Question 19: Since API-932 (Waterwash Best Practices) was published, what has been the impact on reactor effluent air cooler washwater system design and reliability? Are there any active or ongoing studies to improve waterwash systems, in addition to API-932?
BODOLUS (CVR Energy)
The question of issues associated with waterwash has been discussed since the API-932 was issued. This first slide gives a little chronology of some of the documents. There have been a lot of documents issued since the 932 was first published in 2002. Back then, it was called “a Study of Corrosion in Hydroprocessing Reactor Exchange Air Cooler Systems”. Part B about guidelines came out in 2004. The 932-B got republished and updated in 2012 and now refers more to design materials, fabrication, and operations of inspection guidelines. During this period of time, there has also been the issuance of the recommended practice about damaged mechanisms affecting fixed equipment in the refining industry. Section 5 thoroughly covers many aspects of reliability enhancement in REAC (reactor effluent air cooler) systems.
NACE (National Association of Corrosion Engineers)
is getting ready to come out with a very detailed report on the refinery injection: actual quills, design of the quills, designs of the manifolds, how you kick velocities, and all of the really technical details. So, in addition to API 581, all of these have been coming together in the risk-based inspection (RBI) programs.
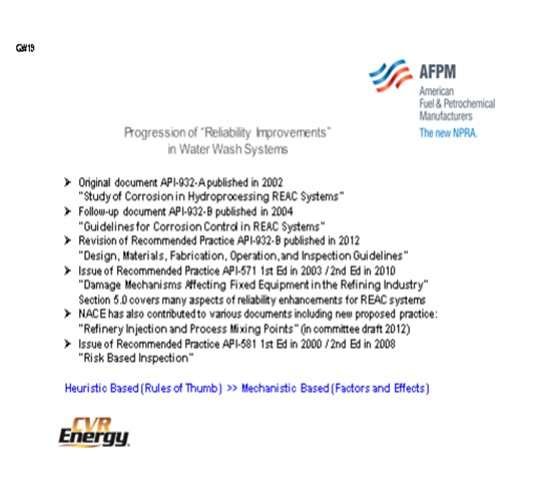
In a nutshell, years ago, the waterwash systems and reliabilities of waterwash were based on mere heuristics, rules of thumb. Guys would say, “Well, I have so many gallons of water for so many thousands of barrels of feed.” Now it is my opinion that this has now gone to a mechanistic-based response through technology where people take a look at their effects in terms of waterwash because the damage mechanisms and prospects for catastrophic failure in hydrotreaters, in this particular area, are very high for a number of different damaged mechanisms.
The next slide also appears in the Answer Book. I sat down and thought, well, what else is involved? I just tried to get awareness. Moving from heuristics to mechanic-based, you have to be a lot more cognizant of the chemistry that might be occurring. At the top of the triangle, you have hydrogen sulfide. It is always going to be there. In the bottom right, you have ammonia, which will always be there with the nitrogen and the feeds.
As one of the new players in the game, chlorine plays a competitive role in all of this. I do not know whether it is just due to awareness, availability, the existence of more chlorides in crudes and in intermediates, or more chloride leakage from your CCR. Chlorine is competitive with H2S for iron. There are various things going on. The iron chlorides are very corrosive.
I want to encourage people by saying that because water is in the middle of all of these, you must bring adequate water and use enough to dilute out the solution, with respect to the regular type guidelines. You also need to be cognizant of the fact that there are a lot of new issues of which people are more aware; particularly, as I said, chloride and ammonium chloride. The rough thing about ammonium chloride is that it often deposits in areas of the heat exchanger system, which is not typically accessible with your current waterwash systems. So, you often have to do an intermediate or temporary waterwash.
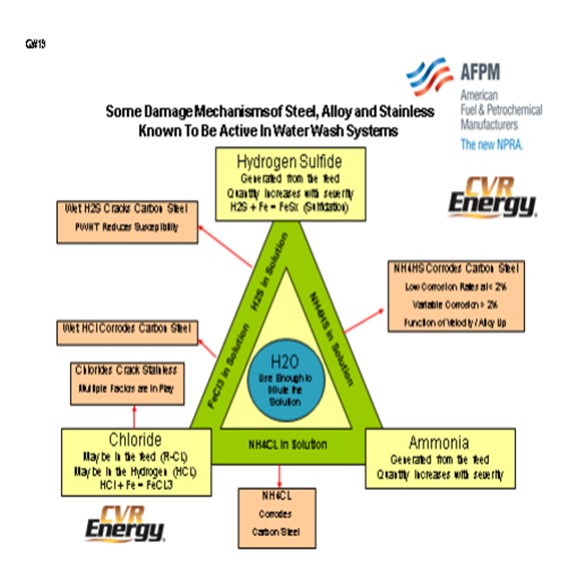
Some general guidelines on maximum velocity for tubes with a given salt concentration, primarily ammonium bisulfide salts: Again, you need to assure that the distribution of the water upon injection has been balanced throughout your manifolds. It is a very highly technical topic these days, so just be aware that there is a reference list published in the Answer Book. Feel free to dig up those references and read them because it is gotten very, very, very good in recent years.
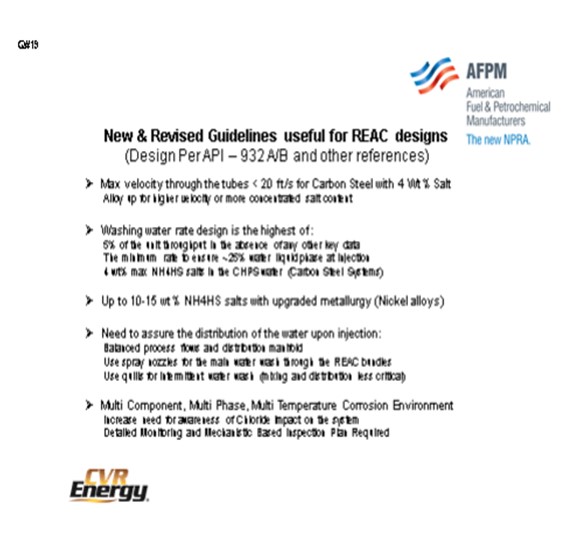
PUI-NANG LIN (Flint Hill Resources, LP)
One of the questions on the waterwash system that we often have is: What kind of guideline do you use in case of a loss of the water pump? Also, how do you decide the length of time you can run without waterwash before you have to pull feed?
LEICHTY (Chevron USA, Inc.)
It depends on the concentration of ammonium bisulfide. My response to Question 25 includes a slide I have prepared to answer that question.
BODOLUS (CVR Energy)
The original API-932-A document was published in 2002, and there have been numerous publications since then that address washwater systems of reactor effluent air coolers (REAC) and associated equipment including:
1. Follow-up document API-932-B published in 2004: “Guidelines for Corrosion Control in REAC Systems”.
2. Revision of Recommended Practice API-932-B published in 2012: “Design, Materials, Fabrication, Operation, and Inspection Guidelines”.
3. Issue of Recommended Practice API-571 1st Ed in 2003/2nd Ed in 2010: “Damage Mechanisms Affecting Fixed Equipment in the Refining Industry”.
4. Section 5.0 covers many aspects of reliability enhancements for REAC systems.
5. NACE has also contributed to various documents including new proposed practice: “Refinery Injection and Process Mixing Points” (in committee draft 2012).
6. Issue of Recommended Practice API-581 1st Ed in 2000/2nd Ed in 2008: “Risk-Based Inspection”.
The newer publication is not so much a revision of the old document as they are a refinement and improvement in the knowledge base of corrosion factors and the abatement techniques that can be implemented. Older guidelines based on Heuristics (Rules of Thumb) have been replaced with a better understanding of the Mechanistic (Factors and Effects) driving the damage pathology.
From my perspective, there has been a broadening awareness of the key chemical interactions taking place in hydrotreaters reactor effluent environment. We are all aware that iron, iron sulfides, hydrogen sulfide and Ammonia play key roles in corrosive action in reactor effluent reactor air coolers, but the prevalence of chloride adds another dimension of complexity. (see Damage Mechanism Slide)
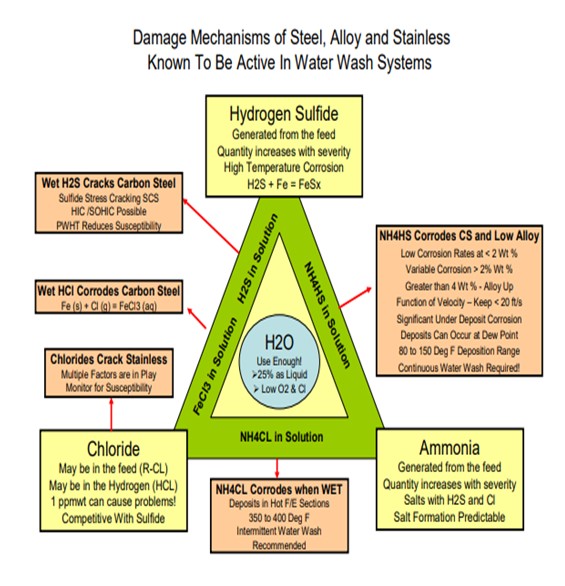
The general focus has been on the corrosive nature of ammonium bisulfide (NH4HS) in aqueous solution but additional attention is being given to ammonium chloride (NH4CL) fouling that typically occurs in process regions not services by continuous waterwash systems. As little as 1 wppm chloride in the feed will cause NH4Cl deposition in the reactors effluent circuit of hydrotreating units, depending on the feed nitrogen and the unit operating pressure.
Fortunately, NH4CL deposits areas in hotter sections of the feed/effluent exchange system (350°F to 400°F) where inherent water dew point is not an issue. As the process stream approaches temperatures consistent with reactor effluent air coolers, water dew point can occur at NH4HS deposition temperatures (80°F to 150°F). Initial depositional aqueous fluids can be very corrosive with localized rates enhanced by velocity, H2S partial pressures and/or the presence of chloride.
Introduction of sufficient, controlled quality (free of dissolved O2 and chloride) water, in the specific process location upstream of the inherent dew point, with a well-designed distribution system has shown to be the primary means to control ammonium salts. Detailed process chemical modeling of the reactor effluent stream needs to be combined with mechanical and physical aspects of the injection point design to generate an effective abatement plan. The plan needs to be monitored on a continuous basis for key process variables of water flow, resulting salt concentration in washwater loop and exchanger network DP build. Suspected corrosion regions need to be inspected online, as able, on a defined interval commensurate with known mechanical risk factors (velocity and geometry) and thoroughly inspected at turnaround opportunities. Vigilance needs to be paid to all known and potential damage mechanisms in the exchanger equipment and piping system including general and localized corrosion, SCC, HIC, SOHIC, chloride stress cracking, and hydrogen blistering.
Guidelines are still useful for REAC designs using carbon steel, with a max velocity through the tubes less than 20 fps (typical API-932 recommendation) for 4 wt% salt.
Washwater rate design is the highest of:
- 5% of the unit throughput in the absence of any other key data,
- the minimum rate to ensure ~25% water liquid phase at injection,
- 4 wt% max NH4HS salts in the CHPS water (carbon steel systems), or
- up to 10 wt% to 15 wt% NH4HS salts with upgraded metallurgy (nickel alloys). You need to assure the distribution of the water upon injection by
- Balancing process flows and distribution manifold,
- Using spray nozzles for the main waterwash through the REAC bundles, and
- Using quills for intermittent waterwash (mixing and distribution less critical)