in the area of the furnace and heat recovery sections. First, avoid dew point of the flue gas, which leads to corrosion. In some cases, bypassing the air preheat, pre-warming makeup air, or metallurgy upgrades are required. Obviously, fewer burners are required in this scenario, so ensure the unit can maintain proper firing balance in the furnace at these conditions. Also, review the burner management protocol to avoid an unnecessary unit trip. Finally, there will be less load on the FD and/or ID fans, so review the capability to reduce fan operation while maintaining acceptable oxygen levels and draft.
4. Hydrogen purification implications: Whether the unit has a pressure swing absorption (PSA) system or a CO2 removal system (such as Benfield, Catacarb, or MEA), these sections of the plant can normally operate at lower turndown than the reformer section. PSAs can normally be run to 30% of design, but require a control system to do so, which most modern units already have included. The primary downside is a slight sacrifice in purity or hydrogen recovery. Depending on the fuel input requirements, some PSA off gas may need to be excessed from the unit.
5. Review instrumentation, pumps, and compressors: While normally not a key constraint at turndown conditions, the pump and compressor systems should be reviewed to ensure minimum flow operation is avoided. For most units, instrumentation often limits the minimum sustainable throughput. Therefore, review control valve positions, variable setpoints, control loop stability, and safety systems, particularly on feed rate, furnace firing, and steam injection control. In some cases, parallel control valve and alternate ranged flow indicators have been installed for units running regularly in turndown.
6. Consider other options: While operating at low rates may be required on a short-term basis, if this situation becomes the new “normal”, the following options should be considered to improve the utilization of the unit.
• Find alternate use of hydrogen, such as increasing hydrotreater purge rates to increase cycle length or raise unit severity to increase volume swell.
• Consider alternate feedstocks as the unit may now have capacity for opportunity feeds.
• Some operators have recycled product to maintain mass rates.
• Operate the unit on “hot standby” if the facility does not need the hydrogen but wants a backup source ready to put into service rapidly.
JOSH SIEGEL (Johnson Matthey)
There are several considerations around minimizing risks when operating a steam methane reformer hydrogen plant at turndown conditions. First it is important to control the heat input to the furnace. It may be necessary to throttle back and/or turn off burners in the furnace to maintain the desired exit temperature. If the exit process gas temperature indicator is located in the exit header, it may not give an accurate reading of the gas temperature at the catalyst exit due to the increased heat loss, and as such we recommend operating to a fixed methane slip. To avoid overheating the catalyst it is important that frequent monitoring of the reformer tubes be completed. It is recommended that tube wall temperature (TWT) measurements be completed at least once per day, along with several visual inspections of the tubes, to locate any indications that there is overheating.
Secondly, the maximum turndown rate is a function of the plant’s design and will vary from plant to plant and site to site. Manufacturers of steam methane reformers have a minimum recommended flow rate to achieve good flow distribution through the tubes. Inaccurate flow meter readings could lead to maldistribution of flow through the primary reformer resulting in localized heating. This localized heating can cause catalyst deactivation from both sintering and carbon formation, and a reduction in steam methane reformer tube life which could subsequently result in tube failures. To address this, key instruments, such as feed and steam flows, should be pressure and temperature compensated. If the steam to carbon ratio is increased during turndown to maintain mass flow through the primary reformer, it is important that the resulting operating conditions do not lead to oxidation of the steam reforming catalyst. If the plant has a low temperature shift reactor (LTS), the LTS inlet temperature needs to be maintained at least 30°F (15°C) above the dew point of the process gas as the steam flow rate is increased.
Heat integration is another aspect to consider when running a hydrogen plant at turndown rates. It is important that the inlet temperature to the purification system stay above 570°F (300°C) to maintain the most efficient removal of poisons such as sulfur and chloride. If the temperature to the purification system falls below this level the efficiency of the removal process for these poisons will decrease which could result in slippage and the poisoning of downstream catalyst.