Question 20: When is it appropriate to neutralize austenitic stainless-steel equipment to protect against stress corrosion cracking (SCC)? What neutralization procedures and methodologies do you recommend?
JEFFREY MUELLER (Marathon Petroleum Company)
Background
Austenitic stainless steels (200-and 300-series steel) are the most common type of stainless steels. Austenite refers specifically to the geometry of the steel (face-centered cubic crystal). These types of steel are most typically recognized as non-magnetic. Austenitic steels are widely used in the industry because they have very desirable mechanical properties. Their austenitic structure is very tough and ductile down to absolute zero. They also do not lose their strength at elevated temperatures as rapidly as ferritic iron base alloys.
One negative aspect of austenitic steels is that they are susceptible to polythionic acid stress corrosion cracking (PTA SCC). PTA SCC refers to an intergranular form of cracking that can occur in sensitized austenitic stainless steels and other sensitized austenitic alloys. The following photo1shows intergranular stress cracking of a heat exchanger.
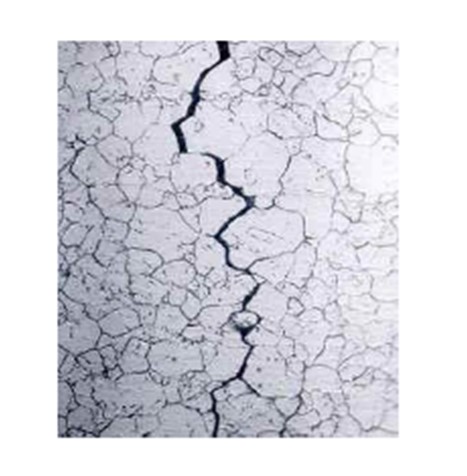
Polythionic acid refers to the family of acids that have the form H2SxOy, where x is generally considered in the range from 1 to 5, and y may range from less than 1 to 6. Polythionic acids are formed when sulfide corrosion products on the internal surface of equipment (e.g., iron sulfide) reacts with oxygen and water.
Sensitization is a metallurgical condition caused by specific heating, cooling, and/or deformation processes that result in precipitation of constituents (for example, chromium carbides in stainless steel) at grain boundaries, which results in the grain boundary being more susceptible to intergranular corrosion. Sensitization can occur in hydroprocessing units that run at higher operating temperatures.
1https://www.nace.org/uploadedImages/Corrosion_Central/Corrosion_101/intergrainscc.jpg.
The critical level of sensitization and stress required to initiate PTA SCC are not well understood. The rate of sensitization can be directly correlated to an increase in temperature within the sensitization temperature range. In addition, the rate of sensitization varies based on the composition of the steel. Certain grades of austenitic steel are “chemically stabilized” with titanium or niobium to alter the sensitization temperature range and thus can be resistant to PTA SCC.
The following table shows the reported sensitization temperature ranges for some austenitic materials.
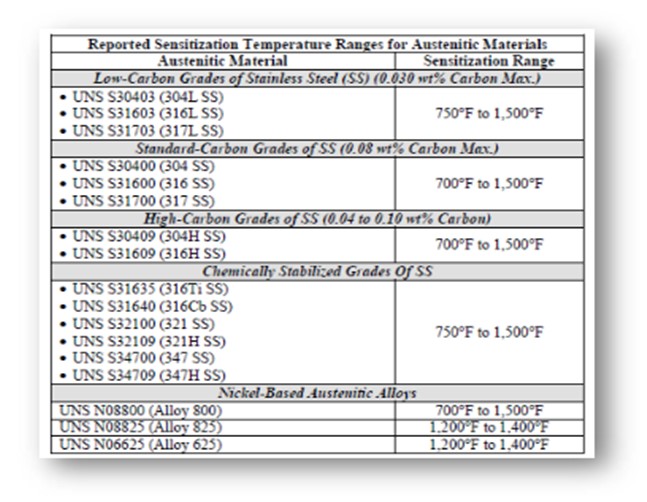
Protecting Against PTA SCC
The first step in preventing PTA SCC is understanding the location(s) in the process where it can occur. In hydroprocessing units, the risk is higher due to the fact that the process operates in a reduced atmosphere (no oxygen or CO2), making it conducive to the formation of high-temperature iron or other metal sulfide scale. Most typically, sections of the reactor circuit operate in the appropriate temperature range andcorrect metallurgy to be at risk of PTA SCC. Within the circuit, stainless heater tubes are another common place for this attack [both ID (inner diameter) and OD (outer diameter)].
Neutralization, or alkaline washing of the equipment surface, is one method used to prevent PTA SCC. In this process, the equipment is rinsed with a soda-ash solution [approximately 2 wt% (weight percent) to neutralize any acids formed at the metal surface and, after draining, leave a thin alkaline film on the surface that can neutralize any additional acid formation. This wash must occur prior to exposure to air (and prior to opening any equipment), and all of the equipment’s internal surfaces must be contacted for the washing to be effective.
Some important notes about the procedure are as follows:
*The system should be filled with alkaline solution under an inert atmosphere to minimize oxygen contamination.
*The equipment should be soaked, or the wash solution circulated for a minimum of two hours.
*At all times, the solution should maintain a minimum pH of 9 and a chloride limit of 1000 ppm.
*Reactor inlet and outlet spools should be sprayed with solution under inert atmosphere, immediately wrapped with plastic, and stored out of weather until reinstalled.
There are potential downsides with an alkaline wash procedure. Chlorides in the wash water and the process unit (ammonium-chloride salts) can lead to chloride SCC of the steel. A sodium nitrate (NaNO3) corrosion inhibitor may be added to the wash solution to reduce the likelihood of chloride SCC. In addition, a maximum chloride concentration of 1000 ppm should be honored during the wash. It is important to have a good rinse step after the wash procedure, as any residual wash water can concentrate during the heat-up process and result in chloride or alkaline stress cracking.
There are other means available to protect against PTA SCC. They include:
*Appropriate Material Selection: Selecting a stabilized grade of austenitic steel where PTA SCC is less of a concern.
*Appropriate Fabrication Methods: Heat treatments to maximize resistance to sensitization should be conducted after all hot and cold forming operations.
*Avoidance of Oxygen Entry: Using nitrogen to keep air out of a process if the shutdown does not involve invasive work of a piece of equipment. (Important: Make sure the oxygen level is less than 50 ppm in nitrogen. Users have found oxygen levels as high as 1000 ppm in commercial nitrogen.)
*Avoidance of Water Entry: Using a dehumidified air purge for protection against PTA SCC is acceptable if the dew point temperature of the air entering the vessel is maintained a minimum of 40°F lower than the internal surface metal temperature. It is important to remember that in process heaters with stainless steel tubes, it is critical to protect the OD of the tubes from PTA SCC. This is most commonly applied at Marathon Petroleum Company (MPC) by maintaining temperature inside process heaters (firebox) with austenitic stainless-steel tubes well above dew point. This is typically accomplished by maintaining some pilots or inserting a portable heater into the firebox during the outage. Sample Procedure The following are key excerpts from a successful neutralization procedure from a distillate hydrocracker at an MPC refinery.
*All austenitic stainless (300 series) steel equipment that has been exposed to temperatures greater than 700°F (can be higher/lower based on MPC guidance) must be neutralized prior to exposure to any source of air (oxygen) and water. Stainless steel equipment that is in contact with sulfide corrosion products may be susceptible to polythionic acid stress cracking (PASCC) if the corrosion products are exposed to contributing factors such as oxygen and water, and if the austenitic material is in a high degree of sensitization.
*For this shutdown, the “hydrogen reactor heater” will remain under an inert atmosphere and will not require neutralization. The convection section of “debutanizer tower reboilers A” is being replaced, so neutralization of this heater will need to occur during this shutdown.
The components identified to need neutralization must be:
*Neutralized with a soda ash solution before exposure to oxygen or water, A chemical handler, such as PSC, should assist in the process. An N2(nitrogen gas) blanket/purge should be completed before blinding.
*Hydro blasted with soda-treated water,
*Hydrotested with hydrocarbon,
*Protected by the soda ash film for the duration of the turnaround, or if the protective film is removed by any subsequent water wash, rain, or mechanical work, it must be reapplied with hand-held sprayers.
*Kept under an inert atmosphere. Three neutralizing circuits will be set up in order to accomplish the process. The circulating solution should consist of the following:
*Condensate is preferred for making the solution, but other water sources may be considered if the chlorides meet the specifications.
*The desired solution is 2 to 2.5 wt% soda ash.
*Addition of 0.4 wt% sodium nitrate as corrosion inhibitor is recommended.
*Addition of 0.2 wt% alkaline surfactant to increase the penetration of oily films and residues is suggested.
*The solution should have a maximum of 50 ppmw (part per million by weight) chlorides, which must be tested prior to use with the chloride test strips that can be obtained from the lab.
*After the catalyst is unloaded and the atmosphere is still inert, the reactor walls/internals should be neutralized. Sprayers with soda ash solution should be used to coat the wall and internals. Throughout the duration of the reactor work, the soda ash solution should be reapplied if the protective coating is removed by water or mechanical work. Any internals (ells, flanges, quench nozzles, thermowells, quench check valves, etc.) removed from the system must also be sprayed as soon as possible. The following needs to happen during neutralization:
*Fill each circuit with neutralization solution. Vent at high points until solution spills to ensure that each circuit is liquid full. Circulate at a target of 200 gpm (gallons per minute) for a minimum of two hours.
*Maintain circulating temperature above 120°F, which may require vendor steam heat (200°F upper limit).
*Monitor the pH and chlorides every 30 minutes; do not go below 9 pH and do not exceed 250 ppm chlorides. The following needs to happen after neutralization:
*Each circuit will be drained into a frac tank before the solution is sent to the WWTP (wastewater treatment plant). If acceptable, spent solution from spraying the reactor internals and ID will be drained directly to sewer.
*A sample from the frac tank should be taken to the lab to test for pH, COD (chemical oxygen demand, TDS (total dissolved solids), Cls (chlorides), and ammonia. Based on these tests, the WWTP will advise on how quickly it can be drained to sewer.
*Drain all low points in the circuit. If water is left in any low points, the bleeders are subject to potential alkaline stress corrosion.
*Use fresh soda ash solution for hydro blasting and hydrotesting.
*Protect bundles and equipment from rain to avoid removing protective coating.
*Prior to equipment start-up and heating of equipment, a hydrocarbon flush should be conducted to flush residual solution out of the system (not practical on the recycle gas and RX (reactor)inlet circuits). Drain all low points in the circuit again.