Question 23: What is the impact of HPNA (Heavy PolyNuclear Aromatics) on hydrocracking catalyst activity, stability. and yield selectivity?
Kaspar Vogt (Albemarle)
The impact on hydrocracking catalyst deactivation and yield selectivity due to precipitation of Heavy PolyNuclear Aromatics (HPNA) is typically based on several criteria.
- Unit configuration
- operating in recycle mode
- operating in once through mode
- Conversion level and therefore unconverted oil bleed rate from the unit
- Feed type and feed properties
- Catalyst type
HPNA FORMATION
The formation of PNA's is an undesirable side reaction that occurs in hydrocrackers. The HPNA's are generated by three primary mechanisms:
- by condensation of two or more smaller PNA's present in the hydrocracker feed;
- by dehydrogenation of larger hydro aromatic cyclic systems; or
- by cyclization of side chains onto preexisting PNA's followed by dehydrogenation.
Dehydrogenation is more favored as reactor temperature increases. Operating at the lowest possible temperature will best manage the HPNA formation.
In the first pass through the reactor, some HPNA's are produced from the smaller PNA's that are present in the feed. The PNA's are preferentially adsorbed on the catalyst because they are more polar than are most of the other feed components. Their polarity increases as their side chains or saturated rings substituents are removed or dehydrogenated (aromatized) in the process. This removal of some side chains further increases the tendency of the HPNA's to adsorb and condense to form larger HPNA's. Further condensation of the HPNA's represent the last steps in catalyst coking.
The HPNA's are high boiling and thus concentrate in the fractionator bottoms stream, which in recycle hydrocracking is routed back to the reactor section. Eventually, the equilibrium concentration of the HPNA's is reached in the reactor effluent and recycle liquid. The HPNA's build up to the limit of their solubility at temperatures used for the condensation and separation of the reactor products.
The formation of HPNA's depends on many factors. The amount and type of PNA precursors are normally related to feedstock composition and boiling range.
Heavier feeds contain more HPNA precursors. In addition to high endpoints, HPNA precursors may also be indicated by high levels of olefins, aromatics, asphaltenes, or heteroatoms in the feed.
Operating severity also has an effect. As conversion increases, the concentration of PNA's with five or more rings increases. With catalyst deactivation, higher reactor temperatures are required, and HPNA levels increase. This temperature effect becomes more significant as conversion approaches 100%.
Catalyst selection also impacts the amount of HPNA generation. In first stage applications using base metal catalysts, pilot plant studies indicate that as the catalyst activity and hydrogenation function increase HPNA generation decreases.
HPNA IMPACT ON EQUIPMENT
HPNA precipitation in equipment downstream of the reactor depends on the concentration of HPNA and operating temperature. Generally we expect the effects of HPNA to become significant when the concentration increases above the range of 50 to75 ppm. As concentrations increase with low unconverted oil bleed from the unit, the impact to equipment, catalyst activity and catalyst deactivation becomes more prominent. Precipitation temperature generally begins to occur between 300 deg F and 350 deg F depending on the concentration. This will impact equipment such as the reactor effluent air condenser (REAC) and exchanger equipment in recycle oil or unconverted oil service.
HPNA IMPACT ON CATALYST DEACTIVATION, YIELD SELECTIVITY
The deposition of HPNAs diminishes the hydrogenation function as evidenced by loss in saturation activity. In other words, as condensation reactions increase and coke formation accelerates, catalyst deactivation accelerates. The loss of the hydrogenation activity or metal function impacts product quality.
As activity is lost, the reactor catalyst temperature is increased and in order to continue the same product conversion, the deactivation rate increases. The increased catalyst temperature, depending on the type of hydrocracking catalyst utilized, generally results in a significant shift in heavy yield selectivity. Increased catalyst deactivation resulting from condensation reactions of HPNA to coke accelerates the deactivation, and therefore increases catalyst temperature to keep desired economic conversion to products. By employing high zeolite catalyst systems (rather than lower zeolite and amorphous catalyst systems) selectivity shifts as much as 2% by volume have been observed in commercial applications.
Generally, as the UCO bleed stream increases and HPNA is purged from the system, in most cases, catalyst activity will typically return, provided that condensation reactions have not progressed to the point that coke deposition is affecting catalyst activity.
Raj Patel (Haldor Topsoe, Inc.)
HPNA’s are high molecular weight condensed aromatic molecules containing multiple aromatic rings with boiling above 500°C. Analyses of HPNA deposits on heat exchanger and aircooler surfaces show compounds with up to 30 aromatic rings are present. Once these compounds are formed by undesired side reactions in the hydrocracker, they are virtually impossible to convert in the hydrocracker. If not removed from the hydrocracking reaction system, they will continue to build up in the recycle oil stream.
The HPNA in the recycle oil stream, typically in the several hundred ppm range, have an adverse impact on the catalyst primarily in the form of catalyst stability. The HPNA molecules will lay down as coke and cause rapid deactivation of the catalyst. The yield selectivity is impacted as a result of the higher required reactor temperatures as the catalyst deactivates.
Topsoe has studied in detail the impact of HPNA on catalyst stability in our pilot plants. Results of some of the testing is provided below. Two tests are shown. The HPNA concentration is allowed to build up in Test 1 while it is controlled in Test 2 as seen in Figure 1. Figure 2 shows the catalyst activity over time for the two tests. The catalyst deactivation is very rapid for Test 1 where HPNA are allowed to build up and is under control when HPNA are not allowed to build up.
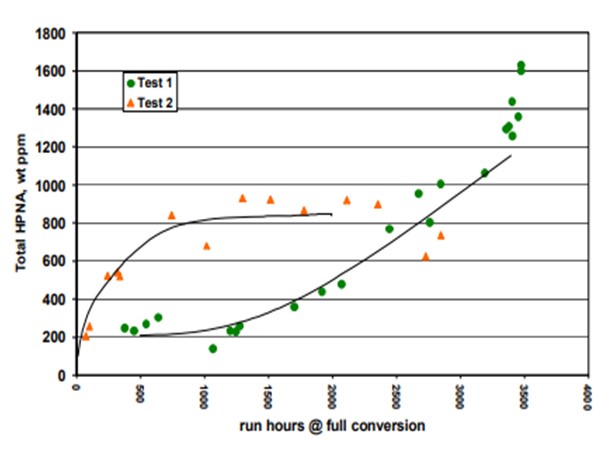
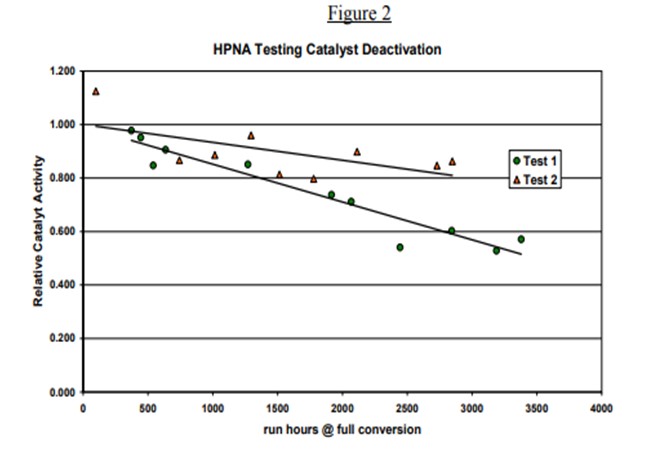
Haldor Topsoe employs a number of approaches to both minimizing the impact of HPNA on the catalyst and equipment and also minimize the need for unconverted oil (UCO) purge and the corresponding loss of product yield. The key design elements are listed below:
• Increased hydrogen partial pressure will suppress HPNA formation. Therefore, the selection of system pressure must be economically balanced with the desired overall conversion in the hydrocracker.
. • The use of catalyst with excellent hydrogenation activity in both pretreatment and hydrocracking service to saturate and convert HPNA precursors and thereby minimize the formation of HPNA.
• The use of a hot high-pressure separator in the reactor section will minimize the possibility of heat exchanger fouling due to HPNA precipitation as the reactor effluent is cooled.
Haldor Topsoe has come up with a new revolutionary process technology to control HPNA build up while minimizing the loss of bleed. This process technology consists of a steam stripper utilizing the existing steam supplied to the fractionator. The quantity of steam is relatively large in comparison to the small quantity of unconverted oil to the stripper. This provides the driving force required to vaporize up to 80% of the oil to the stripper. The HPNA that cause deactivation of the catalyst are high boiling and are not vaporized in the stripper and are eliminated in the 20% bottoms stream. The bleed rate required to control the HPNA is thus reduced to 20% of the original bleed rate. The payback for Topsoe’s unique process technology to control HPNA is typically less than six months.