Question 20: How do refiners quantify the impact of sodium on hydroprocessing units, specifically those processing either residuum or VGO feeds?
Dan Webb (Western Refining)
Sodium generally enters a hydrotreater due to upstream addition of caustic soda or desalter operational problems. Feed sodium content of more than 3-5 ppm should be avoided. Sodium has a significant deactivation effect; 1-3 %wt results in a 50% loss of catalyst activity. The deactivation mechanism is by blocking of acid sites and a reduction in the cracking function. Also, sodium penetrates the entire pore structure of the catalyst; and, when combined with water, can weaken the catalysts support structure causing breakage and high pressure drop. Sodium promotes catalysts sintering during regeneration. Catalysts containing more than 0.25 %wt sodium are not suitable for regeneration.
Brian Slemp (CITGO)
Prior to VGO reactor loading, CITGO projects the level of feed containments and we work with the catalyst vendors to customize the reactor catalyst system metals trapping capacity to achieve the desired run length with maximum value creation. We monitor our feed sodium along with other feed contaminants and estimate the projected level of metals trap saturation. Post reactor dumping, we validate the saturation projection via spent catalyst testing and modify the next catalyst system based on the spent catalyst contaminants level and the anticipated future feeds. As a side note, our historical observations show the feed testing indicates a higher level of sodium contamination than the spent catalyst testing validation. We also monitor our reactor products for indication of metals trap breakthrough such as increased light ends production and loss of volume swell as compared to design.
Vern Mallett (UOP)
Sodium usually enters a hydrotreater as a contaminant from improper desalter unit operation and/or caustic addition in the crude tower to neutralize high TAN feed stocks. Sodium adversely impacts the performance of all hydrotreaters so removing it from the feeds to the hydrotreater is the best solution. Nonetheless, upsets or specific crude runs may introduce enough sodium to VGO or residue hydrotreaters to cause a reduction in performance. Sodium predominantly affects HDS, HDN and HDA reactions. HDM and HDCCR are less affected. Thus, preventing sodium migration from the top bed and guard catalyst to the main active catalyst is important to maintain unit performance as long as possible.
In fixed bed units, Na can deposit both on the catalyst particle surface and within the catalyst pore structure of VGO and residuum hydrotreating catalysts. When depositing on the surface and interstices, the result is likely to be pressure drop build-up while deposition inside the particle generally results in reduced activity. Spent catalyst may accumulate 10 wt% or more of Na when deposited internally, depending on catalyst type and structure. Na is generally observed as Na2S crystals and in combination with Fe as FeNaS crystals. 1 wt% of Na deposited within the catalyst reduces activity by 10-20% and 5 wt% Na on catalyst results in 40-50% activity reduction.
Catalysts with high Na are unsuitable for regeneration since the heat treatment required to remove coke deposits allows the Na on spent catalyst to react with the alumina support. Surface area is drastically reduced during regeneration of high Na containing spent catalyst resulting in very low activity recovery.
Kevin Carlson (Criterion Catalysts & Technologies)
The refining and catalyst industry generally consider sodium to be an adverse feed contaminant resulting in catalyst fouling and deactivation. Criterion as well as other major catalyst developers continues to advise their client base to be aware of the potential impacts. Na can naturally come from crude oil or can be present in aqueous emulsion with the oil. Sodium affects catalyst activity within the cycle in which it is deposited as well as limiting the regeneration of Na contaminated catalyst for reuse. Presence of 1% Na2O on spent catalyst has been shown to reduce activity by more than 50%. It is recommended that efficient operation of desalting units is maintained, and regeneration is not recommended for spent catalysts containing more than 0.25% of sodium.
Data available on catalyst activity affected by deposition of sodium within the same cycle in which it was deposited is rather limited, making “quantification” of the impact difficult. In most of cases Na is carried into hydroprocessing units by aqueous emulsion with the feed. Sodium tends to deposit in the upper portion of the catalyst bed that can result in a crust that increases pressure drop and adversely impacts reactor flow distribution.
Greg Rosinski (ART)
Sodium (Na) is a severe catalyst poison that can cause significant activity loss even at low levels. It works by promoting the sintering of catalytic metals and neutralizing acid sites. Typical sources of sodium include a malfunctioning de-salter, sea water contamination or caustic contamination. Depending on the source of sodium, the signs of poisoning include rapid activity loss and an increase in pressure drop. The figure below shows the impact of sodium poisoning on catalyst activity.
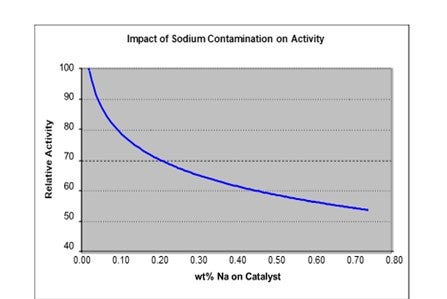
The figure indicates that for a sodium content of 0.5 wt% the activity is at most 60% of fresh catalyst activity. This translates to roughly 30°F loss in activity for 1 wt% sodium on the catalyst