Question 19: In your experience, what are the effects on ULSD hydrotreaters when FCC operation is adjusted to maximize diesel?
Praveen Gunaseelan (Vantage Point Energy Consulting)
There are a number of approaches to maximize the diesel yield from FCC units, such as catalyst optimization, process modifications, and changing the FCC product cut points. These approaches can be used independently or in combination - the ultimate objective being to maximize the production of light-cycle oil (LCO) from the FCC unit for subsequent conversion to diesel.
Increasing the LCO content in the feed to ULSD hydrotreaters can significantly impact their operation. FCC LCO is generally of heavier gravity and higher in polyaromatic content and requires more severe hydrotreating than conventional ULSD feedstock such as straight run diesel. As a consequence, ULSD units that process increasing amounts of LCO may require higher operating temperatures – potentially reducing ULSD catalyst life – and consume larger amounts of hydrogen than conventional ULSD feedstock. FCC LCO also has the effect of lowering the ULSD product cetane number, and thus the fraction of LCO in the ULSD feedstock may have to be limited to conform to product cetane specifications.
Some of the adverse impacts of processing LCO in ULSD units can be mitigated by reducing the LCO gravity and polyaromatic content in the FCC unit. This can be accomplished by a number of approaches such as using tailored FCC catalyst formulations, increasing the severity of FCC feed pre-treatment, and appropriately lowering the LCO endpoint.
Dan Webb (Western Refining)
LCO becomes easier to treat when the FCC is adjusted to maximize refinery diesel production as Main column cut point changes are made to drop the back end of LCN into LCO. Not only does the LCO fraction become lighter, it also contains a higher fraction of less refractive (sterically hindered) sulfur compounds. The table below shows actual feed blend stock component analysis shifts in FCC max gasoline and max distillate modes.
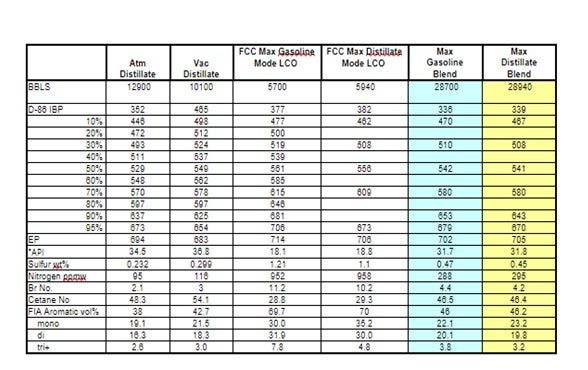
Haldor Topsoe used these actual component analyses to project DHTU catalysts performance. The following unit operating conditions were assumed to be constant.
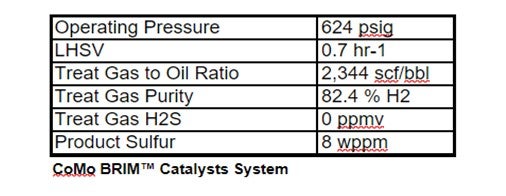
The projections below show that operating the FCC in max distillate mode produces a less severe DHTU feed stock: WABT is reduced by 3 -5 °F; 5-10% less H2 consumption; and catalysts deactivation may be reduced by as much as 20%.
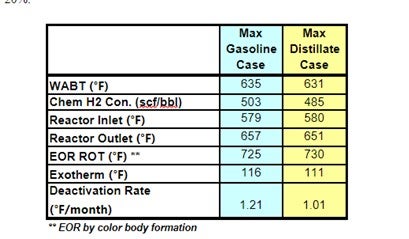
Larry Kraus (Criterion Catalysts & Technologies)
Adding heavy diesel barrels to the feed to a ULSD unit will make the feed more difficult to process in terms of sulfur removal. Heavy feed barrels will also make it more difficult to ULSD products to meet T90 distillation specifications as defined in ASTM D-975. Mild conversion (mild hydrocracking) is sometimes employed in ULSD units to meet distillation specifications. If cracking cannot be utilized due to hardware limitations for naphtha handling or naphtha economics are not favorable, then aromatics saturation is the primary means to shift distillation The number of heavy barrels that can be added to the feed is then constrained by the ability of the unit to meet distillation specifications via aromatics saturation, and possibly cold flow properties. The combination of deeper aromatic saturation combined with heavier feeds containing longer paraffins both exacerbate diesel cloud and pour point, in many circumstances requiring further adjustment.
There are several routes to improve the cold flow properties of distillates. The addition of kerosene and / or cold flow improvers to the diesel pool is the most widely applied routes. Chemicals are effective for pour point and CFPP improvement but have little effect on cloud point.
The amount of kerosene blending is flash point constrained. Light material blending can have a negative effect on some product properties such as cetane and sulfur (if using untreated kerosene). The loss of kerosene in the diesel or heating oil pools is typically not an economically attractive option.
Another approach is to install a catalytic dewaxing unit to selectively reduce the cold flow properties of selected refinery streams or to revamp an existing ULSD unit to accommodate a bed of a dewaxing catalyst. In most commercial applications, catalytic dewaxing of diesel is carried out in single-stage, series flow configuration where desulfurization is carried out prior to dewaxing. Such processes involve base metal dewaxing catalysts usually in sandwich configuration below HDS catalysts, with the dewaxing catalyst being used under severe conditions (i.e., in the presence of H2S, NH3, unconverted organic nitrogen and sulfur-containing molecules). Alternatively, a two-stage configuration employing a noble-metal, second-stage catalyst can be used to provide isomerization / cracking dewaxing. Typically, two-stage dewaxing provides significantly higher yields of higher quality products.
Criterion Catalyst & Technologies and Shell Global Solutions have been involved in numerous projects over the last decade to revamp or build dewaxing capability in refineries that need mild to severe cold flow improvement in their diesel pool.
Sal Torrisi (Criterion)
In maximizing LCO from the FCC, this typically means increasing primarily the LCO and also the HCN volume. We observe that these streams get less aromatic and have a higher API, in many circumstances due to a decrease in conversion or cracking intensity. The combined changes in volume and quality of LCO and HCN can have measurable impact on operation of the ULSD unit as described below:
- Desulfurization Performance – In general, the percentage of difficult sulfur species in LCO as well as the nitrogen content goes down as the volume is increased. If the LCO volume in the ULSD unit remains constant, then the feed blend can be easier to process, however it is a more likely scenario that the extra LCO is processed in the ULSD unit. The net performance of a higher volume of slightly easier to process LCO usually means higher temperature requirements, higher deactivation rate and shorter HDS catalyst life.
- Hydrogen Consumption – More, but less aromatic LCO, will still result in an overall increase in hydrogen demand for the refinery. If the LCO is to be upgraded into diesel, it will need anywhere between 600-1600 SCF/B of hydrogen depending on the operating severity of the ULSD unit. For newer, high pressure ULSD units having ample makeup and recycle hydrogen, this is usually a minor issue. For moderate pressure units, the extra volume of LCO may be a challenge to handle both from a hydrogen supply standpoint as well as from an operation standpoint. See deactivation comment.
- Catalyst Deactivation – Two of the variables that correlate strongly with catalyst deactivation are the quantity of polyaromatics passed across the catalyst and the hydrogen partial pressure. As the LCO rate goes up, so will the polyaromatic coke precursors. In addition, as the hydrogen consumption increases, the subsequent hydrogen partial pressure throughout the system will decrease. The combined effect of these changes can be a measurable increase in catalyst deactivation rate.
- Product Quality – With less aromatic LCO, the cetane of this component will increase. However, the increased quantity of LCO will typically overwhelm this higher LCO cetane to cause a lower overall ULSD unit feed cetane number. If the refinery diesel pool is not cetane constrained, then this is not an issue, but many refiners are pushing cetane limits today and even require additives to make specifications.
If the increased volume of LCO pushes the ULSD operation into a unit constraint, there are ULSD catalyst options available to manage cycle length, hydrogen consumption and even product quality, enabling refiners to maximize diesel volume by incorporating more of these challenging FCC products into the diesel pool.
Brian Watkins (ART)
Increasing the quantity of heavier boiling fractions (LCO, Coker, Light Gas Oils) to the diesel hydrotreater has a number of impacts both on the performance of the hydrotreater and on the resulting ULSD product properties. Higher boiling fractions typically increase the amount of hard sulphur compounds, as well as increasing the amount of nitrogen and complex aromatic species. This has the combined effect of lowering the product cetane and limiting end of run (EOR) by making it difficult to maintain diesel ASTM color. Since general hydrotreating reactions do little to shift distillation, only a small quantity of higher boiling materials can be placed into the pool to maintain the product distillation specifications.
With the use of a selective ring opening (SRO) catalyst as part of the catalyst charge ART is able to improve diesel product cetane numbers by reducing total aromatic and PNA levels. The addition of SRO catalyst also helps provide additional EOR life in terms of product color. A catalyst system utilizing a high activity NiMo (NDXi) coupled with a selective ring opening catalyst will provide the same HDS and HDN activity, while having the ability to process additional LCO and other higher boiling fractions as well as achieving higher aromatic saturation conversion compared to the hydrotreating catalyst alone.
The new SmART Catalyst System® with SRO catalyst capability is very effective for reducing aromatic rings found in heavier feedstocks providing improved cetane and color performance. The majority of this increase in traditional cetane upgrading is due to the saturation of poly aromatic compounds with some moderate amount of mono aromatic saturation. Saturating aromatic rings is an effective way to improve cetane, but there is a practical limit to the amount of cetane uplift that can be achieved. The reaction becomes thermodynamically limited near the end of the cycle resulting in a much lower level of cetane uplift and possible color problems. A better approach is aromatic saturation followed by selective ring opening. The resulting product has a higher cetane and lower aromatic and boiling point and avoids the issue of thermodynamic control at the end of the run. Additional information on this process can be found in the NPRA paper AM10- 166.
Advanced Refining Technologies (ART) is well positioned to provide assistance on how best to maximize unit performance and to take advantage of opportunities to successfully process more complex feeds into the ULSD pool. ART has developed catalysts specifically designed to handle more difficult feeds exemplified by the SmART technology for ULSD. The technology has been widely accepted and the addition of an SRO catalyst to the ULSD catalyst portfolio provides refiners with greater flexibility in the operation of their diesel hydrotreating units.
- Product Quality – With less aromatic LCO, the cetane of this component will increase. However, the increased quantity of LCO will typically overwhelm this higher LCO cetane to cause a lower overall ULSD unit feed cetane number. If the refinery diesel pool is not cetane constrained, then this is not an issue, but many refiners are pushing cetane limits today and even require additives to make specifications.