Question 27: The sulfur block is a crucial downstream component of hydroprocessing operations. What are some of your Best Practices or new developments for optimizing operations and increasing reliability?
SARAH LONG (HollyFrontier Corp - Navajo)
The sulfur block is a very mature technology. There have been few new developments to optimize operations. Optimizing operations of a sulfur plant can indicate an increase of sulfur production while reducing all related sulfur emissions. Some of the new developments in a sulfur plant consist of catalyst-burner design, dip leg improvement, upgrade of ferrule types, oxygen enhancement, oxygen enrichment, TGU developments, and increase in safety stewardship. Process variables can strongly vary from sulfur plant to sulfur plant, but general Best Practices are consistent.
There are several areas to focus when it comes to Best Practice. Poor reaction stoichiometry can impact overall sulfur plant operability from the front end of the SRU to the back end of the TGU. Reaction stoichiometry directly affects catalyst life and catalyst capabilities, as well as amine adsorption. Air demand analyzer is used for best control.
Reaction furnace and converter outlet temperatures are a critical part of optimizing an SRU. The reaction furnace temperature should be operated at temperatures exceeding 2300°F to convert all ammonia molecules. Operating below 2300°F could lead to ammonia salt deposits and cause pressure differential constraints. Within the industry, converter one should be monitored for adequate temperatures because of the potential to be run at temperatures that are too low. Recommended converter one target is a temperature greater than 620°F. However, converters two and three should not be operated at temperatures too high. The sequential converters should target an outlet temperate that is 18°F above the sulfur dew point to avoid sulfur condensation. The outlet temperature is a greater concern for the final condenser prior to the inlet of the TGU section of the sulfur block. Operating at 18°F above sulfur dew point decreases the chance of liquid sulfur entrainment and increases unit efficiency, in terms of conversion. To eliminate sulfur entrainment further, addition of coalescing pads in all condensers should be evaluated. At no point should sulfur components be bypassed around converter beds. Also, optimal duties should be evaluated for the first condenser, as well as the charge reheater in the SRU. Changing reheater types can have big impact on catalyst due to oxygen degradation.
As always, Best Practice also includes stable operations, but the main goal of the SRU is to avoid operational upsets or unscheduled outages. Within industry, the most common PSM-related issues occurring in an SRU consist of:
-
Plugged off quench columns,
-
Sooted catalyst beds,
-
Waste heat boiler damage, and
-
Sulfur storage fires and/or explosions, and
-
Vessel and pipe corrosion failures, resulting in leaks to atmosphere.
Locally, we have experienced several issues that resulted in unscheduled outages. Our most common outage regards TGU SO2 breakthrough. With the instrumentation locally available, a lag occurs from the backend air demand ratio to frontend air controls. For example, an upstream unit has an upset and hydrocarbon is introduced to the SRU. As a result, the air demand ratio is adjusted as additional air is required with introduction of hydrocarbon. When the upstream unit stopped the hydrocarbon carryover, the lag in air demand was long enough to allow excess oxygen to the TGU, resulting SO2 breakthrough.
Some of the different types of catalysts consist of:
-
Clause-base alumina catalyst promotes the standard hydrogen sulfide (H2S) reactions. Base alumina catalyst does not contribute to carbonyl sulfide (COS) and carbon disulfide (CS2) hydrolysis. Alumina catalyst is common for processes of high H2S purity. The typical life span of base alumina is five years.
-
There is an optimized alumina catalyst that targets COS and CS2 hydrolysis. This type will also boost clause reaction. This type of catalyst is recommended for capacity-limited units.
-
Titanium dioxide (TiO2) catalyst has bigger pores, high COS, and CS2 hydrolysis, is resistant to sulfidation, and increases run time.
-
Oxygen scavenger catalyst is an iron-based catalyst. Oxygen scavenger is self-regenerating. This catalyst is recommended for SRUs with direct reheaters.
LIFENG ZHENG (Criterion Catalysts & Technologies)
Reliable sulfur block performance is crucial to the utilization of other refinery assets. Below is a list of Best Practices Criterion would like to share:
-
Operate Claus unit final condenser at optimum temperatures (260 to 275ºF) to minimize sulfur vapor loses and maximize sulfur recovery. The final condenser’s primary function is to condense and separate as much liquid sulfur as possible to reduce the load on the TGU (tail gas unit). Its operating window should be below the sulfur dew point and above the sulfur freezing point (246ºF), plus some additional margin to prevent freezing in the condenser (typically 15ºF). If there is a demister pad installed in the final condenser, ensure that it is adequately heat-traced to prevent pluggage and pressure drop concerns.
-
Operate TGU (tail gas unit) burner properly to prevent oxygen ingress and sooting. Improper operation of burner controls is the prime cause of premature TGU catalyst failure. Above 90% stoichiometric requirement air addition for full combustion of the fuel, oxygen ingress into TGU catalyst can occur. In addition to causing irreversible catalyst deactivation via sulfidation, oxygen is typically associated with SO2 breakthrough that causes SO2 emission exceedances, TGU amine degradation, low pH in the quench water system and fouling of the quench system. Care must be taken to avoid adjusting the air demand too low on the TGU burner; as depending on the RGG (reducing gas generator) burner design, this action can result in soot deposition on the TGU catalyst, which can lead to decreased activity and increased DP.
-
Maintain air demand analyzer, H2 analyzer, and pH meter in working order.
-
The air demand analyzer is utilized to maintain constant and proper air rates to the Claus reaction furnace (the typical target ratio of H2S:SO2 is between 2:1 and 4:1) to maximize SRU sulfur recovery and minimize load on the TGU unit.
-
The hydrogen analyzer is utilized to ensure that sufficient hydrogen is supplied to the hydrogenation reactor to convert all non-H2S sulfur species to H2S. It will also allow optimization of excess hydrogen to reduce operating cost.
-
The pH meter in the quench water is utilized to notify Operations of SO2 breakthrough from the TGU reactor so appropriate action can be taken to correct the SO2 breakthrough and/or reduce corrosion rates. Due to the extremely low residence time for the SRU/TGU, Operations personnel are only provided with a very narrow window to make corrections before an environmental exceedance event will occur. These analyzers are crucial equipment that will help Operations personnel make the correct adjustments to protect the unit equipment and prevent environmental exceedances.
-
Poorly maintained analyzers will result in delayed operation response and, worse, incorrect responses that can result in process safety incidents and costly production losses.
-
Maintain proper amine hygiene in the ARUs (aromatic recovery units) and the TGUs (tail gas units). Poor amine hygiene can result in foaming, corrosion, and loss of absorption efficiency. For the TGU to meet the stringent environmental requirement for SO2 emission, all but a small fraction of the H2S can be entrained in the gas going to the tail gas incinerator. Any non-absorbed H2S directly impacts SO2 emissions. Amine hygiene is recommended to be checked at least once a month.
-
Utilize large-diameter catalyst with uniform size distribution. To ensure long operating cycle lengths, it is important to utilize large-diameter catalyst with uniform size distribution in both the SRU reactors and the downstream TGU hydrogenation reactor. Large diameter catalyst will result in lower pressure drop across the catalyst beds and maximize unit capacity. A non-uniform size distribution can cause significantly higher pressure drop, flow maldistribution, and lowered fouling resistance because the wide range of particle sizes decreases void fraction and the average flow passage diameter.
-
Lastly, establish daily/weekly/monthly proactive monitoring and follow through with it. Many of us are inundated with day-to-day activities such that proactive monitoring tends to fall by the wayside. However, proactive monitoring is needed to identify long-term threats before they become short-term nightmares. Process variables ranging from production capacity, sulfur recovery, DP, catalyst performance, amine hygiene, etc. all need to be monitored on a set frequency. Timely identification and correction of process issues improves unit reliability and reduces cost. Criterion can help you with setting up your monitoring strategy.
COURTNEY E. LANE (ProSys, Inc.)
Gas temperature is a critical process variable in Claus combustion chambers of sulfur recovery units. Successful control of this variable ensures safe operating conditions and low fouling rates; namely, low salt formation in the presence of ammonia. Infrared pyrometers and shielded thermocouples are the main temperature sensory methods, but each is subject to external forces (e.g., flame transparency and purge rates).
What happens when measurement values from two apparently functional sensors indicate significant contradictory behaviors? In other words, Sensor A exhibits decreasing temperature while Sensor B indicates increasing temperature (Figure 1). Which one is demonstrating the expected behavior? Are they both? Is it worth risking equipment damage? This was an obstacle encountered during a sulfur recovery unit advanced regulatory control project.
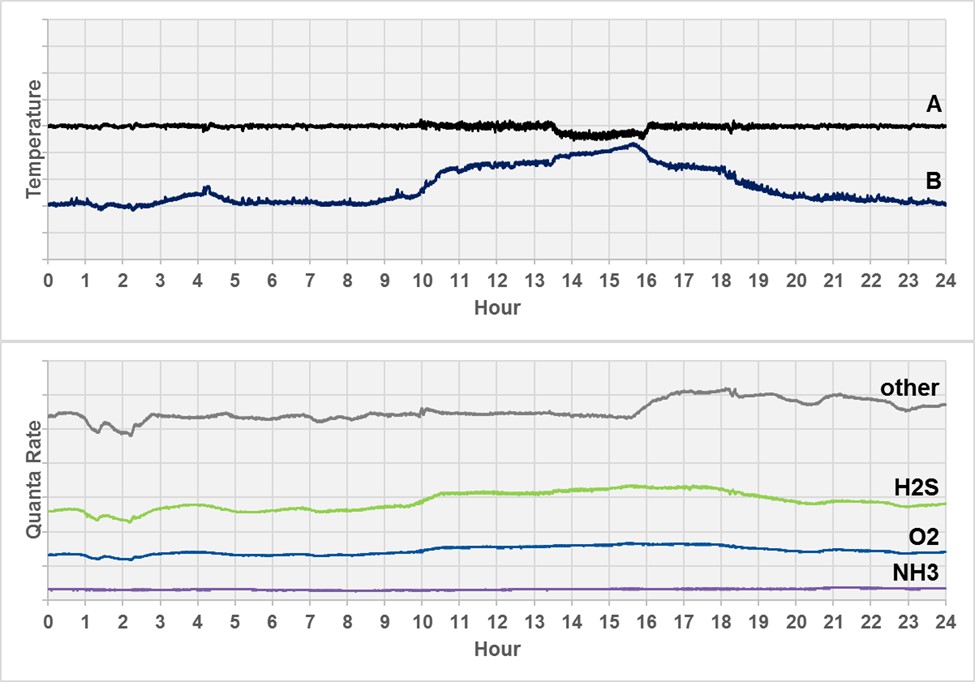
Figure 1. Five-Second Resolution Data of Two Combustion Chamber Temperature Sensors and the Inlet Quanta Rates of Relevant Components
An analytical model was developed using fundamental material and energy balances for real-time temperature estimation within a control system (Figure 2). The intent of this model was to provide insight into the expected behavior of the measured values. The inputs to the model are the inputs to the mixer.
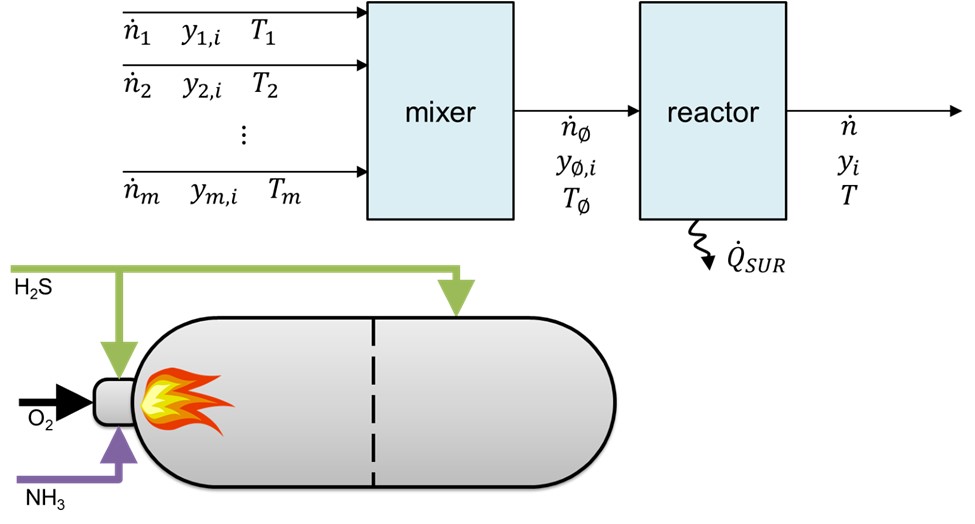
Figure 2. Schematic of System to be Modeled.
The measured value of a zone-two gas pyrometer was used to regress the relevant transfer coefficients. Different sections of the chamber were modeled through selection and limitation of relevant reactions. The regression objective function was weighted to favor the prediction of temperatures, which were higher than their measured counterparts.
One month of recorded data was collected and analyzed, and it was determined that the standard deviation from measurement was less than 65°F (Figure 3). Note: Regression objective function is weighted to favor overestimation of the predicted value.
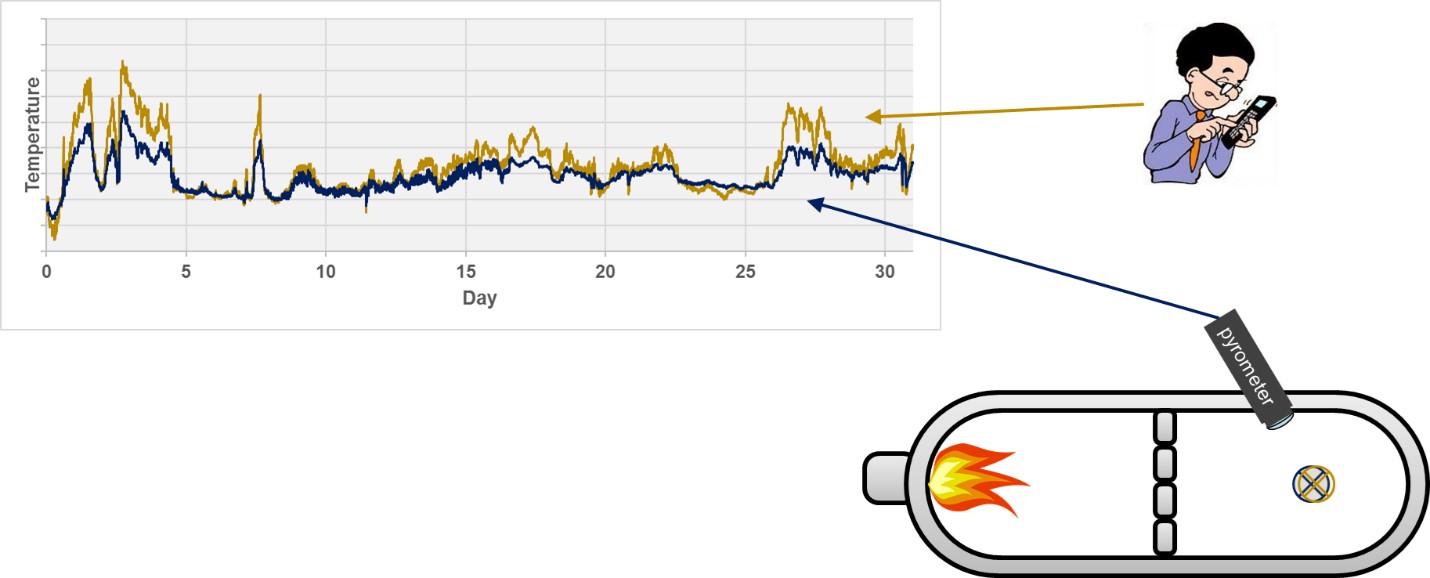
Figure 3. Comparison of Measured and predicted Values over one Month.
To provide some context, a typical operating temperature is greater than 2,000°F. It was found that the model provided valuable insights into the behavior of the combustion chamber (Figure 4). The calculation is still maintained in the control system over a year after its original purpose had been fulfilled. The calculated value was incorporated into a high-temperature override selector to prevent future equipment damage.
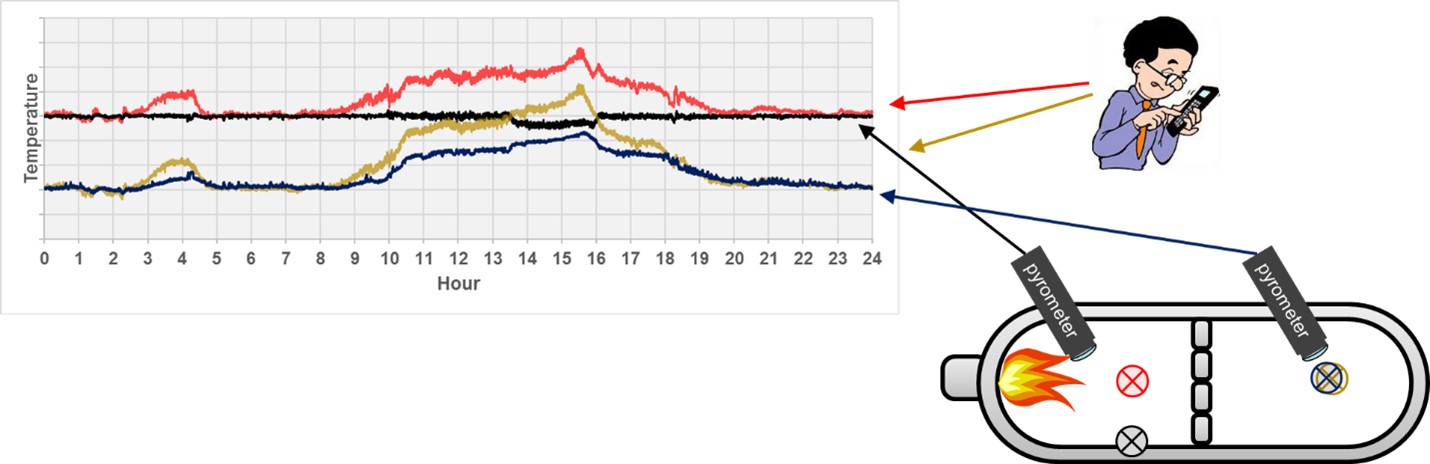
Figure 4. Comparison of Measured and Predicted Values over One Day (see Figure 1)
RAMACHANDRAN (Bharat Petroleum Corporation Limited)
I will just add to what Sarah said. Regarding reliability, there are some simple principles and practices which have helped sulfur plants be operated as close as possible to the design. We have found that electrical heaters, instead of inline burners with fuel gas or any other fuel, are very reliable, in terms of maintaining temperature.
I have seen innovative designs of the wall of the main combustion chamber in place of a checker wall. Use of tangential liquid sulfur outlet nozzles in sulfur condensers, instead of vertical downward nozzles, is an option to avoid plugging. Proper design of sulfur degassing system, which is generally ignored, is an important factor for better reliability. The use of stainless-steel sulfur pits, which is a bit costly, is an option to ward off corrosion and failure. Last but least, provision of jacketed walls on Claus reactor bypass has been very useful.
On the Best Practices side, I want to make a couple of points. First, maintain optimum temperature of the main combustion chamber to ensure destruction of ammonia and prevent plugging of ammonium sulfide salt deposits. The air demand analyzer, as Sarah mentioned, is a key component. Nowadays, I think it is not a choice; it is a necessity.
During startup, heat up the reactors quickly to ward off the formation of sulfuric acid or the formation of carbon black residue deposits. Operating on clean fuels, like LNG (liquefied natural gas) or hydrogen, is a good operating practice.
Monitor critical parameters like low feed temperature and shift in temperature rise across reactors. Incinerator plume color is another good observation to note. Use nitrogen as a purging medium for flame scanners, site glasses, and thermocouples to avoid increase in excess air. Maintain certain minimum operating levels in sulfur pits at all times to avoid pyrophoric fires.
I also see certain refiners’ practice as having spare bundles for sulfur condensers to ensure that there is no downtime in sulfur plants all in the context of having more reliability of hydrotreating processes and higher onstream factor. Ensuring clean sulfur rundown lines, removing catalyst dust, properly aligning bundles, and ensuring good workmanship at turnaround times are some practices that have been of great value to operators in the long run.
PAPPAL (Valero)
As hydroprocessing operators, we cannot forget the operation of the amine absorbers and the impact on the downstream amine regenerator; and ultimately, on the sulfur plant. Improper operation of the amine absorber can carry hydrocarbon to the amine regenerator, causing a foamover. There is a high probability of tripping the sulfur plant. It is important to operate the upstream amine system properly.
GREG BERRY (Andeavor)
I think it is great that we are talking about sulfur plants in the middle of the Hydroprocessing Q&A, but I would like to know the panel’s opinion about Best Practices on the sweet crude you use on your sulfur storage tank and whether you use nitrogen or air.
AGGUS (Becht Engineering Co., Inc.)
I will chime in on that one. I think many people will disagree about the use of nitrogen. I do not know. You have an issue with nitrogen in that you are going to build up some static charge. I have heard the concern that it does create a fire hazard, but I have never seen that play out. I mean, I think as panelists, unless someone else up here has something, we all basically agree on nitrogen.
LONG (HollyFrontier Corp - Navajo)
I would refer to sulfur experts, but I believe nitrogen is a preferred source. If air is in your sulfur pit, sulfur fires are a potential result, depending on the type of sulfur storage at the site. The different types – pit or a tank – can bring on different concerns. Pits are more prone to issues comparatively.
JOHNSON (Motiva Enterprises LLC)
I agree. Your preferred medium for sulfur storage tanks is air as opposed to nitrogen. Eductors are ‘normally’ used for pits and routed to the front end of the thermal reactor.
GREG BERRY (Andeavor)
Do we have any more closet SRU engineers out there?
RICHARD DAWS (CITGO Lake Charles Refinery)
I think there have been some industry explosions on the tanks where nitrogen was used but was not effectively kept in use full-time. Then when oxygen ever got into the tank, the pyrophoric material on the walls auto-ignited and caused the spark that caused the explosion. As I understand, there have been explosions on sulfur storage tanks that had been nitrogen-blanketed.
AGGUS (Becht Engineering Co., Inc.)
The key there is to have good remote flow sensing on your nitrogen. There needs to be an alarm going to the control room if you do this type of scheme. I think that is your Best Practice. I also want to mention that in a situation where you have the tank down for maintenance, you need to keep it wetted. So, if you are drawing down the sulfur level at any part of that tank, and if any part of the walls of the tank or roof is exposed, then the exposed area always needs to be wetted.