Question 25: What is the optimum role for hydrocrackers in refineries that do not utilize or are eliminating their bottom-of-the-barrel processes due to lighter crude blends?
AGGUS (Becht Engineering Co., Inc.)
This is about the most loaded question on earth; because as you all know, there is no one answer for every refinery regarding the ideal role for your hydrocracker. I will go through my answer, but the theme I will keep repeating is: maximize your existing assets. There are many refiners throughout the U.S. that have been fortunate enough to have existing assets which allow them to capitalize on the shale gas or semi-shale boom in the U.S. Some of them retooled to take advantage of the availability of these crudes, so I will go through a few case studies to show where their hydrocrackers fit in.
The first case study shown on the slide is a refinery with multiple crude units. In the past, it was a purchaser of VGO (vacuum gasoil) for cat feed. They undertook a project to increase crude capacity, which will be a common theme here also since capacity increases tend to accompany running domestic crude. This project was coupled with a switch to resid-to-the-cat operation due to the lighter crude. These projects allowed this refinery to become VGO-long. The economics of their HCU (hydrocracker unit)-to-FCC split did not really change, and the pursuit of volume swell was still the goal. Considering this scenario, the plan for this refinery was 1) to increase the rate of AGO (atmospheric gasoil) going to the hydrocracking unit, 2) to move LCO (light cycle oil) that was previously going to the hydrocracker to the other high-pressure diesel treaters, and then 3) route back resid with the purchased VGO to the SCC (stress corrosion cracking) units. Again, this refinery is VGO-long; but unfortunately, they are in a position where they cannot turn down the capacity of their SRUs (sulfur recovery units) enough to take full advantage of the sweet VGO. So, this refinery is at a position where it must do a sweet-for-sour VGO swap. That is the first situation.
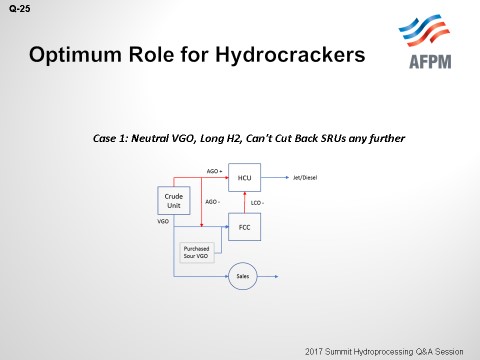
The second case is a VGO-short refiner. This refiner opted to shift LCO to the hydrocracker and push AGO back to the cat to accommodate this light crude slate from the domestic crude. As you all know, if you are running domestic at your refinery, you are increasing distillate yield. So, to accommodate increased distillate yield, the refiner will back LCO out of the other treaters, which will move the hydrocracker into primarily being an aromatic saturation unit for LCO.
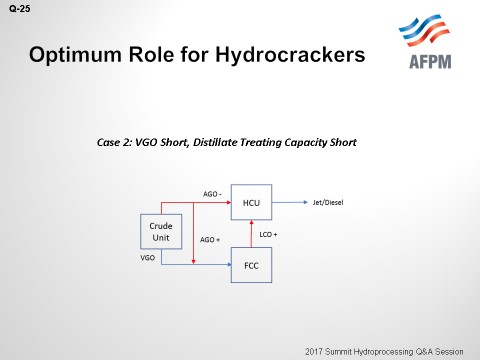
The third case study has to do with switching to a lighter crude slate that is driven with the shale crude. This crude slate shift happened at another refinery when they opted solely to turn their hydrocracker into a diesel hydrotreater. This decision was driven, again, by the increase in distillate production with the new crude blend. The refinery also had a lack of hydrogen availability. The capital cost required to address that hydrogen availability issue did not merit keeping the unit as a hydrocracker. So, this refinery found itself in a position where they would be hydrogen-short if it continued to hydrocrack.
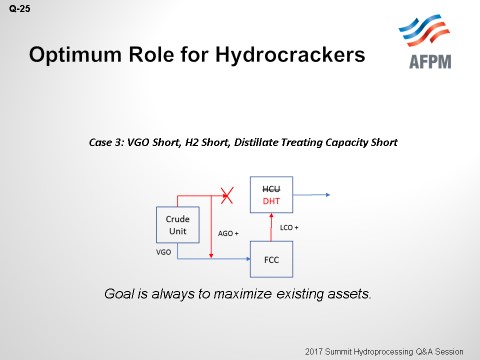
There are other solutions available. I think we all know about UOP’s LCO-X technology. That option might make sense for some refiners’ converting their hydrocracker to an LCO-X unit. Maybe there are some success stories out there. Switching to shale crudes usually means you will get an increase in straight-run naphtha, which would leave a lot of refineries octane-short. The reasons are 1) because you will have a naphtha increase, and 2) a lot of the shale crudes are very paraffinic, and the octane number is terrible. Some refineries have a long-term gasoline-to-diesel advantage. They may consider options like those I just mentioned. There is another option that is specifically available to refiners who have a two-stage hydrocracker: You can convert the first stage to a treat-only reactor and split the interstage product between the cat and the second-stage hydrocracker reactor. That modification will offset the potential feed-sulfur increase from sending your vacuum tower bottoms to the cat. It will also keep you from needing a cat gasoline treater revamp.
There is no one solution. The hydrocracker’s place in a refinery, along with the switch of resid to FCC feed, depends on many factors.
-
Is there a crude capacity increase accompanying this new lightening slate?
-
Can you adjust your cat severity to balance LCO make with the new VGO and resid feed blend?
-
Is the distillate treating capacity balanced?
-
For your blend of lighter sweet crude, does it force a sweet-for-sour VGO swap?
-
Do you have the ability to turn down your SRUs to compensate?
-
Is there a sufficient reformer or purchased hydrogen available to accommodate cracking all the available AGO and VGO and saturating all the LCO?
-
How much cat feed hydrotreating capacity do you have [available or in your unit?]?
-
How much distillate and LCO treating capacity exists?
-
Do you have transportation options that will allow you to take advantage of shifts in the gasoline versus diesel price?
The shifting combinations of these factors demand continued flexibility of hydrocracker operations, if you are in a position where that spread is going to shift frequently. Again, what is common in these cases I showed and discussed is the importance of maximizing your existing assets. That is your primary concern.
PAPPAL (Valero)
I took a little different approach on this question. Many refineries do not run a single crude source; but rather, crude blends. A refiner’s crude slate can be modified; for example, a conventional domestic sweet or international light sweet barrel can be replaced by an advantaged tight oil barrel. In many cases, the refinery does not really see any negative impact on the overall hydrocracker operation.
Brant touched upon light naphtha production. To keep the refinery in naphtha balance, cutpoints on the hydrocracker or crude unit naphtha streams will be adjusted. Many light sweet refineries have traditionally cat cracked resid or used coking or deasphalting followed by FCC to convert the residual barrel. If a tight oil barrel is the primary crude to the refiner, it is quite possible that an existing deasphalter could be shut down and all the resid upgraded in the cat. So, again, crude slate and cutpoints are optimized for individual unit utilization.
In a scenario where coking is eliminated by running a tight oil barrel, if you are consuming all the resid in the cat cracker, the hydrocracker feed could be significantly easier. In that case, the catalyst selection in the hydrocracker could be tailored to give a more favorable yield slate and have a more economical solution in the hydrocracker.
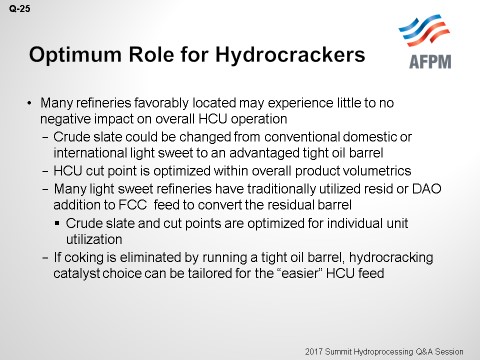
BRANT AGGUS (Becht Engineering)
There have been many refiners who have either been fortunate enough to have existing assets that have allowed them to capitalize on the U.S. shale boom or who have re-tooled to take advantage of availability of shale crudes. I will go through a few case studies to show where the hydrocracking unit fits in.
The first case study is a refinery that has multiple crude units and which, in the past, has been a purchaser of FCC feed. An increase in crude capacity to accommodate available domestic crude, coupled with the switch to resid-to-FCC operation, has allowed the refinery to become VGO-long. For this refinery, the economics of HCU/FCC gasoil split have not greatly changed, and the pursuit of volume swell is still primary. Considering this scenario, this refinery plans to increase the rate of AGO to the hydrocracking unit, move LCO to other high-pressure diesel treaters while routing purchased resid/VGO to the FCC units. This refinery is VGO-long but must trade VGO in a sweet-for-sour swap to meet the minimum capacity of its SRUs.
In a second case, a VGO-short refiner opted to shift LCO to the hydrocracker unit and push AGO back the FCC to accommodate a light crude slate. Increased distillate yield has backed LCO out of other treaters and moved the HCU to being primarily a saturation unit.
In a third case, also switching to a lighter crude slate largely with shale crude, another refiner opted to convert its hydrocracker into a diesel hydrotreater. This decision was driven by the distillate production with the new crude blend, lack of hydrogen availability, and the capital cost required to build a steam methane reformer. This refiner found him/herself in a position where the refinery would be hydrogen-short if it continued to hydrocrack.
Other possible solutions exist. A HCU revamp to LCO-X™ technology may make sense for some refiners. Switches to lighter shale crudes are typically accompanied by a large increase in light straight-run make, which leaves many refiners octane-short. Refiners with a long-term gasoline to diesel advantage may prefer this option.
Another option, specifically available to refiners with a two-stage hydrocracker unit, is to convert the first stage hydrocracking reactor to a treat-only reactor and then split the interstage product between the FCC and second-stage hydrocracker reactor. This modification offsets the potential feed sulfur increase from the new VTB portion of the FCC feed, thereby preventing the need for cat gasoline treater revamp.
There is no one solution; in fact, the hydrocracker’s place in a refinery’s switch to resid-to-FCC depends on many factors:
-
Is there a crude unit capacity increase project accompanying the lightening slate? (This is often the case as shale crudes, in particular, can be highly advantaged barrels.)
-
Can FCC severity be adjusted to balance LCO make with a new VGO/resid feed blend?
-
Does the (typically sweeter) lighter crude blend force a sweet-for-sour VGO swap for SRU turndown?
-
Is there sufficient reformer or purchased H2 available to accommodate cracking all available AGO/VGO and LCO?
-
How much cat feed hydrotreating capacity is available? How about virgin diesel and LCO?
-
Does the refinery have transportation options that allow it to easily take advantage of gasoline versus diesel price spreads? This situation demands continued flexibility of HCU operation.