Question 21: What is the maximum olefin content allowed in isomerization unit feed? Are levels encountered different between C4 and C5/C6 units? What are the major concerns and limiting factors? What is the effect of olefins on the mole sieve used for drying the feed?
STREIT (KBC Advanced Technologies, Inc.)
The typical olefin limit in a C5/C6 isomerization unit is 2 to 3%. The olefin content of the feed is constrained by the high heat release that the olefins cause across the reactor. Olefins can polymerize and cause coking on the catalyst in an isomerization unit. This is typically more noticeable in isomerization systems that are once-through hydrogen because there is less hydrogen in the system.
With regard to the molecular sieves on the frontend of the unit, during normal operation, the olefins are not that much of an issue. Problems arise at the high temperatures experienced in regeneration of the molecular sieves. Those olefins that are on the sieve can polymerize at the high temperature and shorten the life of the filters or of the molecular sieves.
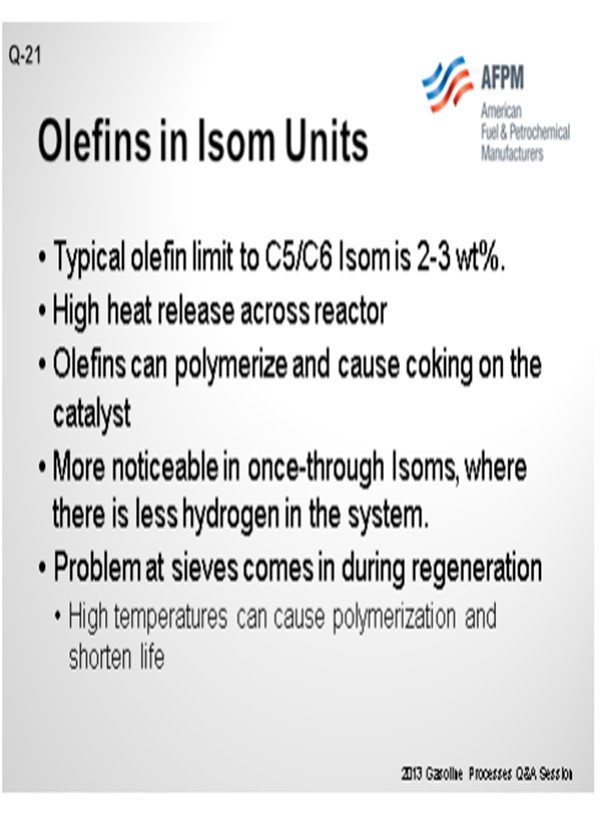
MELDRUM (Phillips 66)
My comments are similar to Eric’s. The limit is usually based on hydrogen consumption, heat release, and the feed dryers. Olefin saturation consumes hydrogen that would be needed for the isomerization reactions. So as the level of olefin increases in the isomerization unit feed, the isomerization unit reactions in the catalyst stability can be hindered. The exothermic temperature rise as olefins are saturated can compromise equipment design and increase the reaction temperatures to a suboptimal equilibrium range. Recommended reactor temperature limit is 400°F for both the C4 and the C5/C6 isomerization units. I agree with Eric on the molecular sieve deposits that can form primarily due to the higher temperatures used in the regeneration.
BULLEN (UOP LLC, A Honeywell Company)
I concur with Eric and Craig. The only additional comment I have is that the olefin is a double-edged sword on the dryer sieve. Not only does it reduce the life; we expect about 50% reduction in life for a number of regeneration cycles compared to non-olefinic feeds. That is probably down in the 200- to 250-regenerations range. In addition, when the sieve sees olefins, it will preferentially absorb them, resulting in pushing off some of the other contaminants; so you tend to have to regenerate the drier more frequently due to a reduction in delta loading. Not only do you get less life, but you also have to regenerate more often. It all becomes an economic decision, trading sieve life for catalyst life.
CRAIG MELDRUM (Phillips 66)
Isom feed olefin limits are defined by hydrogen consumption, heat release, and impact on feed dryers. Olefin saturation consumes the hydrogen needed for the isomerization unit reactions; so as the level of olefin in the feed increases, the isomerization unit reactions and catalyst stability can be hindered. Exothermic olefin saturation can compromise equipment design and increase reaction temperature to suboptimal equilibrium ranges. The recommended reactor temperature limit is 400°F for both C4 and C5/C6 isomerization units. Olefins can form coke in molecular sieve dryer material, limit the ability of the mol sieve to remove sulfur from the feed, and shorten dryer life by 50 to 75%.
UOP suggests limiting Butamer™ feed total olefins to 0.1 wt%, isobutylene to 100 ppm, and diolefins to 10 ppm. Penex™ olefin limits are suggested to be 2 wt% and Bromine number limited to 4. Typical NHT feed has a Bromine number of 0.1. The limit of 4.0 is to allow for sulfolane raffinate or reformer splitter stream to be routed to the unit. The volume percent olefin is approximately half the Bromine number.
PATRICK BULLEN (UOP LLC, A Honeywell Company)
In general, the olefin content to an isomerization unit is limited. The saturation of olefins is an extremely exothermic reaction; and in general, the content is limited to that fraction of total temperature rise that will not impede or interfere with other exothermic reactions that are also concurrently occurring in the isomerization reactor, such as benzene saturation, isomerization, hydrocracking, and ring-opening.
For isomerization units with a drier on the fresh feed stream (Penex™ or Butamer™ process units), the olefins in the fresh feed streams can damage the molecular sieve in the feed driers. The molecular sieve will capture a limited amount of the olefins; and upon the higher temperature during sieve regeneration, the olefins will polymerize to form carbon on the molecular sieve. This will result in reduced molecular sieve life and require more frequent change-outs of the molecular sieve beds and more frequent regeneration as the bed ages.
The presence of olefins can also compete with other contaminants, such as sulfur and oxygenates, for the adsorption sites on the molecular sieve leading to potential breakthrough and contamination of the Penex™ or Butamer™ catalyst.
If olefins do enter the isomerization reactors, in the absence of other contaminants, the olefins should fully saturate to their respective saturated hydrocarbon counterpart.
ERIC STREIT (KBC Advanced Technologies, Inc.)
Olefin content in isomerization unit feed can be as high as 2 to 3% for C5/C6 units that process light reformate or raffinate streams. However, the typical C5/C6 feed olefin content is less than 0.5%. Olefin contents of C4-derived feeds are typically lower than 0.5%.
Olefins in the feed to isomerization units typically saturate to their corresponding paraffin. In doing so, they consume hydrogen and generate heat due to the exothermic reaction. The maximum temperature rise across the lead reactor can become limiting if the feed olefin content is too high. Increased temperatures can lead to excessive cracking. Olefins that do not saturate polymerize and form coke on the catalyst. The polymerization and increased cracking shorten the catalyst life. This is more evident in hydrogen once-through units where the amount of excess hydrogen is limited.
Coker and FCC naphthas are fewer desirable feedstocks unless the diolefins in these streams have been removed. The highly reactive diolefins polymerize more readily, leading to shorter catalyst life.
At normal operating temperatures, olefins have little impact on the molecular sieve driers. A small amount of olefins may absorb on the sieve; and when heated to regeneration, temperatures, these olefins polymerize. This polymerization reduces the effectiveness of the driers to remove moisture to protect the catalyst. Shorter drier life can be expected as a result. As with any stream containing olefins, if oxygen is present in the feed along with the olefins, gums can be formed that can contribute to fouling on any of the equipment upstream of the reactors. This is normally not an issue in isomerization units because the oxygen is a poison for halided isomerization unit catalyst; so usually, there is no oxygen in the feed.