Question 25: For refinery complexes considering grassroots or brownfield expansion of gas oil conversion capacity, what are your typical capital expenditure (capex) costs and relative refinery margin improvement between FCC (fluid catalytic cracking) and hydrocracking? What are the key technology features that impact your economic decision? What are the crucial considerations that, if they include both technologies, to allow for future integration, especially around the changing gasoline/diese
JEFFREY MUELLER (Marathon Petroleum Company)
Capex (capital expenditure) costs are very unique to each specific refinery. Offsite investments (tankage, utilities, etc.) and downstream unit configurations are very significant and must be considered when determining an investment strategy around an FCCU versus an HCU (hydrocracker unit).
One of Marathon’s engineering contractors provided the following ISBL (inside battery limits) costs per barrel for a grassroots FCCU versus an HCU:
FCC: $6,200/bbl(barrel) to $7,000/bbl
HCU: $7,200/bbl(Partial Conversion) to $9,000/bbl(Full Conversion)
A couple important points:
*FCCU products may need to undergo further processing to remove sulfur to meet specs. This is not included in the costs.
*The above-quoted values are for units in the 50 to 70 mbpd range.
In general, Marathon’s economic viewpoint is that hydrocrackers have better projected margins going forward than FCCUs, as they maximize higher valued ULSD over gasoline and have higher volume expansion (see Figure 1). This is driven by many factors mentioned in the primary response and is particularly attractive when ULSD is strong relative to gasoline and when natural gas or hydrogen) is inexpensive. Each company has a different viewpoint on this topic, so the opinion will vary somewhat across the industry.
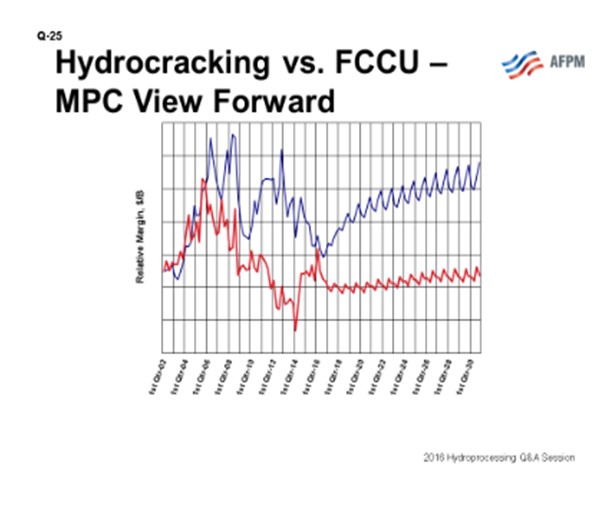
HOWARD WU (Haldor Topsoe, Inc.)
Selection between FCC and hydrocracker as the conversion process for gas oil requires detailed analysis of feed qualities, desired product slate and properties, and local economics.
An FCC unit can, in general, process a wide range of materials including gas oil, deasphalted oil, and residual oil. On the other hand, the hydrocracker, while it can also process a wide range of materials, operates better with a cleaner feed.
FCC is a thermal, catalytic carbon-rejection process, and it naturally produces lower C5+liquid yields with lower product qualities than hydrocracking, which is a high-pressure, hydrogen-addition process. Typically, an FCC unit, for a maximum gasoline mode, would make 4 to 7wt% dry gas, 25 to 30 vol% (volume percent) LPG, 55 to 65 vol% gasoline, 15 to 20 vol% LCO, and 4 to 10 vol% decant oil. All of these FCC product streams require further cleanup and processing to become usable materials. The flue gas needs to be scrubbed to meet the SOx (sulfur oxide) and particulate emission requirements. The gasoline product needs to be hydro treated for sulfur removal. The cycle oil, because of its high density and low cetane index (typically low 20s), needs to be severely upgraded in a hydro treater to be a usable diesel blending stock. The decant oil, because of its high density and low hydrogen content, often can only be used as fuel oil. However, a specific advantage for FCC unit is that it could produce a large number of light olefins for alkylation or Petro chemical applications.
Hydrocracking is a versatile process; and with a proper design, the unit can achieve almost 100% conversion with flexibility to swing between naphtha-focused or diesel-focused operation, depending on the need. Typical yields for a full conversion hydrocracker using a flexible catalyst to swing between naphtha and diesel modes are: 0.2 to 0.4 wt% dry gas, 6 to 13 vol% LPG, 28 to 48 vol% naphtha, and 54 to 85 vol % jet and diesel combined. If the unit is designed to make maximum naphtha, the total naphtha yield could be as high as 115 vol%. Light naphtha from a hydrocracker often can be blended directly into gasoline pool. The heavy naphtha is typically sent to the reforming unit for an octane boost. The reformer generates hydrogen, but a hydrogen plant is likely required to supplement the hydrogen need of the hydrocracker. The jet and diesel products require no further processing; they often exceed the smoke point and cetane requirements, respectively.
Once the product slates for the FCC and hydrocracking processes are known, the economic advantage for one process versus the other can be calculated. The following chart (data from the United States Energy Information Administration) can be used as a reference with regard to the cost and prices of the transportation fuels:
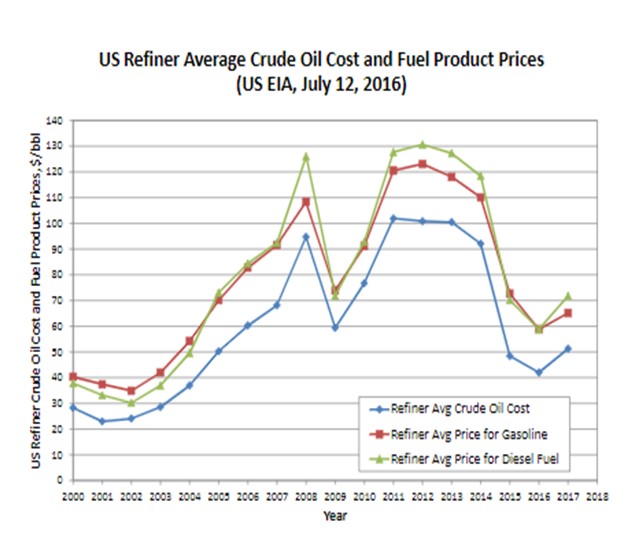
It can be seen that from years 2005 to 2014 diesel to crude oil has a larger spread than gasoline to crude oil; for year 2015 the trend had reversed; and for the current year 2016, the two seem to be equal. The EIA (Energy Information Administration) is currently predicting price advantage for diesel for 2017. Several refineries have recently reported that between summer and winter, there is a significant difference in profit between making gasoline and making diesel fuel. Therefore, without knowing what the future would hold, it seems that having flexibility to make more naphtha or diesel would be important to a refiner. The importance of operating flexibility gives an advantage for the hydrocracker over the FCC because of its greater ability to swing between these two operating modes.
Estimating required expenditure for erecting an FCC unit or a hydrocracker would require detailed analysis. In general, a hydrocracker would cost approximately 30% more than an FCC unit. However, for an FCC complex, having a pre treater or a post-treater (or both, in some cases) most likely would be required given the upcoming gasoline tier 3 ultra-low sulfur specification (10 ppmw). In addition, as mentioned above, the cycle from the FCC unit will need to be processed before it can become a usable product. Considering these pretreat and/ or post-treat requirements, an FCC complex may cost the same or more than a hydrocracker complex with hydrogen plant and naphtha reforming capacity.
If a refinery has both an FCC unit and a hydrocracker, it will obviously have great flexibility to shift between diesel and naphtha productions. Shifting feedstock between these two units automatically changes the naphtha-to-diesel yield ratio. Each unit can be adjusted to maximize production of the desired product. This adjustment is done through changes in cutpoints, catalyst types, and operating conditions. In addition, the cycle oil from the FCC unit can be processed in the hydrocracker and the unconverted oil from the hydrocracker can be sent to the FCC unit. For design, all these aspects need to be considered.