Question 19: What are your Best Practices for recovering from high coke on spent catalyst in continuously regenerating reforming units?
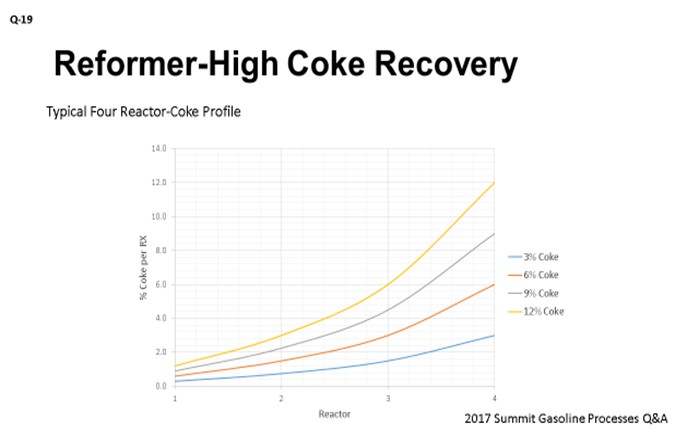
PETER ECKELS (Honeywell UOP)
The Honeywell UOP Platforming™ CCR regenerator is designed to burn 5 wt% (weight percent) carbon off catalyst circulating at 100% of the design rate. Most units can successfully burn off significantly more coke than design at normal operating conditions when the screens are clean and regeneration gas flow is uniform. Note that if there is screen fouling or some other condition leading to non-uniform or reduced flow, the coke-burning capacity would be reduced.
Coking rate and coke combustion must stay in general balance across the unit. If coke is high due to the reactor-side operation (rather than an extended outage of the regenerator), the severity in the reactors should be moderated to reduce the rate of coke formation. Refinery Economics and Planning personnel will need to adjust to allow for reduced severity. Depending on the cause of the coke imbalance, it may take several catalyst cycles (i.e., days or weeks) to re-balance the unit and resume normal operations.
The first option for burning high coke is to operate the regeneration tower in black-burn mode with reduced catalyst circulation. The reduced circulation rate allows more residence time to burn off the high coke levels; however, the reactor coking rate may need to be reduced.
If there is too much coke on the catalyst to burn in a single pass through the regeneration tower, it may be necessary to operate in a partial-burn mode. The total weight of coke burned in this operation can be more than during normal complete-burn because diffusion does not limit oxygen availability to the same extent; however, coke would remain in the center of the catalyst pills. In this case, more care should also be taken when the partially burned catalyst comes back for another pass in the regenerator. The remaining coke from the partial burn may be more difficult to remove and black burn should continue until full combustion of coke in the burn zone is verified.
In either case, operations in black burn should be limited because the metals on the catalyst will agglomerate without the redistribution that is normally accomplished in the chlorination zone. At some point, this agglomeration will affect the catalyst performance (activity, selectivity, and stability). Metals agglomeration can typically be reversed through operation in white burn, but it may take several cycles to return to optimum catalyst condition.
If the coke level of the spent catalyst has increased to an excessively high level or if part of the catalyst inventory (whether this high coke catalyst is grouped together or distributed throughout the catalyst bed) has significantly more coke than the rest, UOP recommends contacting your UOP regional services manager to discuss the appropriate path forward. In special circumstances, other techniques have also been used to resolve high coke situations.