Question 21: What are your important considerations for water washing with respect to: 1) Intermittent injection a. Process temperature of injection b. Duration of injection c. Frequency - triggers to begin d. How frequently before making it continuously? 2) Water Quality: a. pH range b. Oxygen c. Total Suspended solids d. Total dissolved solids e. Recirculation vs. make-up f. Other
WENDY WILDENBERG (Flint Hills Resources)
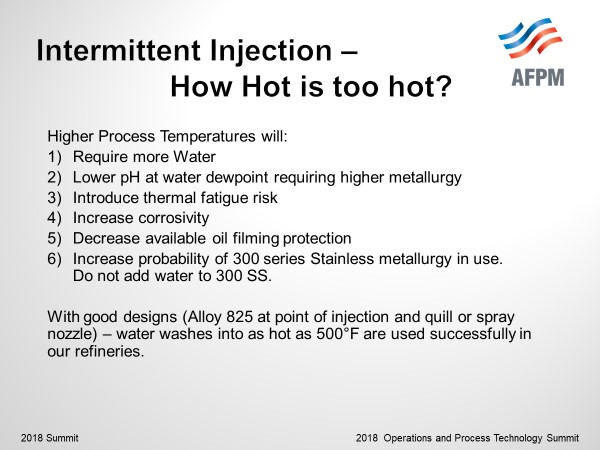
How hot is too hot for injection? Higher Process Temperatures will:
-
Require more Water to meet 25% Free Water at injection temperature. Injection of water that will all vaporize at the hotter temperature will guarantee that the droplets will form downstream and produce a corrosive mist prior to a well diluted stream. This may lead to aggressive corrosion where this occurs.
-
Lower pH at water dewpoint due to high solubility of HCl and low solubility of NH3. Recognition of this low pH may mean to consider higher alloy at the point of injection.
-
Increased thermal fatigue risk especially when greater than 300°F difference between water and upstream process temperature.
-
Increased corrosivity due to higher temperatures and typically lower liquid oil rates. Liquid oil has been shown to lower corrosivity.
-
Beware of Stainless-Steel Metallurgy that is more likely used at the hotter process temperatures. Do not inject water into stainless steel in order to prevent chloride stress corrosion cracking. All other components for this mechanism are already present except for liquid water.
Hotter temperatures typically will increase in the need for better designed injection systems. The injection mix point needs to be designed to contact and scrub the vapor well, with adequate dilution of water, with metallurgy at the injection point selected to handle the lower pH of the droplets. The goal of this injection is to as quickly as possible contact the liquid water with the vapor to move all the chlorides from the vapor into the aqueous solution without leaving deposits behind as places for under-deposit corrosion. A good injection system is even more important at the higher temperature where increased potential for vaporization and hot/cold areas if poorly distributed may exist.
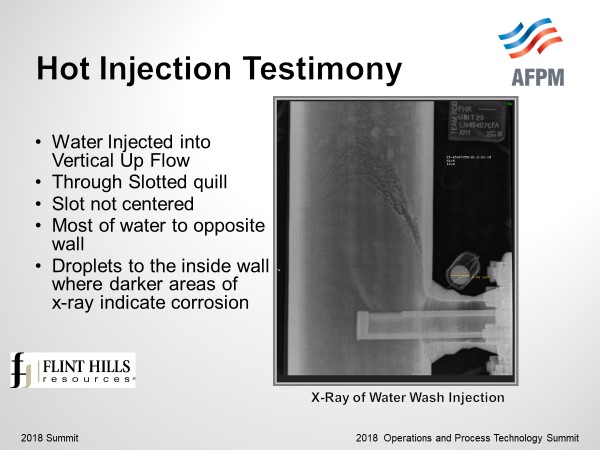
Lessons learned from a hot injection with a simple quill show what may happen with inadequate mixing / inadequate contact of the hot vapor with the water injection. This example shows a continuous injection of water with a slotted quill into vertical up-flow piping. An X-ray reveals several items: water comes out of the slot in a larger stream and directed with more flow toward the opposite wall. This slot was not centered in the piping. Droplets spray back to the inside wall above the quill. Infrared images show hotter temperatures above the quill on the inside wall and colder temperatures on the opposite wall confirming that more of the water flows to the opposite side. Corrosion is evident in between the hotter and colder areas and can be seen on the X-Ray. After this injection system was replaced with a better system (spray nozzle, static mixer, in an Alloy 825 section of piping), analysis of the removed piping allowed understanding of what this hot injection experienced.
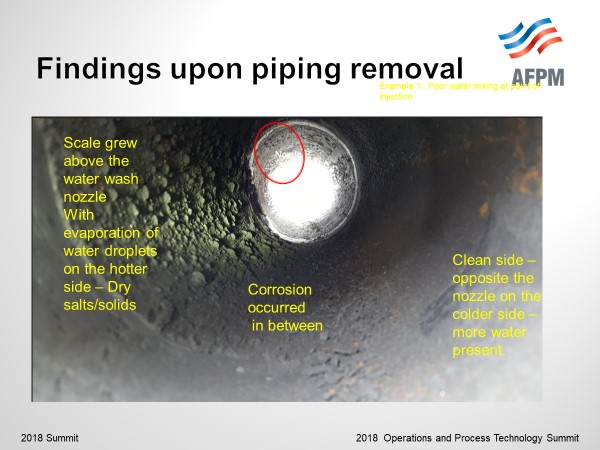
Scale formation was evident on the hotter section of piping. Vaporization of the stripped sour water left deposits of iron, iron sulfide, and other salt deposits on the piping. The opposite wall was clean and full metal thickness – this section was adequately water washed. But in between the dry area and the well washed cooler area, we found corrosion.
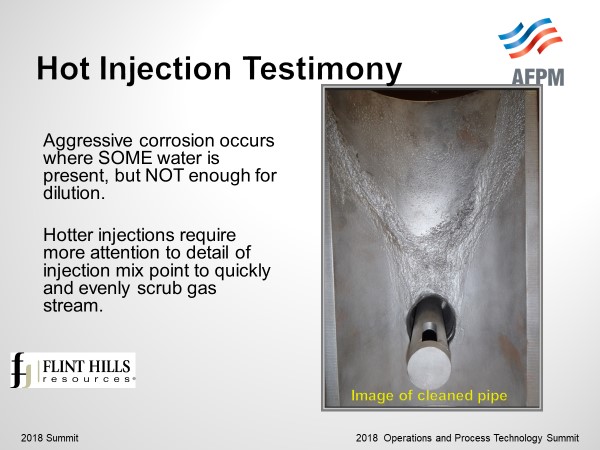
How long to intermittently wash? Duration of injection is typically 6-12 hours. Injection time is necessary to wash away all the salts which is longer than the time necessary for pressure drop to decrease too normal. If salts are not removed, the moist salts will increase corrosivity. Recommended practice is to sample the sour water for ammonia (NH3) and Chlorides (Cl) while executing the intermittent wash. Continue to wash until the ammonium salt levels decrease to baseline. As an alternative, documented results from previous washes can be used to establish duration of water wash. Audits are recommended to ensure conditions remain similar. Refer to API RP 932B, Section 6.8.3 for more information.
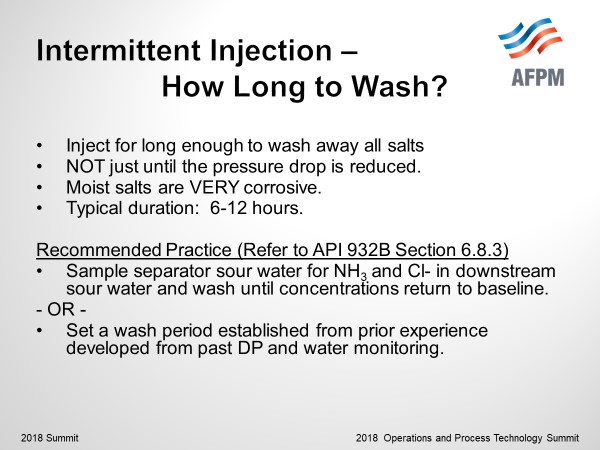
How long to intermittently wash? Duration of injection is typically 6-12 hours. Injection time is necessary to wash away all the salts which is longer than the time necessary for pressure drop to decrease too normal. If salts are not removed, the moist salts will increase corrosivity. Recommended practice is to sample the sour water for ammonia (NH3) and Chlorides (Cl) while executing the intermittent wash. Continue to wash until the ammonium salt levels decrease to baseline. As an alternative, documented results from previous washes can be used to establish duration of water wash. Audits are recommended to ensure conditions remain similar. Refer to API RP 932B, Section 6.8.3 for more information.
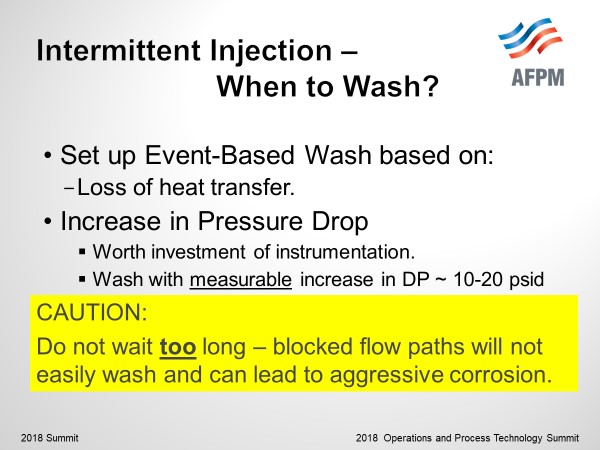
When to intermittently wash? Establish guidelines of when to wash based on loss of performance from exchangers. Loss of heat transfer is most often the earliest warning. An increase of pressure drop especially in the tube side of exchangers will also tell of the presence of salts. Shell side of the exchanger may take longer to show.
Recommendation is to wash when a pressure drop of 10-20 psid is measured, but not to wait too long until tubes become blocked.
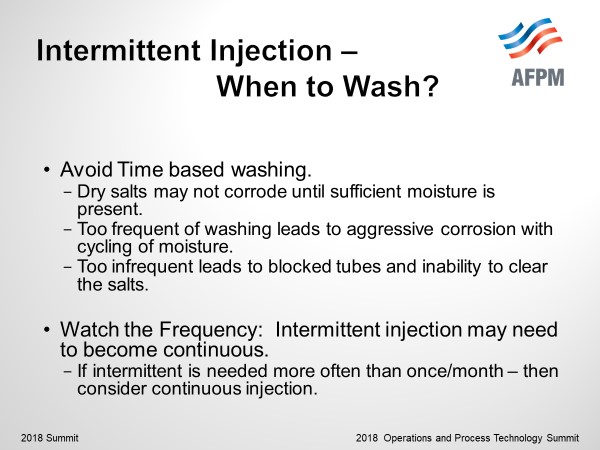
Avoid time-based washing. Dry salts may not corrode until enough moisture present. But too frequent of washing leads to aggressive corrosion. Watch the frequency of injection. If intermittent is necessary, more often than once per month consider reducing salts or making the injection continuous.
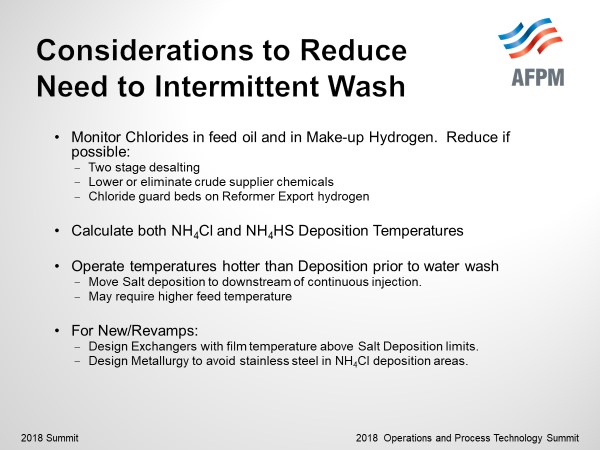
Consideration may be given to reduce the need to intermittently wash through changes to the incoming chlorides, changes to operational temperatures, and changes to new design or revamps. Most intermittent washes are washing ammonium chloride salts from upstream exchangers. Reduce chloride in feed oil and make-up hydrogen if possible. Two stage desalting and discussions with crude suppliers to lower chloride and/or bromide containing chemicals may aid in reducing oil sources. Chloride guard beds on reformer export hydrogen will reduce or eliminate chlorides in make-up hydrogen.
Calculate both ammonium chloride (NH4Cl) and ammonium bisulfide deposition temperatures and operate to maintain temperatures higher than deposition until the continuous water wash if possible.
For new designs or revamps, exchangers can be designed in order to plan for salt deposition downstream of the continuous water wash. Design exchanger trains with film temperatures above salt deposition in first exchangers with colder film temperatures downstream of the continuous injection. Also, exchanger metallurgy can be determined to avoid stainless steel in areas where ammonium chloride may deposit.
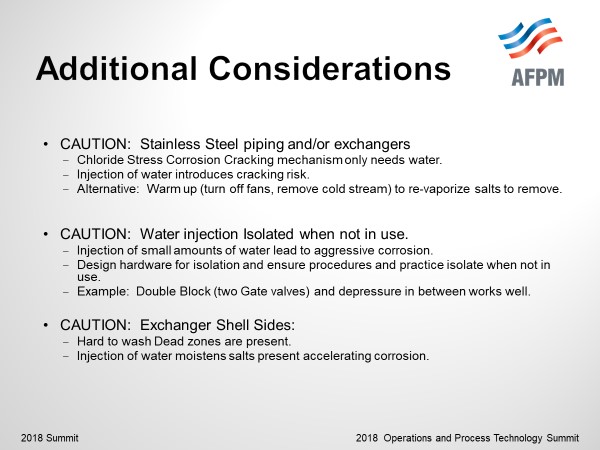
A few other cautions with intermittent water washing:
CAUTION: Stainless Steel piping and/or exchangers. Recommendation to not wash. Addition of water completes the recipe for stress corrosion cracking. Instead, consider warming up by removal of the cold stream or turning off fans if finfan to re-vaporize the salts to remove instead.
CAUTION: Ensure to isolate the water injection when not in use. The continued injection of small amounts of water leads to aggressive corrosion. Design hardware for isolation and ensure procedures and practices are in place to isolate when not in use. In our experience, a double block (two gate valves) with bleed to depressure in between works well.
CAUTION: Shell side water washing can be done, but hard to wash dead zones may be present. Additional water volume and longer wash times are recommended to remove salts.
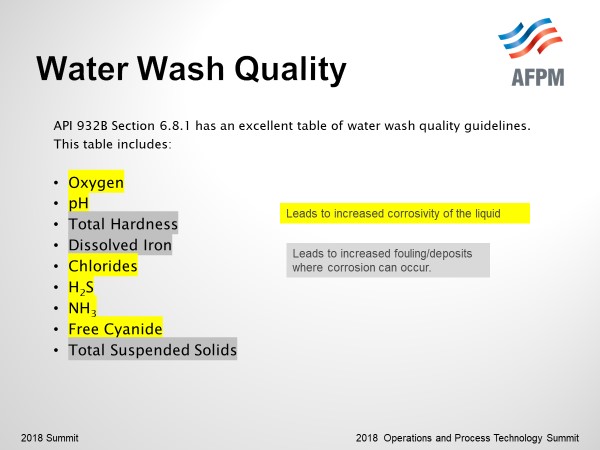
Water wash quality guidelines are well covered in API RP 932B and include limits on Oxygen, pH, Total Hardness, Dissolved Iron, Chlorides, H2S, NH3, Free Cyanide, and Total Suspended Solids with a description on the importance of each. Some of these factors increase the corrosivity, some increase fouling. Methods for water quality monitoring are important for your unit.
RICHARD TODD (Norton Engineering)
1a. Water wash rates are set by a variety of conditions, including at least 25% liquid water at the injection site, calculated by using the process conditions at the injection location.
1b. Intermittent injection should continue until the NH4Cl or NH4HS is shown to be removed by water testing for contaminants. It should not be set by pressure drop reduction as that can happen rapidly, while there are still salts to be removed.
1c. Intermittent wash water frequency should be set by delta pressure measurements, rather than on a time basis.
1d. If washes are required more than a few times a week, switching to continuous water wash should be considered.
2a. Water quality should be of stripped sour water or bfw/condensate composition, low oxygen, < 50 ppb, dissolved Fe, < 1ppm, and pH range of 7 to 9, TSS < 1, Cyanide <1 ppm. Recirculation should be determined by NH4HS, NH4Cl concentrations, and metallurgy. i.e., carbon steel requiring lower concentrations, along with % liquid water at the injection location.
JEFFREY ZURLO (Suez Water Technologies & Solutions)
Ammonia and halides in the reactor effluent will form corrosive salts as the it is cooled downstream of the reactors. Unless dissolved or dispersed, these salts can lay down in downstream equipment and result in fouling and under salt deposit corrosion, impairing production and reliability. Water washing the reactor effluent stream is an effective way to keep salts from fouling and corroding downstream equipment. Best practice is to provide the water wash continuously to ensure consistent washing of the piping/exchangers and prevent cyclical buildup of salts that can foul and corrode in between wash cycles. That said, water washing on a periodic basis can be effective, assuming the system is well designed, and the frequency is often enough to prevent equipment fouling and corrosion. The exact requirements for how frequently and how long to wash should be established on an individual basis as each system may react differently. The primary disadvantage of periodic water washing is creation of wet salts in the system, which generally increase corrosion rates as compared to dry salts or no salts.
Injection location should be upstream of salt formation temperature in the system and varies based on unit operating conditions and salt formation temperatures for the individual system.
One of the main considerations is to provide enough wash water such that there is enough liquid water present downstream of the water injection to dissolve and wash away the salts. Thermal and ionic modeling of the reactor effluent system can produce the required water volume and salt point temperature of the system to determine proper injection location and required water volumes.
Ideally, steam condensate or other source of water free of suspended solids, dissolved solids, and oxygen should be used. Poor quality wash water can result in adding to the solids deposition of the system, rather than cleaning the system of fouling materials.