Question 23: What are some options for increasing the cetane index (CI) of diesel to more easily meet export market requirements?
CARLSON (Criterion Catalysts & Technologies)
As we are short on time, I will reduce my response and point you to the Answer Book for detailed coverage of this question.
Cetane improvement chemistry mechanisms available to us are aromatic saturation and naphthenic ring opening (hydrocracking), both of which allow us to further take advantage of low-cost hydrogen to provide cetane upgrades and liquid volume gains.
Many refiners in the Americas process challenging crudes and incorporate significant 650+ conversion processes that result in high aromatic/low cetane diesel components. ULSD hydrotreaters that were designed or upgraded during the preparation for clean fuels productions already perform a significant cetane upgrade via aromatic saturation and density shift as they remove the contaminant sulfur and nitrogen. Many units’ designs now have the capability of furthering their level of performance via “drop-in” solutions utilizing recent catalyst technologies. By combining catalyst advances and improved reactor internal designs, today’s units have the potential for cetane improvement upgrades that may provide export options when feedstock segregation is practiced. By maximizing hydrogenation with conventional catalysts, product tends to contain a high concentration of monoaromatic molecules that require a higher level of effort to further saturation or enable ring opening cetane upgrades.
Aromatics saturation (ASAT) provides cetane improvement while maximizing diesel yield. The lead beds of an EAS (enhanced aromatic saturation) unit are used to remove organic sulfur and organic nitrogen down to ULSD levels and temperature profile management maintains the final catalyst bed in the optimal temperature range for aromatics saturation. EAS is typically performed in high pressure units with high H2 circulation that have a favorable hydrogenation environment.
Selective ring opening (SRO) provides cetane improvement while managing/minimizing H2 consumption. An SRO catalyst system is typically 80% to 90% hydrotreating catalyst and 10% to 20% mild hydrocracking catalyst. SRO utilizes temperature profile management to maintain the final catalyst bed within the optimal temperature range to ensure sufficient ring opening and achieve the desired product cetane level while minimizing excess cracking to naphtha boiling range materials. SRO is typically used in moderate to high pressure units, but it has been successfully applied in low pressure units. SRO has the advantage of utilizing base metal catalysts and can be implemented in single-stage units. Operating a unit in SRO mode will result in reduced diesel yield as compared with ASAT.
The last option is noble metal (NM) saturation. Essentially, complete aromatics saturation can be achieved with noble metals catalysts, even at pressures as low as 450 psig (30 bar). NM catalysts are highly sensitive to organic S (sulfur), organic N (nitrogen), H2S, and NH3, so they must be used in the second stage of a two-stage unit. The two-stage requirement for NM ASAT makes it a more capital-intensive and operationally complex than EAS and SRO processes.

OHMES (KBC Advanced Technologies, Inc.)
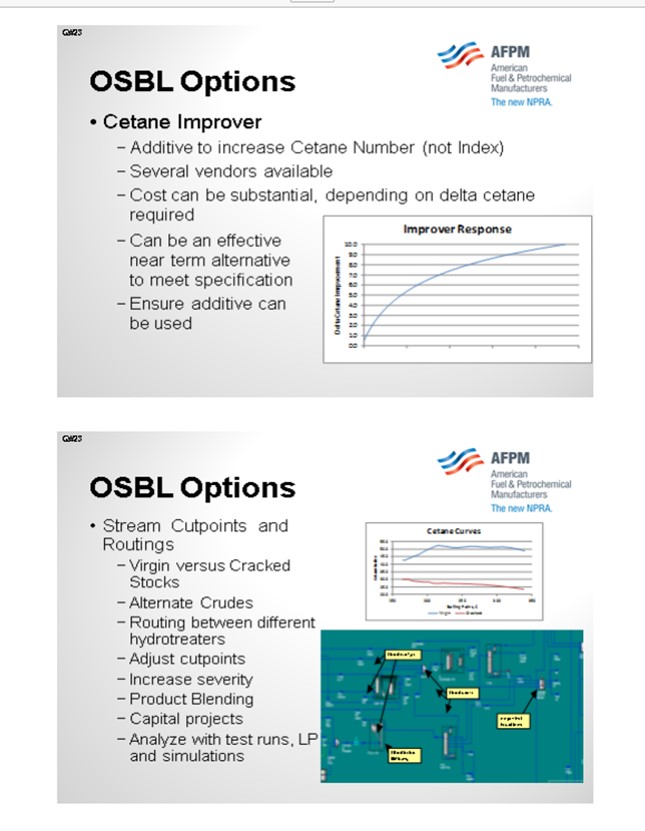
KEVIN CARLSON and LARRY KRAUS (Criterion Catalysts & Technologies)
As the question implies, there are opportunities available to increase product margins by supplying ULSD into high demand export markets. While the realized margins can be significant, tighter cetane specifications in these markets typically require U.S. refiners to further upgrade their products to meet those market needs.
A bit of background: The question mentions cetane index (CI); however, many of the specifications in question are, in fact, cetane number. Both measures refer to the ease of combustibility in a diesel engine. Cetane number (CN) uses a test engine to measures the actual time delay between the start of the fuel injection and the ignition of the fuel in comparison to two standards; n-hexadecane (cetane) with a number of 100 and heptamethylnonane with a number of 15. The measured cetane number of the analyzed product is that which matches the combustion characteristics of a mixture of the two standards.
Cetane index is a calculated value based upon density and distillation. These methods are used to estimate the combustion characteristics for blended diesel fuel products. It does not always compare favorably for a wide range of component blend stocks, nor does it respond to the presence of improver additives. Based upon offsets between values, many regions have different specifications for each.
The current standard for diesel sold in European Union, Iceland, Norway, and Switzerland is set in EN 590, with a minimum cetane index of 46 and a minimum cetane number of 51. In North America, most states adopt ASTM D975 as their diesel fuel standard which includes the minimum cetane number of 40, with typical values in the 42 to 45 range.
In order to improve the CI/CN of a diesel stream, it is useful to understand the chemistry involved. Cetane number varies depending on the hydrocarbon structure of the diesel boiling range molecule. Of the molecules we deal with in distillate production, the highest cetane molecules are the straight chain paraffin’s that have CN greater than 75. Isoparaffins can have a wide range of CN (between 10 and 80) depending on the degree of branching of the molecules. Those with few longer side chains will have higher values while those with many short side chains will have lower values. Alkylcyclohexanes can vary between 60 to 85), depending on mol weight and side-chain decorations. Alkylbenzenes range from 30 to 65, depending on level of aromaticity and again, side chain structure. Multi-ring species typically have low cetane values. Naphthlenes have very low cetane number values in the 0 to 20 range, while decelins and tetralins are in the 10 to 20 and 30 to 40 range, respectively. The low cetane values of multi ring naphthenes and naphthenoaromatics limits the cetane upgrading of LCO through aromatics saturation alone. The high cetane values of alkyl cyclohexanes and alkyl-benzenes illustrate the value of ring opening for cetane improvement.
Based on this understanding of cetane chemistry, we have aromatic saturation and naphthenic ring opening (hydrocracking) available to improve product cetane properties and volume swell and further take advantage of low-cost hydrogen.
Many refiners in the Americas process challenging crudes and incorporate significant 650+ conversion processes that result in high aromatic, low cetane LCO diesel components. ULSD hydrotreaters that were designed or upgraded during the preparation for clean fuels productions already perform a significant cetane upgrade via aromatic saturation and density shift as they remove the contaminant sulfur and nitrogen. Many unit designs now have the capability to further their level of cetane upgrade/volume swell performance via “drop-in” solutions utilizing recent catalyst technologies. By combining catalyst advances and improved reactor internal designs current units have the potential of cetane improvement upgrades that may provide export options. Maximizing hydrogenation with conventional catalysts and hydrotreating processes results in products with high concentrations of mono-aromatic molecules. To upgrade these molecules to higher cetane species requires additional deep aromatics saturation or ring opening.
The following figure and table outline the impact of applying cetane improvement mechanisms on a low cetane naphthalene species common in cracked distillate feeds. In the removal of heteroatom contaminants via indirect hydrogenation reactions, significant di+ saturation provides a sufficient cetane gain enabling the production of blended EPA ULSD for most refiners. However, to lift the pool into the levels required for the export market the application of enhanced aromatic saturation (EAS), selective ring opening (SRO), or noble metals aromatic saturation (NM ASAT) is typically required.
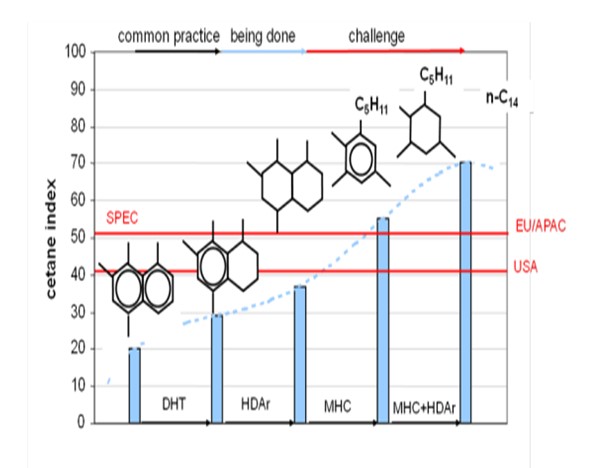
The application of each of these process approaches have considerations that may influence the technology selection for any given facility depending on required level of uplift and process design capability available.
Enhanced Aromatic Saturation (EAS)
Aromatics saturation (ASAT) provides cetane improvement while maximizing diesel yield. Enhanced Aromatics Saturation (EAS) utilizes temperature profile management to maintain the final catalyst bed in a multiple bed unit in the optimal temperature range for aromatics saturation. This allows the desired level of ASAT to be maintained throughout the catalyst cycle.
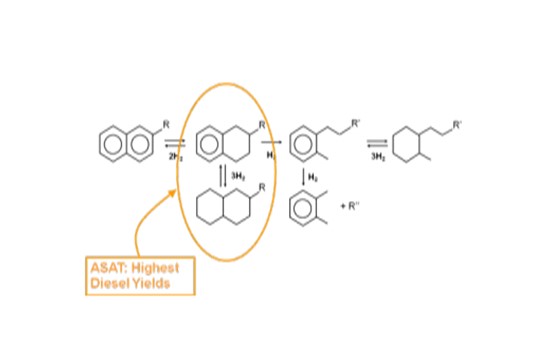
The lead beds of an EAS unit are used to removed organic sulfur and/organic nitrogen down to ULSD levels. This creates an inhibitor-free environment in the final bed that maximizes the ASAT performance of the catalyst. EAS is typically performed in high pressure units with high H2 circulation that have a favorable hydrogenation environment. In order to implement EAS, a unit must have sufficient quench to maintain the final catalyst bed in the desired temperature range throughout the cycle. EAS has the advantage that it utilizes base metal catalysts and can be implemented in single stage units. EAS can improve mono-aromatics saturation but cannot achieve the deep mono-aromatics saturation possible with noble metal ASAT.
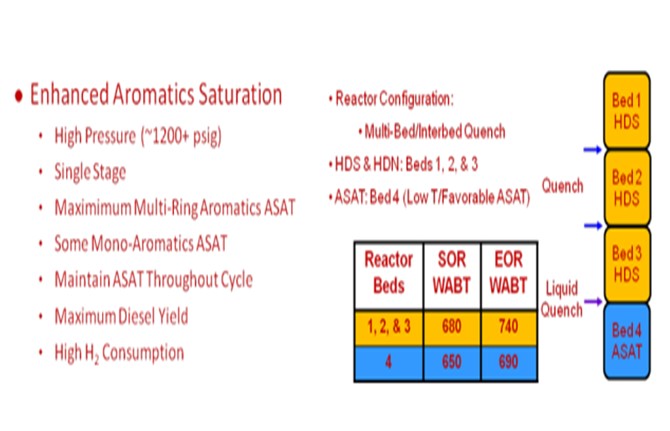
Selective Ring Opening (SRO)
Selective ring opening (SRO) provides cetane improvement while managing/minimizing H2 consumption. SRO provides greater cetane number improvement per unit of H2 consumption than ASAT. This makes SRO a means to upgrade product cetane in H2-constrained units. An SRO catalyst system is typically 80% to 90% hydrotreating catalyst and 10% to 20% mild hydrocracking catalyst (MHC). The MHC catalyst is located in the final bed of the reactor and is followed by a post-treat hydrotreating catalyst bed to prevent mercaptan formation. For SRO applications, the MHC catalyst used typically has very low cracking activity to minimize secondary cracking to naphtha.
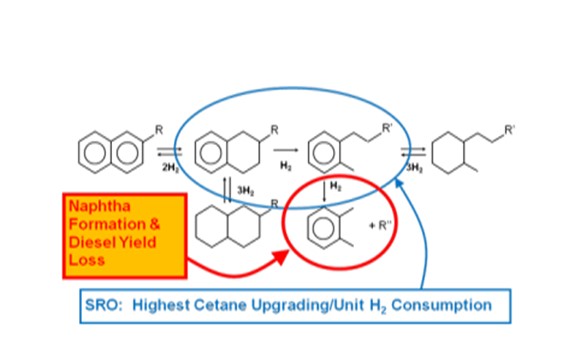
SRO utilizes temperature profile management to maintain the final catalyst bed in a multiple bed unit within the optimal temperature range to ensure sufficient ring-opening to achieve the desired product cetane level while minimizing excess cracking to naphtha boiling range materials. The lead beds of an SRO unit are typically used to removed organic sulfur and/organic nitrogen down to ULSD levels. This creates an inhibitor-free environment in the final bed that maximizes the ring opening performance of the catalyst and minimizes temperature requirements in the MHC bed. The lead beds of a unit operated in SRO mode can be operated to allow nitrogen slip to the MHC bed to help manage cracking activity.
SRO is typically used in moderate to high pressure units, but it has been successfully applied in low pressure units. SRO has the advantage that it utilizes base metal catalysts and can be implemented in single stage units. Operating a unit in SRO mode will result in reduced diesel yield as compared with ASAT. To implement SRO, a unit must have sufficient product separation/handling capabilities to manage the additional naphtha and light gas make that will be observed with this process.
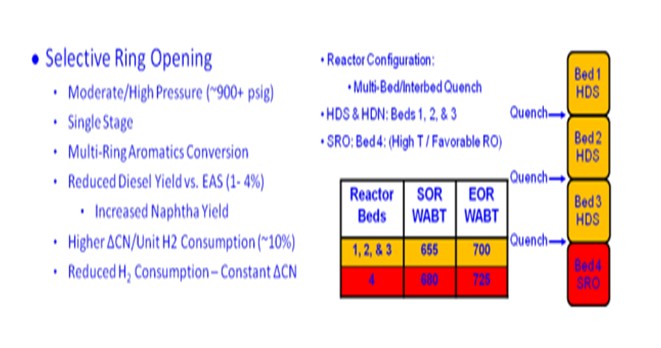
Noble Metal Aromatic Saturation (NM ASAT)
Noble metal (NM) catalysts are capable of exceptionally deep aromatics saturation because of their uniquely high mono-aromatics saturation activity. NM ASAT catalysts are a means to boost product cetane by saturating alkyl-benzene species to their high cetane alkyl-cyclohexane analogues. Essentially, complete aromatics saturation can be achieved with noble metals catalysts, even at pressures as low as 450 psig (30 bar).
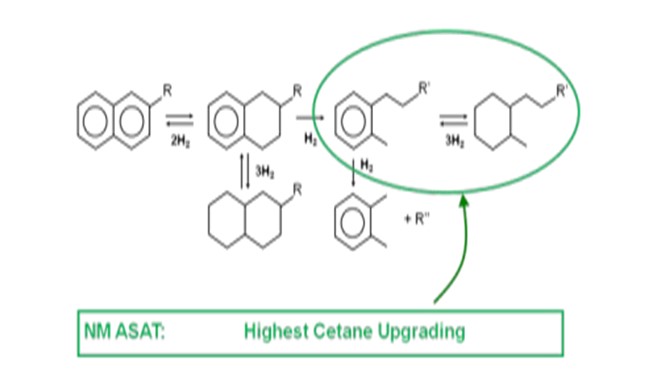
The ultra-high ASAT activity of noble metal catalysts allows NM ASAT to occur at low temperatures which maximizes diesel yield and results in very low catalyst deactivation rates. NM catalysts are highly sensitive to organic S, organic N, H2S, and NH3, so they must be used in the second stage of a two-stage unit. Reducing oil S and N to ULSD levels in the first stage of the unit and interstage separation to remove H2S and NH3 from the treat gas are both necessary to ensure low levels of catalyst inhibitors in the NM catalyst bed. Sulfur tolerant NM ASAT catalysts are available to help mitigate the effects of sulfur on catalyst performance. The two-stage requirement for NM ASAT makes it a more capital intensive and operationally complex than EAS and SRO processes.
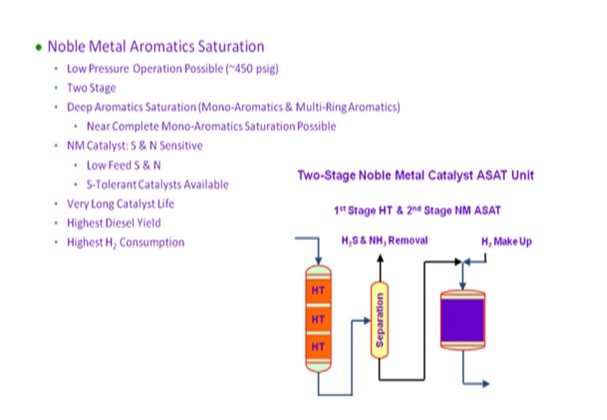
OHMES (KBC Advanced Technologies, Inc.)
In addition to the comments made by the other panelists, several OSBL options are available to improve cetane of distillate products.
Cetane Improver
One option that several refiners employ is the cetane improver. Basically, cetane improver is an additive that improves combustion, thereby resulting in a higher cetane number (cetane index remains constant, as it is a calculated property). Several vendors are available that can provide the additive.
A typical additive response curve is shown below. The amount of additive is dependent on several factors: sulfur content, target cetane number, and cetane number of the feedstock. As shown, the initial amount of additive has a large improvement to cetane and the response tapers off as the dosage increases. Therefore, though cetane improver can be effective at providing some “trim” improvement on cetane, large dosage is often cost prohibitive, with the typical cost of high dosages in the range of $0.15/bbl (per barrel) to $0.20/bbl of diesel. Finally, before using the additive, ensure that the purchaser of the resultant diesel allows the use of cetane improver additive and certify that the resultant cetane number will meet specification.
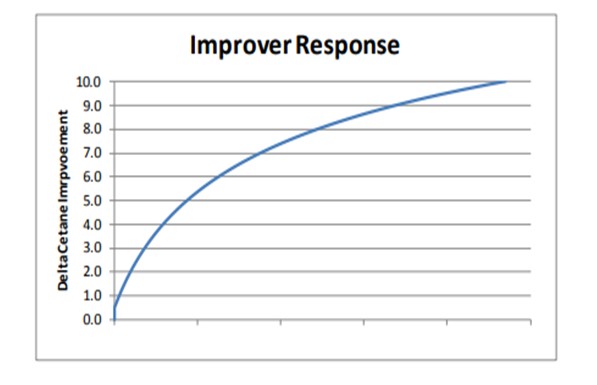
Operating Variable and Feedstock Options
Several options are available in the area of feedstock routings and cutpoints. Most refineries have several streams that are part of the diesel product pool, and each stream has its own unique cetane content and distribution. The following chart summarizes a representative cetane index curve for virgin and cracked stocks.
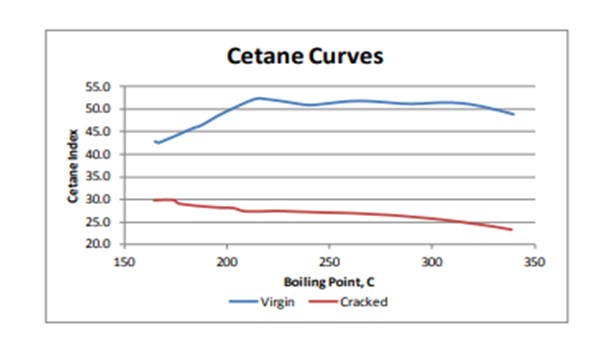
Therefore, when trying to increase cetane in the diesel product, the refiner should examine not only the stream being routed to the resulting product pool, but also review the front-end and back-end cutpoints.
To further illustrate this point, the following diagram summarizes several options to adjust and improve cetane.
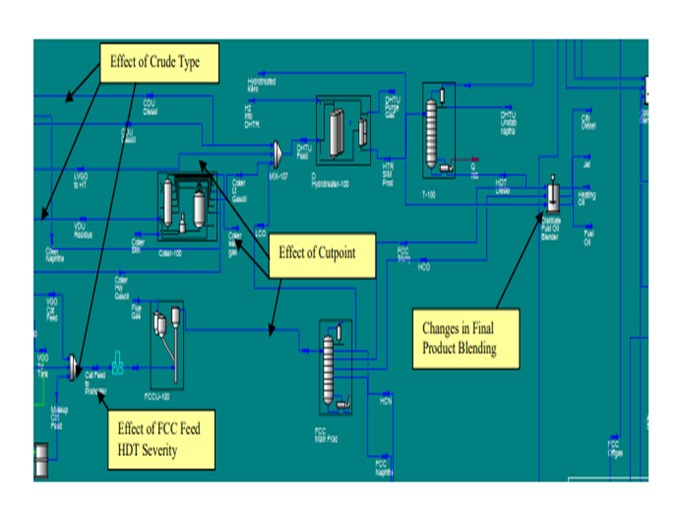
For instance:
• If several hydrotreating units are available, consider segregating the feedstock and hydrotreaters to produce a specific high cetane product.
• Consider alternate crudes that contain virgin material with higher cetane, such as shale or tight oil crudes.
• Adjust cutpoints in crude and vacuum units, FCC, coker, and FCC feed hydrotreater to improve cetane.
• Increase hydrotreater severity beyond what is needed to meet sulfur target to increase cetane improvement across the unit.
• Review product blending to determine the streams that can meet the higher cetane specification while allowing the facility to produce conventional cetane diesel.
• Examine alternate disposition for low cetane blendstocks, such as hydrocracked feed, fuel oil blending, or sales.
• Purchase high cetane blendstock, such as Fischer-Tropsch liquids.
• Consider capital project options, if economics support the upgrade. Options include building an aromatic saturation unit for low cetane blendstock or revamping existing units to allow higher severity and cetane upgrade.
To evaluate these opportunities, most refiners rely on a combination of unit test runs, LP model evaluations, and kinetic reactor models. A particularly useful tool is a process simulation that includes both kinetic models and fractionation models, such that the refiner can evaluate each of these options and determine the right operating scenario that meets the product specifications for each product