Question 18: What considerations are being given to include mild hydrocracking in your high pressure ULSD unit?
Kaspar Vogt (Albemarle)
Due to the increasing global demand for diesel, the ability to reduce product density (increase volume gain) and blend a significant amount of heavy diesel and/or light vacuum gasoil in the ultra-low sulfur diesel pool represents a large economic advantage. These economic gains could potentially include margin increases of tens of millions of dollars per year for a refinery.
Typical mild hydrocracking units operate between 800 and 1200 psig with a conversion level of around 30%. The cracking catalysts selected in lower pressure units are amorphous silica alumina catalysts. Zeolitic catalysts are applied in higher pressure operations. We have extensive experience in mild hydrocracker (MHC) operations including maximizing USLD production and/or maximizing density reduction.
Normal hydrotreaters are not designed for hydrocracking and below we list the issues to address when converting the ULSD unit to a mild hydrocracking unit. First and foremost, the safety of the employees, community, and equipment needs to be considered. The risk of a temperature run away is very limited in hydrotreaters, while in hydrocracking it can happen if the proper precautions and counter measures are not in place. The measures include:
- Proper emergency shut-down procedures
- Operator training
- Good liquid and gas distribution
- Well-designed quenches
- Proper unit control with advanced control systems
It is important to be conscious of the typically large lag time in the unit and the fact that relatively small changes of the process parameters can result in considerable cracking bed responses.
Also important in the evaluation is the presence of or access to sufficient hydrogen to the unit and a thorough review of the fractionation section. The increased conversion will lead to increased light end yields. The unit separation equipment must be able to accommodate these higher yields in the reactor effluent.
By adding hydrocracking catalysts in the existing unit, a catalyst system needs to be designed to offset the activity loss of the hydtrotreating catalysts that are displaced. Such measures include the usage of higher activity pre-treatment catalysts similar to those used in hydrocracking.
The hydrogen partial pressure does not need to be very high. For example, a commercial unit processing diesel with LVGO at a total reactor inlet pressure of 750 psig accomplished 50% 660 deg F conversion and 9.5 deg API density reduction. In this example, the hydrogen consumption roughly doubled.
In general, higher pressure will promote better yields and product properties. For each case, we need to calculate the performance and/or conduct pilot plant testing to determine the product properties based on the conditions, feeds, objectives and limitations at the refinery.
Martin Gonzalez (BP)
A distinction must be made between hydrocracking of diesel to produce gasoline vs. selective ring opening as a way to improve properties of finished diesel. Recent diesel margins have sparked an interest in the latter as a way to enable a higher volume or quality of finished diesel products. This may be particularly important for refineries shifting to cheaper, lower quality crudes, where it can be difficult to meet specifications related to aromatics like cetane number, smoke point, and naphthalene content. Mild hydrocracking in a ULSD unit may be effective for improving product cetane index and volume swell above what can be achieved by ring saturation alone. In addition, the byproduct naphtha may be higher in octane than a typical virgin naphtha. The draw-back is that hydrogen consumption is likely to be greater. Several licensors offer technology that incorporates mild hydrocracking with an incremental H2 consumption that is relatively small.
Shankar Vaidyanathan (Flour)
I will limit my comment to mild hydrocrackers with at least a 20% conversion objective. I will exclude diesel units that have a sandwiched catalyst system for cold flow property improvement.
We frequently study the option of including mild hydrocracking in high pressure ULSD units during the planning phase. Though technically feasible, the option is economically unattractive since the primary objective is treating distillate stock to ULSD specification. Volume preservation is of paramount importance so distillate cracking to naphtha is not desired. From this perspective, the ULSD unit is viewed as an environment unit and so the refiner’s objective is to minimize the overall investment for ULSD production. In order to include mild hydrocracking in ULSD unit, pre-investment for pressure, reactor, compressors and separation equipment is required. Depending on the specific refinery’s economic considerations, some refiners have even converted their distillate hydrocrackers to ULSD treating service.
On the other hand, if the primary objective is to make incremental ULSD by including mild hydrocracking of higher boiling gas oils and not distillate stock, a ULSD reactor can be efficiently integrated within a new mild hydrocracker (MHC), cat feed hydrotreater (CFH), or hydrocracker (HCK) unit. This is a standard option that we study for new hydroprocessing blocks as a means of optimizing capital investment. Integration of a ULSD reactor in a unit processing gas oils may make economic sense if incremental refractory distillate is available for upgrading. It may be preferable to hydrocrack heavy cracked stock than treat in a ULSD and so an economic cost-benefit analysis needs to be carried out.
Robert Wade (ART)
Many refiners consider complimenting their existing ULSD HDT catalyst with a hydrocracking catalyst to improve cold flow properties. This is accomplished through end point reduction. The hydrocracking catalyst used is usually the type that preferentially cracks large straight chain paraffins. For properly designed catalyst systems this will be economic as heavier feeds may be processed while meeting stringent diesel cold flow properties, and simultaneously not severely reducing diesel selectivity.
Some refiners find it economic to retrofit their existing ULSD units so that they can run full range VGO. This option is very dependent on the design pressure of the reactors as the fouling rate will be considerably higher for a VGO service. In addition, the capital expense required to meet recovery section requirements may be a major consideration.
Raj Patel (Haldor Topsoe, Inc.)
Mild hydrocracking can be added quite simply to many ULSD reaction systems. The rapid advance in Topsoe USLD HDS and HDN catalyst activity as a consequence of BRIMTM technology means that room can be allocated in reactors for new functional catalyst systems to enhance performance. Topsoe catalysts such as TK-578 BRIMTM (CoMo) and TK-607 BRIMTM (NiMo) are as much as 50% more active than the catalysts applied in the first wave of ULSD units.
The benefits of hydrocracking include the following:
- Incremental heavy gas oil conversion to diesel and lighter products (end point shift)
- Incremental product density reduction and cetane uplift
- Viscosity reduction
- Cloud point improvement
The reaction system illustrated below shows the substantial improvement in density and cetane quality as a consequence of aromatic saturation. The addition of hydrocracking ring-opening chemistry provides substantial incremental improvement with a relatively modest incremental cost of hydrogen.
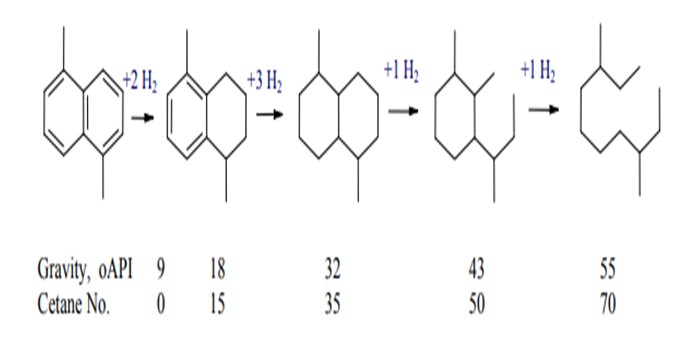
The sequence of aromatic saturation and ring opening will give a reduction in boiling point of as much as 100o F. This very large reduction in boiling point means that extra gas oil boiling above the normal diesel cut point can be recovered and then shifted into the ULSD product pool.
Haldor Topsoe can offer catalyst formulations that give both conventional hydrocracking performance and also hydrocracking with enhanced isomerization function to improve the cold flow properties of the distillate together with cetane improvement and end point shifting. An example of this performance is shown in the figures below. A high density (27o API) high end point (700o F T95) gas oil feedstock is first desulfurized to ULSD level and then hydrocracked over catalyst with enhanced isomerization function. At modest levels of conversion to naphtha, the density, distillation, cloud point and viscosity of the feed are improved significantly.
Hydrocracking catalysts can be applied in stacked systems with hydrotreating catalysts under moderate pressure levels as low as 700 psig in the reactor. A key consideration is the HDN performance of the pretreating catalyst allowing deep hydro-denitrogenation in addition to deep hydro-desulfurization. The proper allocation of both hydrotreating catalyst and hydrocracking catalyst will optimize performance and cycle life.
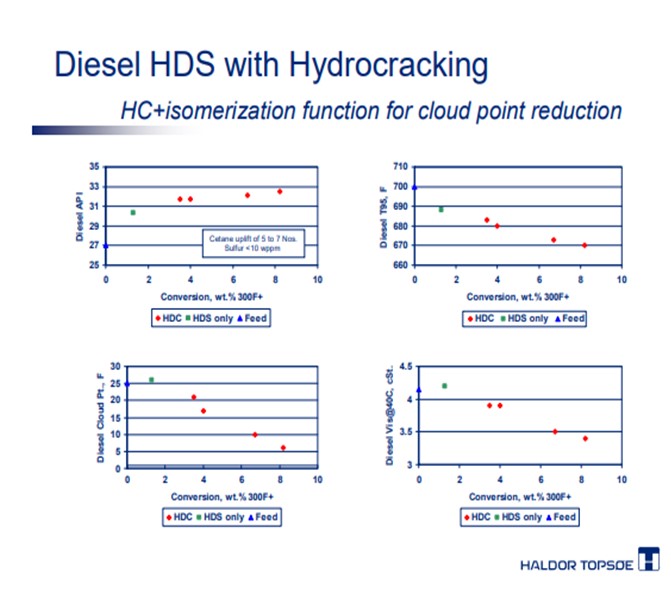
Haldor Topsoe can offer both CoMo and NiMo catalysts with the highest activity for deep HDS and HDN in the refining industry. Further product uplift can be achieved by the application of hydrocracking and isomerization chemistries utilizing Topsoe’s Hydrocracking and dewaxing catalysts specifically designed for heavy distillate upgrading.