Question 19: What is the maximum recommended nitrogen content of reformer feed for continuously regenerated units? What is its impact on chloride consumption and ammonium chloride generation?
LAMBIE (KBC Advanced Technologies, Inc.)
The typical licensor guideline is 0.5 ppm maximum nitrogen in the feed. When nitrogen contacts the catalyst in the reforming unit, it essentially strips chloride from the catalyst. The reduced chloride on catalyst results in reduced catalyst activity. However, in most instances, the impact on the activity is not substantial. For example, 0.5 ppm nitrogen in the feed will reduce the catalyst chloride content by 0.02%. To put that in perspective, each ppm of nitrogen in the feed results in a reduction in catalyst chloride of about 0.003%; so the impact is fairly small. Nitrogen converts to ammonia upon catalyst contact, and the ammonia will react with hydrogen chloride in the recycle gas to form ammonium chloride salt.
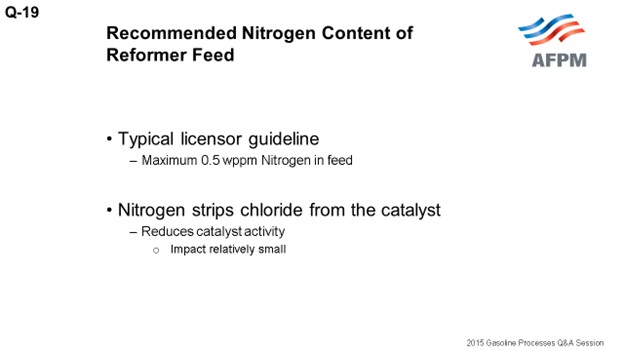
The salts that form will precipitate onto equipment, which will lead to fouling and potentially corrosion. The most common areas are the stabilizer trays where periodic waterwashing is required, but salts can also accumulate in compressors and fuel gas burners, as well as on combined feed exchangers, product condensers, and chloride guard beds. Some units can tolerate higher levels of nitrogen in the feed up to 0.5 ppm, while others have salting and fouling issues with 0.2 ppm nitrogen in the feed.
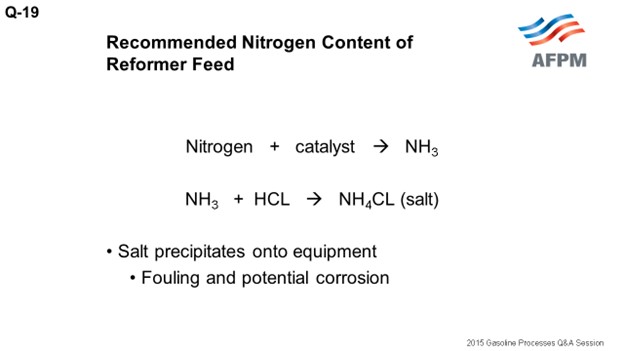
Basically, each refiner’s ability to handle the salt formation in the unit will dictate the tolerable level of nitrogen in the feed. In other words, the guideline is not meant for catalyst activity purposes but more for salt handling considerations.
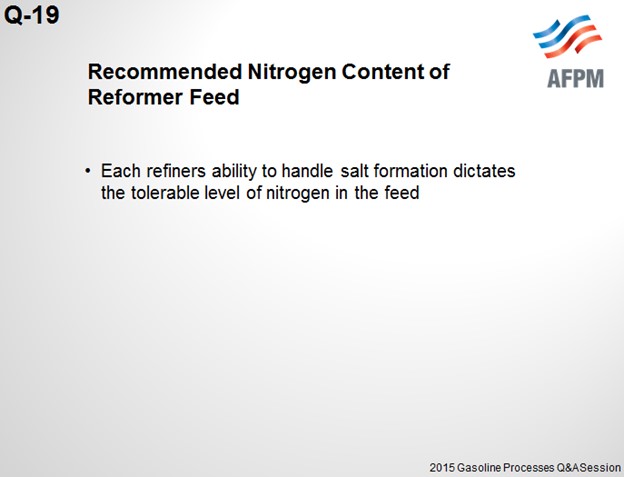
The ammonia produced, as I mentioned, reacts with HCl (hydrogen chloride) in stoichiometric balance. From that stoichiometric equation, you get the following relationships: 0.1 ppm nitrogen to feed produces 3.8 pounds of ammonium chloride salt. Or if you want to look at a different way, 0.1 ppm nitrogen to feed produces about 1,100 pounds of salt a year for a 30,000 barrel-per-day unit. And for every pound of nitrogen in feed, about 2.5 pounds of chloride is consumed or stripped from the catalyst. To put that in perspective again, 0.1 ppm nitrogen in feed results in a 0.003 reduction in the catalyst chloride content.
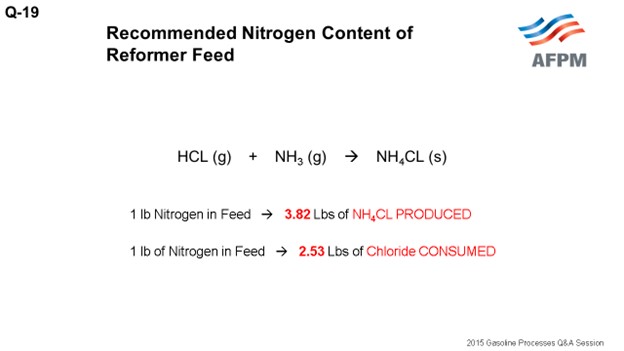
The plot on this slide shows the relationships of nitrogen in feed to salt formation and chloride consumed.
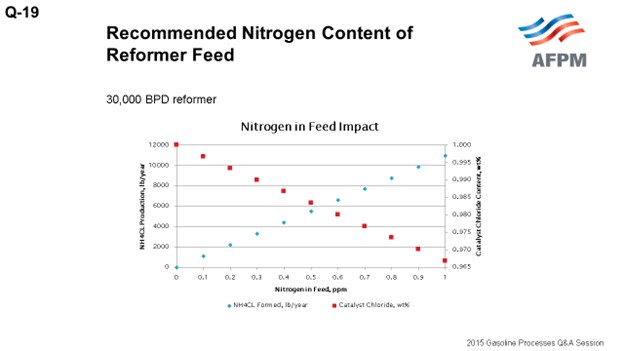
JUSTIN IRICK (GE Water & Process Technologies)
Do you have any experience with nitrogen speciation? Is it your opinion that all of the nitrogen in the feed converts to ammonia in the CCRs or does some sneak through?
LAMBIE (KBC Advanced Technologies, Inc.)
It has been my experience that most or all of the nitrogen in the feed gets converted to ammonia.
RATHINA SABAPATHI [Kuwait National Petroleum Company (KNPC)]
Do you have any information about the nitrogen content in advanced residue disulfide naphtha, which is the naphtha, because of the nitrogen turning pink? We are worried about that naphtha and would like to know if any speciation or anything else is done for the naphtha that comes from the residue hydrotreaters.
LAMBIE (KBC Advanced Technologies, Inc.)
I do not have experience with speciation of the nitrogen components in the naphtha boiling range from residue hydrotreaters.
SCOTT LAMBIE (KBC Advanced Technologies, Inc.)
A) The typical maximum recommended nitrogen content in reformer feed is 0.5 ppm. Nitrogen in the feed, when contacted with the catalyst, strips the chloride from the catalyst and converts to ammonia, NH3. The directional impact is reduced chloride on the catalyst and essentially lower activity due to the lower acidity.
In typical operations, the impact of the activity loss is not substantial. For example, the amount of chloride removed from the catalyst, assuming 0.5 ppm nitrogen in feed, is equivalent to reducing the chloride content by less than about 0.02 wt% (weight percent), or from 1.0 wt% chloride on catalyst to 0.98 wt%. The regenerated catalyst after additional chloride makeup is returned to 1.0%. A summary of the impact on catalyst chloride content is shown in the table below.
Nitrogen in the feed is typically managed more for salt production and fouling issues within the reforming unit than for catalyst activity debits. The salts that form will essentially wash through the system but will also accumulate in some of the equipment causing fouling; and in extreme cases, underdeposit corrosion. Some reforming units with feed nitrogen contents as low as 0.2 ppm have issues with salt formation and fouling, while others are able to manage at higher levels.
Each operator’s experience and ability to handle ammonium chloride salt formation will dictate the acceptable level of nitrogen in the feed. The effectiveness of water-washing the stabilizer trays to remove salts and the frequency required often dictate acceptable feed nitrogen levels.
The locations most often affected by salt formation and fouling are the net gas compressors and the trays in the stabilizer (debutanizer) column. Salt formation and fouling have also been experienced in reactor product condensers, fuel gas burners, and chloride guard beds in some locations. Combined feed exchangers are usually not affected by salt or fouling under normal conditions but may experience issues under certain conditions favorable to salt deposition.
B) The ammonia (NH3) produced from the nitrogen in the feed will react with hydrogen chloride (HCL) present in the recycle gas to form ammonium chloride salt (NH4CL) in stoichiometric balance per the following equation.
HCL (g) + NH3 (g) à NH4CL (s)
From this equation, the following relationships are formed:
-
For every 1 lb (pound) of nitrogen in the feed, 3.82 lbs of ammonium chloride salt is PRODUCED.
-
For every 1 lb of nitrogen in the feed, 2.53 lbs of chloride is CONSUMED.
For a 30,000 BPD reformer:
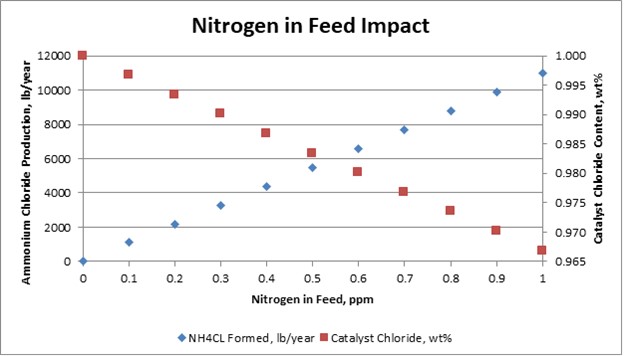