Question 24: For refiners who have naphtha splitter columns, either upstream or downstream of a hydrotreater, how many of these towers experience overhead corrosion issues? Has oxygen played a role in any experienced corrosion? What solutions exist to mitigate the issues?
GROPP (GE Water & Process Technologies)
As a preface to my answer, I thought it important to define what we see as a splitter versus a stripper. To us, a naphtha splitter is a simple fractionator vessel. It takes naphtha and separates it into a light fraction that goes to gasoline blending and a bottom, heavier fraction that goes to catalytic reforming. A naphtha stripper, on the other hand, is a fractionator with a reboiler that produces the final desulfurized naphtha product from the naphtha hydrotreater unit.
With that in mind, GE does not have a lot of experience with oxygen-related corrosion issues in naphtha splitter units upstream or downstream of hydrotreaters. We do have a significant amount of experience with corrosion control in the overhead of naphtha strippers. Typically, the root causes of corrosion are associated with ammonium bisulfide and ammonium chloride deposition.
Solutions for ammonium chloride and bisulfide deposition include waterwashes and metallurgy. In some cases, filming inhibitors with good salt dispersion properties can be used to form a protective layer on the metal surfaces and disperse salts. With the waterwashes sometimes comes oxygen from oxygen-contaminated water sources. The oxygen can cause corrosion problems. In these cases, filmers with low emulsion-forming tendencies can establish a film on the metal surface to protect it from the oxygen and oxygen-related corrosion.
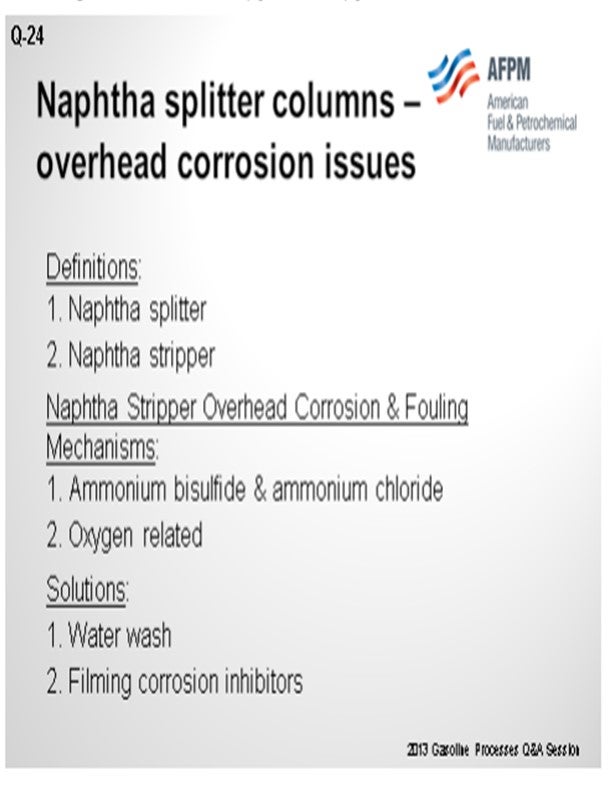
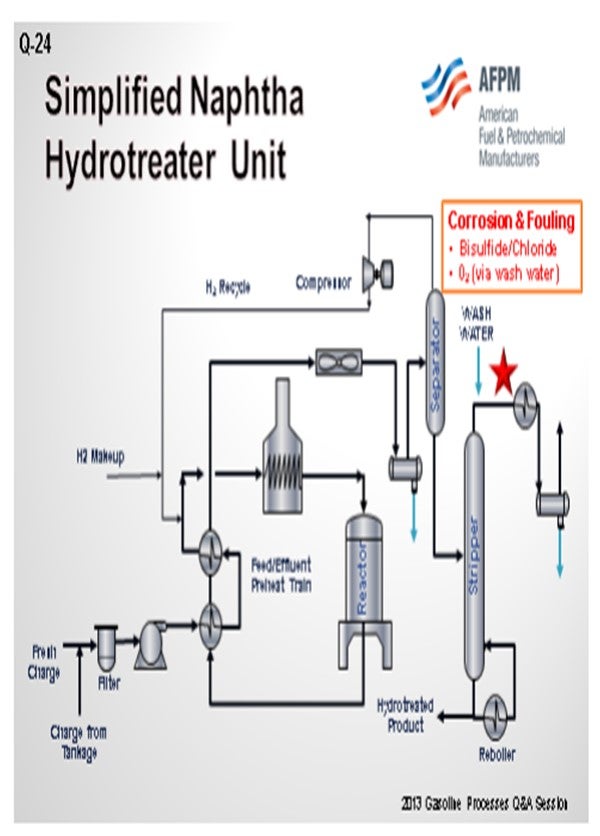
STREIT (KBC Advanced Technologies, Inc.)
Probably one of the reasons GE does not have a lot of experience with the issues in naphtha splitters is because they typically do not have much corrosion. That being said, corrosion can occur whether the splitter is upstream or downstream of a naphtha hydrotreater. It will typically involve water, chloride, ammonia, H2S, oxygen, or some combination of those substances. Normally, it is water-based and H2S-based corrosion if it is occurring.
The main key to making sure that you do not have corrosion in these towers is to operate those splitter towers, which Ron just mentioned, correctly upstream, whether on the crude unit or after the reactors on the naphtha hydrotreater. As long as those are being operated properly, all of your corrosive, or the majority of your corrosive, materials should go overhead where they can be handled to avoid leaving you with the problem at the naphtha splitters.
One issue that can be a problem is that oxygen can get into material in tanks. Ideally, the naphtha should not be run down to a tank. Obviously, that is not always realistic; so if you do run it to a tank, you should have a floating-roof or fixed-roof tank with a nitrogen blanket. However, a fixed-roof tank with a nitrogen blanket does not always keep the oxygen out of the naphtha, especially if you pull hard on the tank. You may still get some oxygen intrusion into the tank. Putting an oxygen stripper upstream of the naphtha splitter can help to remove any oxygen that was able to get into the naphtha. You will see those on naphtha hydrotreaters every once in a while. But in general, it is not usually a big enough problem to cause worry.
In some cases, the amine injection into the naphtha splitter overhead, which Ron just discussed, can create compounds that get out of the bottom of the stripper tower and get into the splitter. When these compounds hit the hot tubes of the splitter reboiler, they cand potentially cause some corrosion. So, make sure that by treating upstream, you are not causing problems downstream a crack back into ammonia and H2S. The ammonia and H2S can move back up the splitter tower into the overhead.
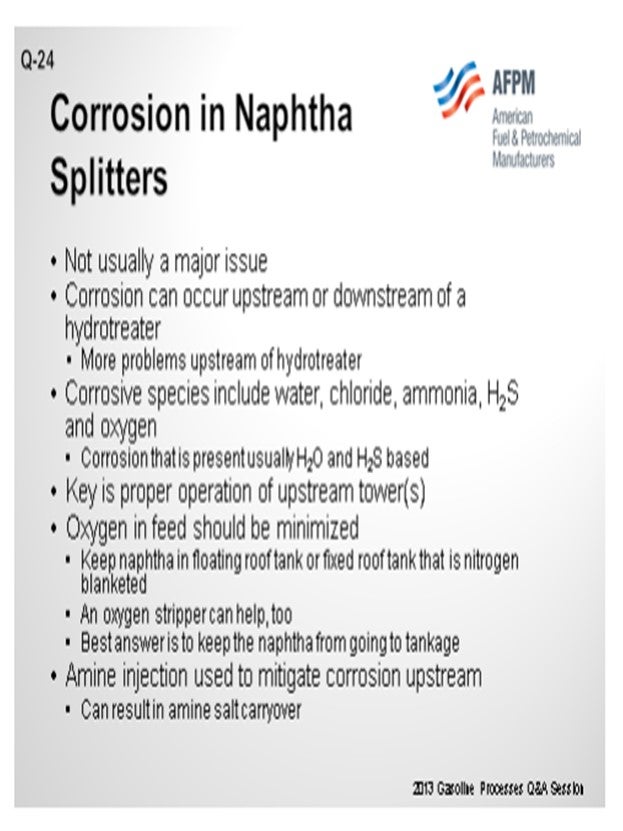
RONALD GROPP (GE Water & Process Technologies)
As a preface to our response to this question, we want to state that we believe it is important to establish our interpretation of the term “naphtha splitter” versus the more common “naphtha stripper” unit.
• Naphtha Stripper: A stripper fractionation tower with a reboiler that produces the final liquid desulfurized product from the hydrotreater unit.
• Naphtha Splitter: The bottoms product from a debutanizer tower is routed to a naphtha splitter tower where it is fractionated into an overhead light naphtha product and a bottoms heavy naphtha product. The light naphtha is routed to the gasoline blending pool, and the bottoms product is fed to a catalytic reformer. There are also “naphtha splitters” in diesel hydrotreater units where the overhead of the tower is a gasoline range material that is sent to a catalytic reformer and the bottoms product is routed to the diesel blending pool.
With these unit designations in mind, GE has no experience with oxygen-based corrosion control in naphtha splitter units either upstream or downstream of hydrotreaters.
GE does have significant experience with corrosion problems and corrosion control solutions in naphtha strippers. We have experienced two primary situations:
1. Ammonium Bisulfide and Ammonium Chloride Corrosion and Fouling: A major contributor to corrosion and fouling in naphtha stripper overhead systems is ammonium bisulfide. In some cases, chloride contamination can result in ammonium chloride deposition and associated underdeposit corrosion. It is normal to control ammonium bisulfide and/or ammonium chloride corrosion and deposition with combinations of waterwashes and metallurgy. Filming corrosion inhibitors with good salt dispersion properties are also used to form a protective layer on the metal surfaces and disperse salts.
2. Oxygen-Related Corrosion: Another contributor to corrosion in naphtha stripper overhead systems is oxygen. The primary source is oxygen-laden overhead washwater. If oxygen is available to participate in corrosion mechanisms, filming corrosion inhibitors have helped mitigate the corrosion issues. The filming corrosion inhibitors are designed for effectiveness in oxygen-containing environments and provide a physical barrier to oxygen contact with the equipment metal surfaces. The inhibitors used should have low emulsification tendencies to minimize potential downstream water haze concerns in the gasoline blending pool.
CRAIG MELDRUM (Phillips 66)
Phillips 66 has seen corrosion issues on the overheads that have been attributed to chlorides and amine salts coming from poor upstream water separation. Focus on making sure feeds to the splitters are dry. That usually takes care of most of the issues, but it is often easier said than done.
ERIC STREIT (KBC Advanced Technologies, Inc.)
Corrosion can occur in naphtha splitters either upstream or downstream of a hydrotreater, although it is usually not a major issue. On splitter towers upstream of a hydrotreater, any number of potential sources of corrosion can exist including water, chloride, ammonia, and oxygen. On splitter towers downstream of a hydrotreater, the contaminants are more limited in number.
Some units have amine injection to these towers. However, this should not be necessary if the upstream tower operations are carefully monitored. The upstream stripper/debutanizer should be removing most contaminants if they are operated correctly. The problem with amine injection to the naphtha splitter is that nitrogen species can get into the light or heavy naphtha as amine salt carryover. If the heat source to the splitter is too hot, some H2S may be cracked out.
The best way to protect the naphtha splitter is to run the upstream towers to the correct temperatures to control H2S and water in the bottoms. Few folks do that and wait for naphtha splitter product issues such as drier or sulfur trap problems on the isomerization unit feed.
Oxygen can play a role upstream the hydrotreater if it has been picked up during storage or transportation. Corrosion inhibitors and antifoulants can help reduce the effect of oxygen. Some refiners have installed an oxygen stripper to remove the oxygen. Corrosion can also be caused by chloride contamination due to organic chlorides, salts from the CDU (crude distillation unit) or HCl (hydrogen chloride) in the recycle hydrogen. Corrosion inhibitors can help control the corrosion caused by HCl and NH4Cl (ammonium chloride).
PAUL FEARNSIDE (Nalco Champion Energy Services)
As crude unit throughputs have been increased over the years, the reflux drum residence time has correspondingly decreased. This is resulting in “wet” naphtha leaving the unit and feeding the naphtha splitter column. This wet naphtha contains all the acidic species normally associated with crude unit overhead corrosion. Taking steps to dry out the naphtha can go a long way towards solving/eliminating the splitter column corrosion. Increasing the internal naphtha draw standpipe height to allow more residence time for the water to settle, installing water coalescers, and utilizing emulsion breakers have all been used to help dry out the naphtha.
GARY HAWKINS (Emerson Process Management)
Emerson Process Management offers both non-intrusive and process wetted online corrosion measurement technologies to monitor corrosion due to aqueous or organic methods. The correlation of corrosion rates with other process measurements can assist with determination of causes and effectiveness of mitigation techniques.