Question 21: High pressure strippers are an option for controlling VOCs in process condensate and managing export steam quality in a steam methane reformer hydrogen plant. What types of pH controls are being used?
OHMES (KBC Advanced Technologies, Inc.)
There is a lot more in the Answer Book on this topic, so I will just give some background for those who may not be fully aware of this situation. Most hydrogen plants take the process condensate, send it to a deaerator to clean it up, and then reuse that condensate while mixing it with some boiler feedwater internally. There are configurations that have high pressure strippers where they will bring in some steam and do some initial stripping. The benefit is that you get to recycle that steam, which is a savings. But really, the driver is that there are now more point source emission regulations, particularly in California, that require the installation of these strippers, which will impact how you do your pH control.
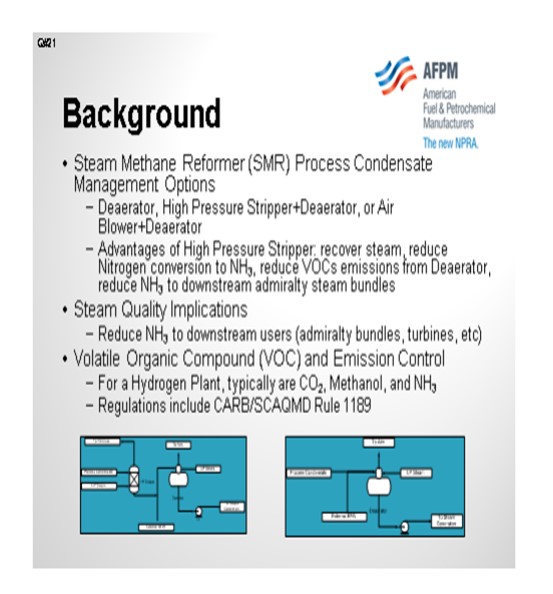
One option is to reduce the contaminant formation in the first place. Some refiners have looked at low ammonia and methanol formation catalyst. Most of them are using natural gas as their feed. So, if you can reduce the amount of nitrogen there, okay; but the nitrogen level often is what it is, and you just have to plan for a given content. For the condensate treatment itself, to be honest, most hydrogen plant operators just treat it like any other process condensate; so, talk to your water treatment vendor. Use a very consistent approach. We recommend two tips: First, make sure you mix your process condensate with the boiler feedwater you bring in before the deaerator because it gives you another layer of protection. And second, use some of the process chemistry that is already available.
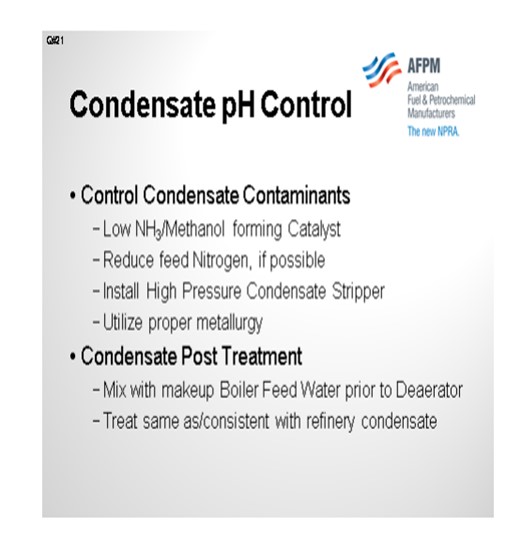
Most people will use neutralizing amines. There are a lot of options in this area. Again, I defer you to your water treatment vendor. The key there is just to check with your catalyst vendor to make sure the amine, or any treatment chemical, is not going to cause a problem, particularly since a lot of them will go to vapor phase and come back at the reformer catalyst.
Injection system is fairly simple: injection quill, day tanks, and metering pumps either going into the deaerator tank or into the suction line of the pump. For the pH, there is a wide range. Again, it really depends on your chemistry. Also, make sure you are following the ASME, (American Boiler Manufacturers Association) guidelines for operating pressure. Most of the hydrogen plants are generating 600 psig to 900 psig steam, so you can go all of the way down to about an 8.3 on the pH.
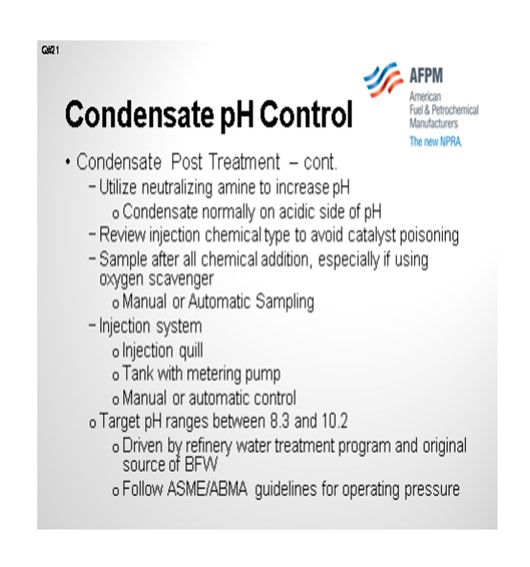
The final question was about carryover. Obviously, you need to treat the water, but you also must make sure you are running the steam generation equipment correctly. Manage your cycles of concentration as you would any other steam generator. Check the separation to confirm that you are not getting carryover of liquids that will cause problems downstream. If you are doing some deaeration, verify that the condensate has been properly treated.
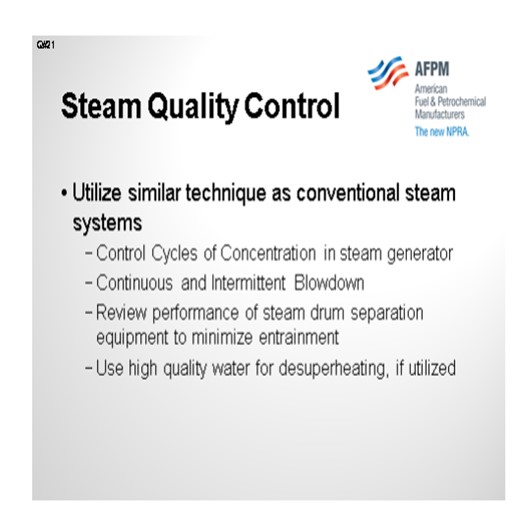
OHMES (KBC Advanced Technologies, Inc.) and ROSS BRUNSON, III (Süd-Chemie, Inc.)
To provide some context to the question, SMRs have several configuration options for managing and preparing internally generated condensate for use in steam generation, either within the SMR or within the broader facility.
Deaerator
• High pressure stripper followed by deaerator
• Air blower followed by deaerator (not shown)
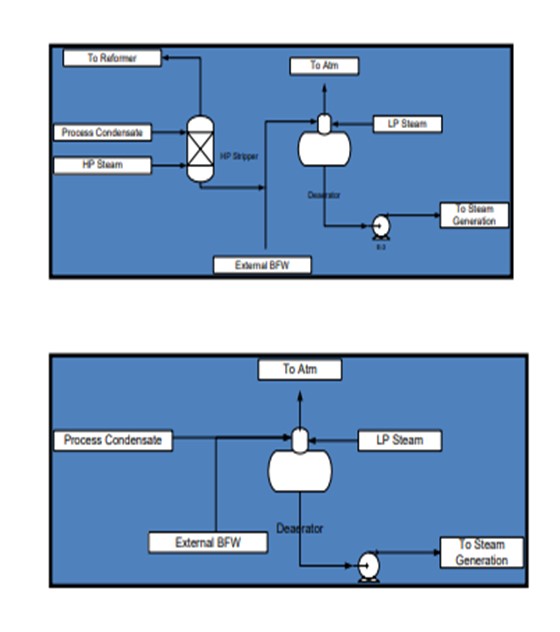
The primary purpose of this section of the SMR plant is to remove any oxygen (O2) or carbon dioxide (CO2) that is in the condensate. However, other contaminants, such as ammonia (NH3), methanol (CH3OH), and other trace volatile organic compounds (VOCs) and/organic acids. The ammonia is formed when nitrogen exists in the Reformer feedstock, while the other compounds are formed as trace secondary products in the reaction.
Ammonia and methanol in the condensate will end up in the steam product, which will impact the downstream steam users. Typical problem areas are steam turbines and admiralty bundles, as these compounds will cause corrosion and poor equipment performance.
In recent years, VOC and emission regulations have come into effect, thereby impacting hydrogen generation units. Regulations include CARM/SCAQMD Rule 1189, which impacts units in California. Outside of the reformer furnace, the condensate manage system is one of the next largest emitters on the unit. With a conventional deaerator, any volatile condensate.
contaminants exit the deaerator plume. Therefore, installing a high pressure stripper prior to the deaerator allows the unit to significantly reduce or eliminate VOC emissions, as the resulting stripper vapor stream is routed by the reforming section, thereby recovering these contaminants.
Therefore, installing a high pressure stripper and deaerator has the following advantages:
• Recovery of stripping steam,
• Reduction of conversion of nitrogen in feed to ammonia, as the recycled ammonia impacts the equilibrium reaction,
• Reduction of VOC emissions, and
• Improved steam quality through reduction of contaminants.
In reviewing in a broader sense, there are two primary options for controlling condensate quality: 1) control the condensate contaminants directly or 2) post-treatment of the condensate. For instance, if ammonia formation is a problem, reducing the native nitrogen in the feed may be an option or using a low ammonia (or methanol) forming catalyst in the shift reactor helps manage contaminant production. As high purity condensate can be highly corrosive, using proper metallurgy in the condensate treatment section helps minimize corrosion and corrosion product formation.
Outside of the treatment system configuration discussed above, KBC’s experience is that most hydrogen plants treat the internally generated condensate similar to how other facility condensates are treated. Therefore, the chemicals, injection systems, monitoring systems, and guidelines are normally consistent within a given facility.
In addition to pH control, the following practices and guidelines are recommended for condensate post-treatment:
• Mix the makeup boiler feed water (BFW) with the process condensate prior to the Deaerator to provide an extra layer of protection on water quality to the SMR steam generator.
• Most process condensates will be on the acidic side, so use a neutralizing amine to increase the pH.
o Review the chosen chemical with the reformer catalyst vendor to ensure poisoning will not occur (applies with all water treatment chemicals).
o Chose a neutralizing amine that achieves the desired Distribution Ratio (DR) between vapor and liquid phase for the chemical.
o Sample the treated water after all chemicals is added, especially when using oxygen scavengers, to ensure the final treated water meets target specifications.
o Sample systems and analysis can be manual or automatic.
• For the injection system:
o Use an injection quill to ensure proper mixing and dispersion of chemicals.
o Typically, use a metering pump connected to a chemical tank.
o Injection rate control can either be automatic or manual.
• Most plants target a pH between 8.3 and 10.2.
o Follow the ASME (American Society of Mechanical Engineers)/ABMA (American Boiler Manufacturers Association) guidelines for water quality, which are dictated by the resulting steam generation pressure
o Ultimately, the operator should discuss the hydrogen plant condensate treatment approach with the on-site water treatment chemical vendor to ensure the treatment approach is consistent with the facility water treatment chemistry and targets.
Finally, since the resulting condensate will be used to generate steam internally to the SMR or in the general facility, steam quality is also driven by the steam generation system. Therefore, as part of the review, consider the following aspects:
• Control cycles of concentration (CoC) in the SMR steam generator as one would for any other steam generator.
• Utilize both continuous and intermittent blowdown.
• Review performance of the steam drum separation equipment to minimize entrainment, which will impact steam quality.
If the SMR steam is being desuperheated, use high quality injection water to avoid steam contamination.