Question 22: Describe your strategies for optimizing the pretreat and cracking catalyst cycles. How does this strategy vary when operating between maximum naphtha and maximum distillate modes? How does this impact catalyst selection for the next cycle?
JEFFREY MUELLER (Marathon Petroleum Company)
Marathon Petroleum Company has adopted the philosophy of optimizing the hydrotreater and hydrocracking catalyst together as one unit. We do not measure nitrogen slip from the hydrotreater section, but rather allow the hydrocracker apparent conversion dictate adjustments to the pretreat section.
The hydrocracker is operated at temperatures as needed for a specified conversion, with individual bed temperatures varied to establish equal T (equal reaction) in each bed. An overall WABT is calculated and compared to our standard budget curve for the required cycle length. The hydrotreater reactor(s) WABTs are initially set to the budget, and then raised/lowered such that the deviation from budget on the hydrotreater is the same as the hydrocracking reactor.
For example, if the hydrocracker is operating10°F over budget and the hydrotreaters are on budget, the hydrotreater would be increased 5°F with the expectation that a reduction in slip would allow the hydrocracker WABT to be reduced and achieve the same target conversion. Successive moves (slowly, over a period of days) would be performed until the two sections are balanced. The attached graph (a fictitious example) outlines an example of this balancing.
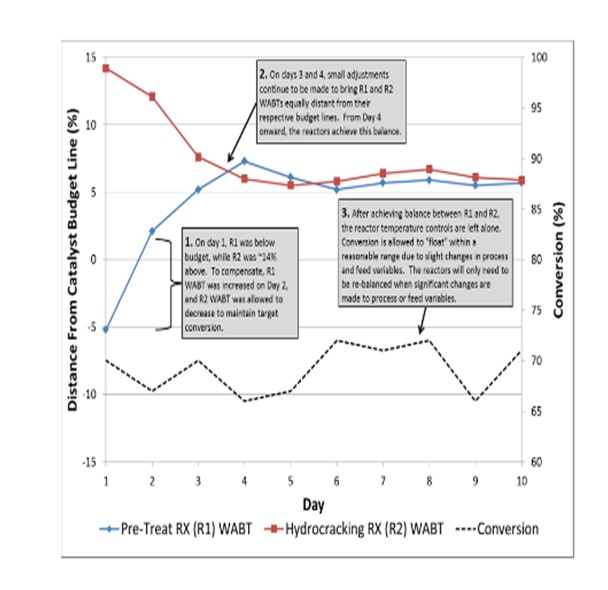
Variations in nitrogen slip due to feed composition changes, etc. will cause conversion to oscillate around an average. However, we will let the oscillations occur and not chase nitrogen slip with hydrotreater temperature. Balancing the reactors in this manner reduces the number of adjustments made throughout the run. MPC has seen those minimizing adjustments and maintaining steady-state operation results in a longer run-length, with more barrels under the curve.
There is no variance in this balanced operating philosophy when operating between max naphtha and max distillate modes. A good understanding of the business objectives of the process unit is needed to optimize the catalyst selection process for the next cycle. Many refiners choose a middle-of-the-road catalyst which will allow the unit to adapt to the volatile market requirements present in today’s business environment (swinging between naphtha/distillate modes).
DAVID VANNAUKER (Haldor Topsoe, Inc.)
Optimization of hydrotreating (HDT)/pretreat (PT) and hydrocracking (HDC) catalyst cycles begins with reactor loading design, which hinges on proposal basis parameters such as unit configuration and operating constraints, desired cycle length, feed (aromatics, distillation, sulfur, and nitrogen), conversion targets, and product selectivity/yield targets. Once the catalysts are loaded and the cycle has begun, both the HDT/PT effluent nitrogen content and the conversion from the HDC reactor are monitored to obtain the respective deactivation rates for the two reactors. Traditionally, the HDT/PT catalysts deactivates faster than HDC catalysts due toa higher coking tendency and contaminants in the feed, which must be considered. In some units, the HDC catalyst activity is sufficient to run twice as long as the HDT catalyst (i.e., changeout the HDT/PT catalyst once mid-cycle through the HDC catalyst cycle). Therefore, the optimum loading is one where both the HDT/PT catalysts and the HDC catalysts reach their end-of-run (EOR) limitations in unison (or, if possible, some multiple of HDT-to-HDC cycle lengths).
For maximum naphtha operating mode, the HDT/PT should be operated as needed to control nitrogen slip (N-slip) and the HDC temperatures should be raised to high conversion. For maximum distillate operating mode, HDT/PT should be run hard for maximum aromatic saturation (ASAT) while HDC temperatures should be run low for minimum saturation to reduce over cracking (secondary/tertiary cracking reactions) and minimize conversion.
There are three primary options for catalyst selection and the resulting operating window:
1) Select a flexible, medium-zeolite cracking catalyst and achieve the change of product slate through the change of cut point and/or conversion per pass as mentioned.
2) Install multiple cracking catalysts with varying activities/selectivity's such that the product structure can be optimized with bed temps between naphtha and diesel operating modes (Note: Recycle compressor capacity should be evaluated to ensure sufficient reserve quench); or,
3) Utilize HDT catalysts in the HDC reactor up to the limit of naphtha make and minimum naphtha octane. The conversion can swing by as much as 25% between maximum naphtha and maximum diesel, which is a function of catalyst volume [LHSV (liquid hourly space velocity)] in the hydrocracking reactor(s), so smaller units (i.e., smaller catalyst volumes/LHSV) will have a smaller potential conversion range. The key for catalyst selection is determining the optimal midpoint. Once this is defined, the new catalyst selection can be made.
JOE FLORES (Criterion Catalyst & Technologies/Zeolyst)
The main strategy for HCPT (hydrocracking pretreat) catalyst is to adjust average temperatures (WABT) throughout the cycle to achieve the designed nitrogen (N) slip (or its indications) to the cracking catalyst. Note that the N slip can be allowed to increase, which will affect the selectivity of the HC catalyst to be more diesel selective. The WABT is held at this temperature until excessive N slip is measured, or symptoms of N slip are observed, in the cases were Nslip cannot be measured. Desired delta T in first bed of cracking (at a target bed average temperature) provides an indirect measure of the N slip from pretreat. Based on pretreat catalyst deactivation, pretreat WABT will need to be increased to meet minimum N slip requirement for the cracking catalyst throughout the cycle. Therefore, choosing a catalyst which provides both high activity and strong stability will allow pretreat temperatures to be lower over the cycle.
An alternative pretreat strategy is to operate HCPT at the optimum temperature for maximum aromatics saturations initially [during SOR (start-of-run)] and then to hold that temperature through the cycle. This technique is often used with LCO or high aromatic feeds to maximize volume gain and is shown in the graph below.
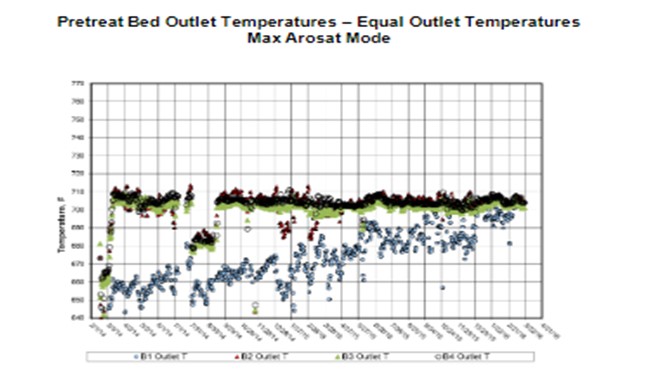
Note that every unit has a defined operating window in each of the HCPT and HC catalyst systems, as set by the delta between SOR and EOR temperatures. This delta, along with an estimated catalyst deactivation rate, will identify how much flexibility –or lack of flexibility –is available throughout the cycle for other parameters such as metals poisoning, processing heavier feeds (in the HCPT) or increasing N slip, or increasing conversion beyond the cycle operating goal (in the HC). Due to optimization efforts, units tend to have limited flexibility in their operating windows. And as an example, operating to a constant N slip and/or constant conversion is important in order to make a defined cycle as per the cycle operating goal, as shown in the next graph.
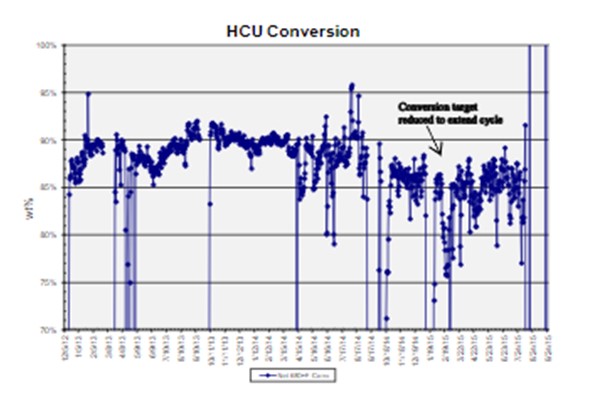
For HCPT, optimum catalyst utilization and maximum HCPT cycle life is achieved by operating to equal outlet bed temperatures as this results in each bed deactivating at similar rates. Some units have to operate pretreat in ascending profile due to heat integration limits in the units or to optimize metals uptake.
The main strategy of the HC catalyst is to operate to the design conversion. Optimum catalyst utilization is achieved by operating to equal bed dTs, which results in each cracking bed deactivating at similar rates. Equal dT operation in cracking beds often ends up with descending temperature profiles (since HC Bed 1 sees the highest nitrogen slip and aromatics slip from the pretreat beds). This bed is required to operate at the highest temperature to provide the same dTs as the beds below. In addition, a descending profile is usually not a safe way to operate; when recycle gas is lost during an upset, it could lead to an exotherm in all subsequent beds. Hence, we usually recommend a lower axial dT target for Bed 1 in hydrocracking, and equal dTs for other beds, to be able to target similar outlet temperatures at each cracking beds.
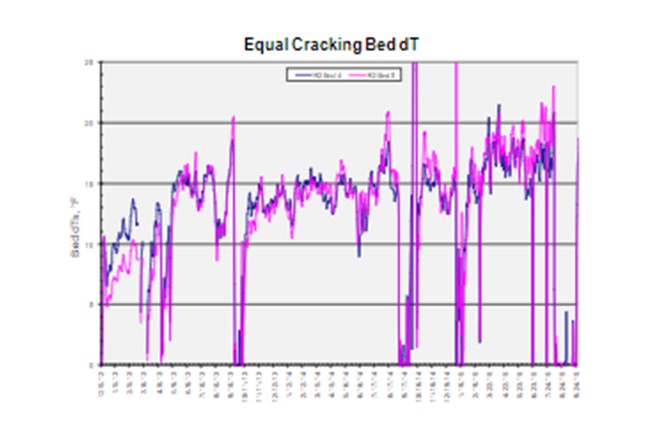
For cracking beds with very different volumes, the equal delta T strategy may need to be modified to suit the deactivation rates and peak temperatures profile. When operating between max (maximum) naphtha and max distillate modes, the equal dT strategy may need to be modified as EOR is reached, and the cracking bed temperatures start to approach mechanical limitations. Under these conditions, temperatures may need to be shifted to extend the catalyst cycle. Overall, the strategy is to utilize all catalyst beds during the cycle.
Typically, increasing conversion beyond the design will result in additional naphtha production (decrease in diesel), and a decrease in conversion will result in less naphtha production (and marginally more distillate material). Therefore, operating in a max naphtha mode normally would require the HC catalyst to operate at or above design conversion (and above estimated WABT) and up to the downstream gas plant limit. In max diesel mode, the HC catalyst would operate at or below design to maximize the distillate yield.
One must decide early which mode of operation (naphtha or distillate) will be desired for the next cycle so that the best catalyst solution for HCPT and HC combined is chosen. Operating a distillate selective catalyst in naphtha mode will not yield the optimum naphtha yield or cycle life, and operating a naphtha selective catalyst in distillate mode will not yield the optimum distillate yield. The correct mode of operation should be decided by involving the economics and planning department during the selection process in order to maximize profitability. In addition, RFQs need to be based on the most realistic case, and not the worst case, in order to make the best possible catalyst decisions.
Max naphtha catalysts offer longer cycle length when compared to max distillate catalysts. They often provide the highest volume yield due to their ability to operate at higher conversion, unless the feed is very easy; then, the conversion can be too high, because more naphtha will be converted to gas than distillate to naphtha.
Max distillate catalysts typically have lower activities, will operate at higher temperatures at equal conversion when compared to max naphtha catalysts, have lower selectivity towards naphtha, and higher selectivity towards distillates, and have lower gas make. Due to their lower activity, these catalysts will typically offer shorter cycle length when they are operated in max naphtha mode. At equal conversion, they often offer higher volume yields when compared to max naphtha catalysts due to higher aromatics saturation and lower gas make.
The optimum catalyst solution is determined by working closely with a catalyst supplier and considering individual refinery economics (including volume gain), cycle length requirements, and unit hardware constraints.