Question 21: Silica uptake on gas oil and diesel hydrotreating units is an increasing problem. In your experience, what is the source of silica in these feeds? Do you have effective ways to manage this silica?
Vern Mallett (UOP)
The main source of silicon in Hydrotreaters is polysiloxane compounds (such as polydimethylsiloxane) used to control foaming in delayed coker units. It has also been reported that indigenous silicon is present in some heavy oils. Silicon may also be introduced to crude as a component of some drilling chemicals. Synthetic crude blends may include appreciable silicon as a consequence of the upgrading and production methods.
Under the high temperature conditions of a delayed coker, polysiloxane is thermally decomposed to silicon containing molecules of varying chain length. Siloxane molecules in the naphtha boiling range account for approximately 70% of the silicon in coker liquid products. The remaining silicon is distributed in the distillate and VGO fractions at around 15% each. The siloxane chain length increases with boiling range and this impacts the effect on hydrotreating catalysts. It is well known that silicon capacity of coker naphtha catalysts is proportional to surface area and spent catalyst analysis shows relatively uniform distribution of silicon throughout the catalyst pore structure. The same deposition observations hold true for siloxanes in distillate units. We observe different behavior in VGO units where apparently siloxane chain length is high enough to affect diffusion rate into catalyst pores. In VGO units it is not uncommon to observe high levels of silicon collecting on the surface of the hydrotreating catalyst, creating a kind of crust, often in combination with iron.
Depending on the feedstock, the countermeasures to the effect of silicon vary. In the naphtha and distillate fractions, use of high SA guard and main bed catalysts prevent breakthrough for the maximum period. In VGO units, a large pore diameter material with lower SA may be more effective at removing silicon. It's worth noting that the combination of lower LHSV and lower siloxane content in distillate and VGO feed stocks, as compared to naphtha feeds, makes it much easier to prevent silicon from progressing deeply into the reactor.
Brian Moyse (Haldor Topsoe)
Initially, we must examine the terminology
Silicon : The element Si, Mwt ~28
Silica : Silicon dioxide SiO2, Mwt ~60
Silicone : Polymers based upon repeating units with SiOR2
Typically Poly Di-Methyl Siloxane PDMS (Figure 1)
So, in our business, we typically talk about silica SiO2, because this is often what we actually measure in spent catalyst samples.
Today, silicon enters the oil refining system via a number of widely differing routes:
Oil Production
Crude oil
Water injection (enhanced recovery)
Utility systems (heating, gas scrubbing)
Downhole operations (drilling, cementing)
H2S/CO2 removal systems
Refineries
Delayed coking (antifoams – PDMS) Gas scrubbing
Wastewater treatment Fuels
Terminals
Crude oil
Wastewater treatment
So, we can see that for hydrotreater feedstocks, there are a number of possible sources for contamination by silicon. Historically, most of the silicon encountered in the refinery comes from the use of antifoams like PDMS used in delayed coking units.
When exposed to temperature, PDMS breaks down into fractions (Figure 2). So, depending on your cut point, although most of the silicon will be in the naphtha cut, some will also be encountered in the diesel and heavier gas oil fractions.
Figure 3 shows the impact of silica (SiO2) on catalyst activity. For silicon, the values on the X axis should be halved.
It is interesting to note that silicon deposition affects the HDN function more than the HDS activity.
As far as silicon pickup capacity of catalyst is concerned, there are a number of factors to be considered. First is that the actual deposition of Si is diffusionally-limited for catalyst particles larger than 1/20", so less-than-ideal pickup of Si will be experienced in 1/8" or 1/10" particle sizes.
There is also a function of catalyst surface area. The more surface area, the greater the capacity to pick up silicon.
From this, we can see that high surface alumina with no metals would have the greatest silicon pickup but, of course, would have no activity for HDS or HDN.
Finally, there is an effect of reactor operating temperature. Silicon pickup on catalyst increases with operating temperature, and pickup can double by increasing temperature from 500-600°F.
Properly formulated Silica tolerant hydroprocessing catalysts are capable of picking up 25 - 30% by weight of silica or 12 - 15% by wt of silicon.
Figure 1
POLYDIMETHYLSILOXANE
SYNONYMS Poly(dimethylsiloxane),dimethylpolysiloxane, dimethylsilicone fluid,
dimethylsilicone oil; INS No. 900
DEFINITION Consists of fully methylated linear siloxane polymers containing repeating units of the formula (CH3)2SiO, with trimethylsiloxy end-blocking units of the formula (CH3)3SiO-
Chemical names Simethicone (CAS name)
C.A.S. number 8050-81-5
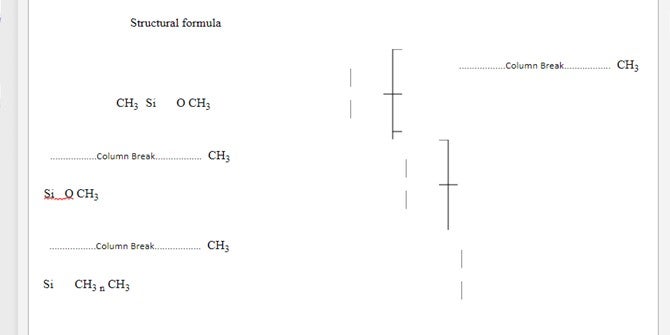
The average value for n is 90 to 410
Formula weight 6,800 to 30,000 (average and approximate)
Assay Silicon content not less than 37.3% and not more than 38.5% of the total
DESCRIPTION: Clear, colorless, viscous liquid. Polydimethylsiloxane is frequently used in commerce as such, as a liquid containing 4- 5% silica gel, and as an aqueous emulsion formulation containing, in addition to silica gel, emulsifiers and preservatives. The pure substance described here can be isolated by centrifuging from the silica gel-containing liquid at about 20,000 rpm.
FUNCTIONAL USES: Antifoaming agent, anticaking agent
Decomposition of PDMS
(Boiling Point of PDMS Fractions)
Product b.p. °F
Cyclic D3 273
Cyclic D4 349
Cyclic D5 410
Cyclic D6 473
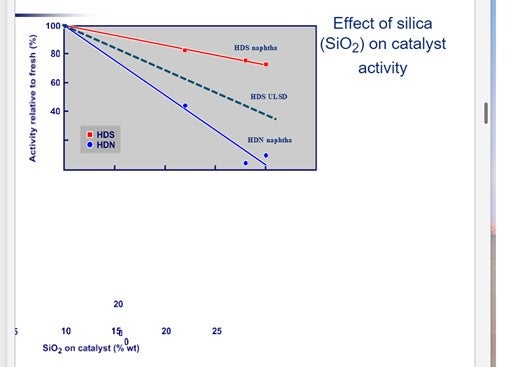
Figure 3
Geri D’Angelo (ART)
Silicon typically can be found coming from two locations in the refinery. Refiners having a coking process which requires antifoam usage generally see high concentrations of silicon in the naphtha and other light cuts from these units. Recently, refiners have been observing an increase in silicon levels coming from the crude tower and have begun to trace this to synthetic and other crudes new to the refinery. The process of making synthetic crude often involves a coking process, as well as other agents and antifoams added to the final product for ease of transport. Many different crude suppliers have been found to use additives containing silicon for the crude drilling process, and pipeline companies are using silicon containing additives injected into the crudes for both flow enhancing performance and foaming issues. The silicon tends to concentrate into most of the lighter cuts in the refinery including naphtha, kerosene, diesel and some gas oils. We’ve seen many of these types of units processing a feed directly from the crude unit which used to run for years between catalyst change outs, and now they shut down every 1-2 years due to silicon poisoning. The units did not have any guard catalyst installed as the refiners were not expecting silicon in a feed from the crude tower.
Some of the crude suppliers and pipelines have agreed to look into using different chemicals and technologies to decrease the amount of silicon ending up in the synthetic and other crude types. Progress in reducing the silicon values have been made by some of the suppliers which has been confirmed by the refineries. The reductions of the silicon values have been as high as 400%.
The most effective way to manage the silicon, assuming it can’t be removed from the feed slate, is to use a silicon guard catalyst near the top of the reactor to protect the main bed catalyst from poisoning for as long as possible. ART offers two catalysts which are effective at trapping silicon. AT724G is a high surface area silicon guard which has silicon pick up of capacity 20 wt% Si. Even higher levels of pickup have been observed in units which operated at higher temperatures. ART also offers AT734G which is a combined silicon and arsenic guard. It has a silicon capacity similar to AT724G with 4 times the arsenic capacity. Both AT724G and AT734G also have moderate activity and are used for activity and size grading at the top of the catalyst bed.