Question 20: Pre-hydrotreated feeds and crudes look easy to process on paper. Why is it more difficult than expected to process pre-hydrotreated feeds in a hydroprocessing unit?
Tim Lewer (Shell)
A: Pre-hydrotreated feeds are often the most difficult feeds to process in hydrotreaters primarily because the remaining molecules to be treated are the most refractory. Low sulfur feeds are not automatically the easiest to process; the sulfur species determines the difficulty of processing, not the total sulfur.
The chart below illustrates the different sulfur species in a distillate stream with boiling point, their relative concentrations, and the relative reaction rates:
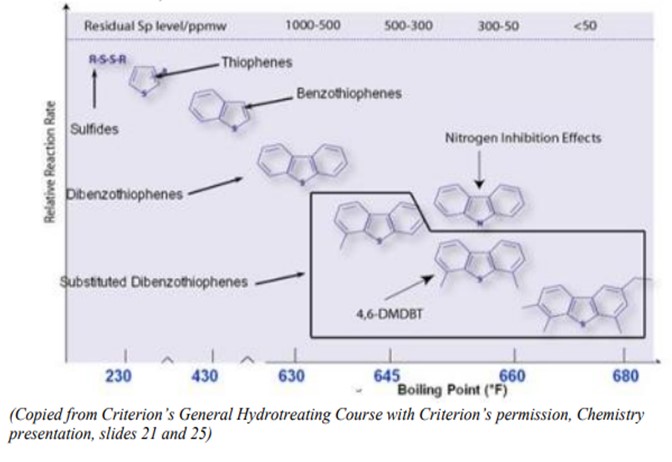
The chart illustrates that as boiling point increases, the molecules that contain sulfur both drop in concentration and reduce in HDS reaction rate. Thus, for example, sulfides are significantly more easily removed than dibenzothiophenes, which are themselves more easily removed than di-substituted dibenzothiophenes. Additionally, as boiling points increase, the nitrogen species also become more refractive and difficult to treat, adding to competition for the active sites on the catalyst.
Pre-treating has the added effect of removing the lighter, less refractive and more reactive species from the stream to be hydrotreated later. Thus, the sulfur molecules that remain are the most refractive and difficult to treat.
Consider, as an example, the following three feeds:
• Feed A: Previously hydrotreated straight-run diesel with 0.2 wt% Sulfur;
• Feed B: Straight-run diesel blended with cracked stock containing 1.29 wt% sulfur;
• Feed C: Straight-run diesel blended with cracked stock containing 0.52 wt% sulfur.
A cursory evaluation of these three feeds might suggest that Feed B is the most difficult to treat, containing the highest amount of sulfur and cracked stock. However, a more in-depth analysis, specifically a gas-chromatograph (GC) of sulfur species with boiling point reveals significantly more information:

Here, the relative concentrations of each molecule are measured along the y-axis, and the boiling point of each species is measured along the x-axis.
Evaluating this GC illustrates that the most refractive sulfur is in Feed A with 94% refractive sulfur, followed by B with 48% refractive sulfur and finally Feed C with 37% refractive sulfur. Thus, pretreating increases a feed’s processing difficulty by removing the “easy” sulfurs and leaving only the “hard” sulfurs to remove.
Traditional models are based on correlations of bulk properties, not molecules. In such models, pre-hydroprocessed feeds seem easier than they are because their total sulfur, total nitrogen, and density are low. But there can be a 10x to 100x difference in reaction rates between “easy” sulfur compounds and “difficult” compounds such as di- and tri-methyl dibenzothiophenes (DM-DBTs and TM-DBTs). The same applies to “easy” and “difficult” nitrogen. Low severity hydrotreating removes easy molecules, leaving tough ones behind. In ULSD, almost all of the remaining sulfur is present in DM-DBTs and TM-DBTs. An additional round of low severity hydrotreating won’t do much. They can only be removed by high-severity treatment.
Hydrocrackers frequently process feeds that were previously hydrotreated in low-severity units. These feeds usually remain more difficult to process than the non-hydrotreated feeds, especially if they come originally from cat feed hydrotreater (CFH) units or Syncrude's derived from Resid. Previous treatment removes sulfur and nitrogen, saturates aromatics, and might even clip offside chains. The resulting products boil below 1000°F, but they contain large polynaphthenic compounds. Due to strong thermodynamic drivers, these are very susceptible to dehydrogenation under high temperature. When the large PolyNapthenics lose hydrogen, they form large PolyAromatics which condense readily into coke.
Shankar Vaidyanathan (Flour)
Pre-hydrotreated feeds are more difficult to process because the conventional inspections of bulk gravity, sulfur and distillation do not adequately define the characteristics. Additional information such as chemical speciation and molecular distribution over the boiling range may be necessary. Upstream upgraders are all not equal in process configuration so a good idea is to evaluate how the syncrude barrel is constituted. In general, deeper hydrogenation, higher pressures and larger reactors may be necessary to process pre-hydrotreated feeds. The chemical hydrogen uptake estimates need to be prepared with special care for pre-hydrotreated feeds. Catalyst fouling rates need to be defined based on pilot work.
Downstream processing of pre-hydrotreated SCO derived diesel for ULSD may require ring opening or deeper hydrogenation for aromatic saturation in order to meet sulfur, cetane and gravity specifications. The nitrogen and aromatic content of pre-hydrotreated SCO derived gas oils is high and this can be a challenge in downstream treating for FCC feed. If the pre-hydrotreated gas oil is partly derived from an ebullated bed process, consider the fact that it had already passed over a high pressure, high residence time hydroprocessing environment while defining the downstream hydrocracker treating and conversion objectives. Some refiners have also seen higher levels of suspended sediments, metals and silica so pay specific attention to catalyst system selection, configuration and layering to avoid pressure drop issues. Other refiners have faced heat balance issues, and a few have also had compressor capacity issues.
Kaspar Vogt (Albemarle)
Simply put, the easy sulfur and nitrogen bodies have been removed and the hard sulfur and nitrogen molecules remain. Pre-hydrotreated feeds went through an upgrading process, e.g., coking, followed by preliminary mild hydrotreating.
Pre-hydrotreating is an economic way to meet feed specifications without consuming too much in hydrogen or investing in a high-pressure hydrotreating unit. Pre-hydrotreated crudes are also often blended with lighter feeds, e.g., naphtha, to reduce density and improve pumpability.
The pre-hydrotreating process removes easy Sulfur, but only part of the refractory Sulfur and Nitrogen, and only saturates PNAs. Typically, at least in case of a mild pre-hydrotreating process, N/S ratio is higher than in non-pretreated feeds, as on average Sulfur species are easier to remove than Nitrogen species.
Typical characteristics of a pre-hydrotreated feed are thus a very high refractory Sulfur fraction (can easily be 50% of the total Sulfur vs typically 7-9% in a regular LGO), a high concentration of aromatics and mono/polyaromatics ratio (e.g., 85% vs 55-60% of a regular LGO) and a very high N/S ratio (0.15 vs 0.01 in a regular LGO).
Apart from the shift in the N/S ratio, which is particularly evident in case of a mild pre-hydrotreatment, or the MonoAromatics/PNA shift, the best way to recognize and characterize pre-hydrotreated feeds is by means of Sulfur or Nitrogen specific speciation analyses, like GCxGC-S/NCD. These techniques typically reveal a shift towards a relatively higher concentration of the most refractory S- and N-species, like 4, 6-DMDBTs and highly refractory organic basic Nitrogen, like acridine. In addition, the still large presence of N-containing PNAs makes the feed prone to coking on the catalyst surface. When light feeds are added to reduce density, low hydrogen partial pressure may be further lowered during operation due to higher feed evaporation. This can make coking more pronounced, especially at the reactor bottom where temperature is the highest. All considered, it is thus very important to know the source of a feed and if it has been upgraded and pre-0hydrotreated.
Brian Watkins (ART)
Opportunity feedstocks, having already been processed through conventional refinery processes, pose unexpected challenges to refiners wishing to incorporate them into the distillate pool. Some of these streams have proven to be significantly more difficult to process underscoring the fact that it is important to understand the potential impacts of processing new feed streams in order to avoid unpleasant surprises. Significant differences in feed reactivity for various pre-processed feeds components are not necessarily anticipated from the usual bulk feed analyses.
When considering the use of synthetic crudes an understanding of the upstream processing is important. Production of synthetic fuels involves a combination of several processes in order to accommodate downstream processing. These upstream processes include coking or an ebullating bed reside operation, followed by a hydrotreating or hydrocracking operation in order to produce a lighter grade material. These hydrocracking units tend to operate at severe conditions in conjunction with high hydrogen partial pressures. At these conditions, the removal of all the easy, less refractory sulfur is readily achieved, and the majority of the multi-ring aromatics are saturated. This leaves a product that is relatively low in sulfur and PNA’s and when added to the feed to a ULSD unit gives rise to a surprisingly difficult feedstock to process. These products are then blended in with other heavier materials as a diluting or cutting stock and sent downstream as synthetic crude.
Likewise, the use of diesel range products from an H-Oil®, LC-FINING unit or fixed bed residuum desulfurizer can also have a significant impact on downstream diesel catalyst activity for similar reasons. The general properties of these types of diesel feeds often indicate that they may be relatively easy to hydrotreat due to their low sulfur content and API gravity, which is often similar in appearance to straight run (SR) materials. Table 1 lists the properties for several of these diesel feeds including the diesel product fractions from an ebullating bed residuum (EB) unit, a fixed bed residuum (FB) unit and a diesel fraction from Canadian synthetic crude.
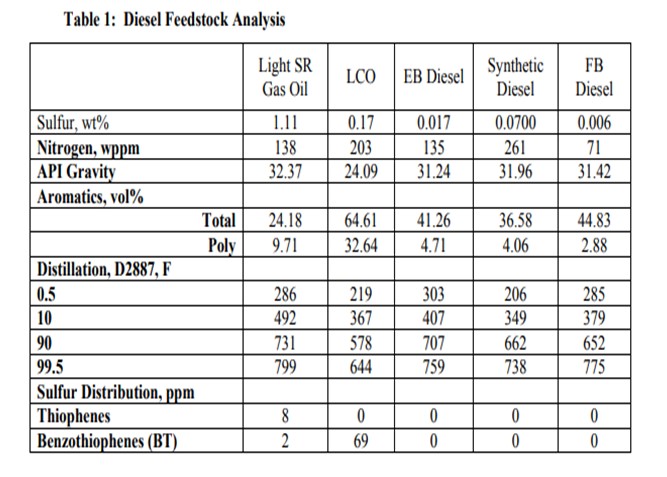
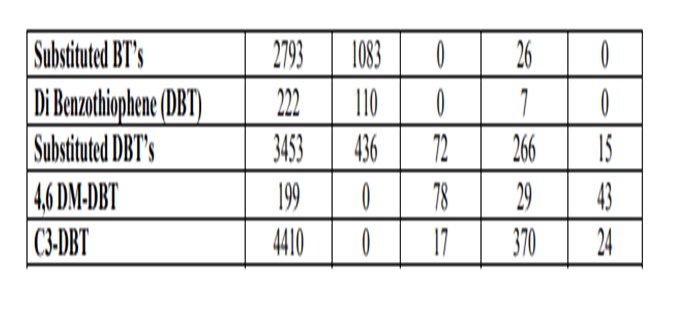
Figure 2 shows the activity difference between a SR and a blended SR / Synthetic diesel. Note that at higher product sulfur, the two feedstock’s respond similar to each other. As the application becomes more demanding, the required reactor temperature increases dramatically for the synthetic diesel feed as compared to the SR feed. The blended feed requires more than 25°F higher temperature relative to the SR to achieve ULSD sulfur levels.
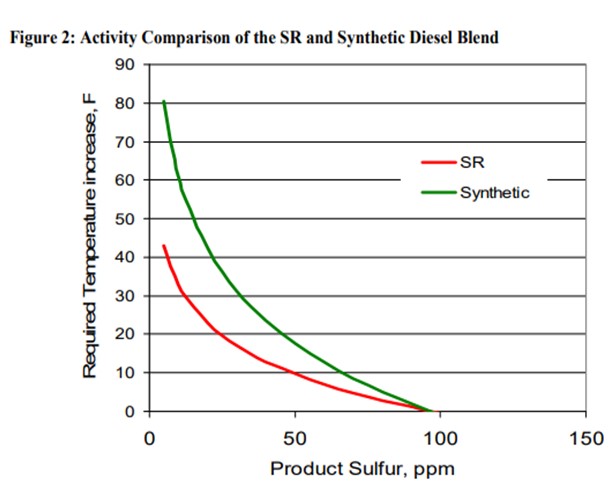
It is reasonable to expect that the upstream hydroprocessing of the synthetic diesel material results in a feed that behaves similarly to other previously hydrotreated feedstocks like those from the EB and FB residuum applications.
Advanced Refining Technologies can work closely with refining technical staff to help plan for processing opportunity feeds such as those discussed above. One of the keys is being aware of the potential impacts processing certain feeds will have on unit performance. Feeds which have been previously processed present unique challenges and ART® is well positioned with its experience at providing customized catalyst systems for ULSD applications. Opportunity feeds provide yet another objective to consider when designing the appropriate catalyst system to maximize unit.
Raj Patel (Haldor Topsoe, Inc.)
The main reason is that pre-hydrotreated feeds have already had the easy sulfurs removed in the initial hydrotreating step and thus when this pre-hydrotreated crude is blended with other crudes in the refinery and the intermediate cuts after the crude unit reach the next step in hydrotreating, the overall properties (i.e., API, distillation, total sulfur, etc..) may seem to be easily processed but unknowingly the sulfur distribution is heavily weighted to the difficult sterically hindered species (4,6 dimethyldibenzothiophenes and heavier).
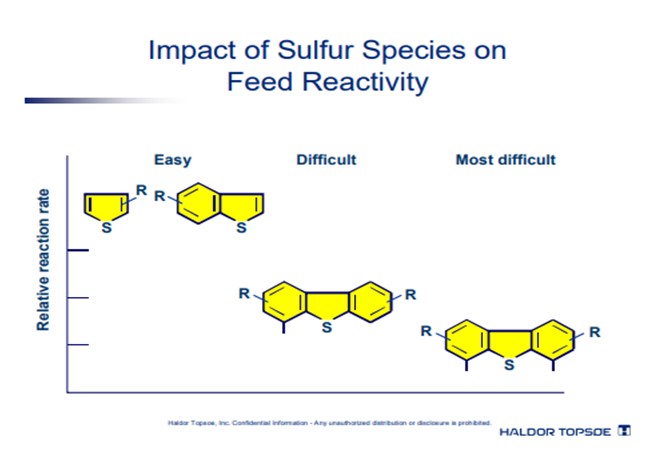
To give an example of the impact of the sulfur distribution on the operation of a hydrotreater, Haldor Topsoe has evaluated a refiner’s Ultra Low Diesel Unit feed at two different times in the run. The feed to this unit appeared to be very similar in feed properties routinely monitored by the refinery however the hydrotreating temperatures required were showing a difference in severity. Upon review of the sulfur speciations of the feed retain samples, the following results were determined:
Feed Sample #1
Total Sulfur (ppm) 4900
4, 6 Dimethyldibenzothiophene (ppm) 90
4-methyldibenzothiophene (ppm) 154
4, 6 DMDBT/Total Sulfur (%) 2
4-MDBT/Total Sulfur (%) 3
Feed Sample #2
Total Sulfur (ppm) 5080
4, 6 Dimethyldibenzothiophene (ppm) 212
4-methyldibenzothiophene (ppm) 315
4, 6 DMDBT/Total Sulfur (%) 4
4-MDBT/Total Sulfur (%) 6
This difference between what appeared to be similar diesel feeds at first glance required a 25°F increased WABT to make the same ULSD product with Feed #2.
Another example is found below.
Comparison of two LGOs with equal total sulfur content but different history
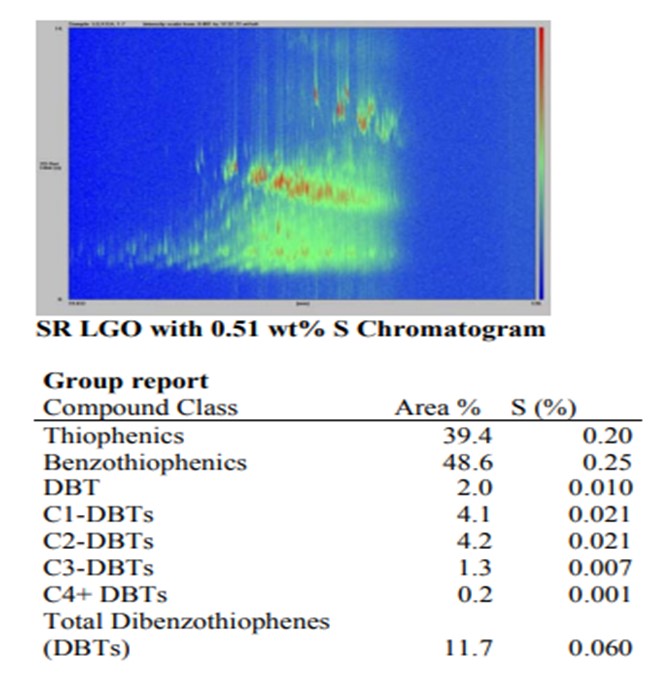
In the “raw” straight-run LGO that has not been hydrotreated, the distribution of sulfur is dominated by the lighter boiling and higher reactivity compounds – sulfides, thiophenes, naphthenothiophenes and benzothiophenes. These “easy” sulfur compounds constitute 88% of the sulfur in the feed.
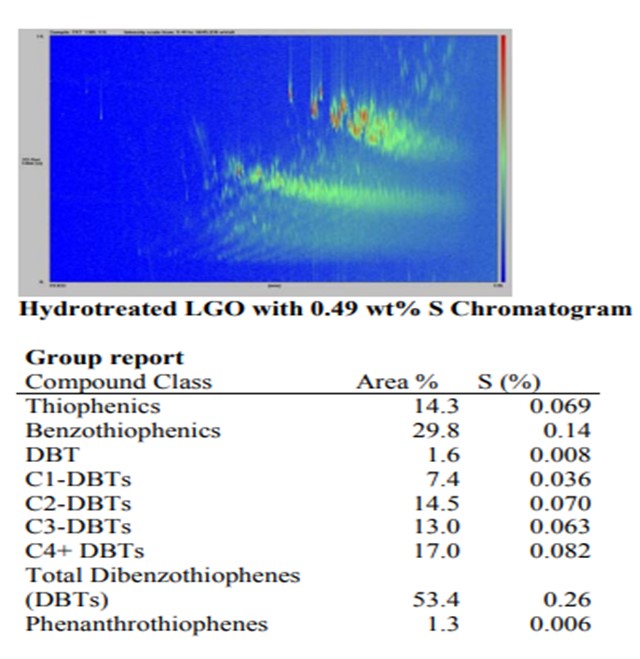
In contrast, the sulfur distribution in the hydrotreated LGO shows that more than half of the sulfur is present as dibenzothiophenes (DBT) structures with one or more alkyl groups. These sterically hindered species are the slowest reacting sulfur molecules existing and will greatly impact the overall reactivity of the feed.