Question 16: What is the commercial experience on the use of H2 membranes in hydrotreaters or hydrocrackers for H2 recovery? What is a reasonable membrane life given the sensitivity to fouling and temperature changes?
ESTEBAN (Suncor Energy, Inc.)
At the Denver Refinery, we have a few hydrogen separation membranes. We call them our hydrogen purification unit. Our #3 HDS, which is currently our ULSD unit, was previously a gas oil hydrotreater until we revamped it in 2006. So the HPUs (hydrogen purification units) were in consistent service from 1990 to 2006. We do not have the ability to use them today because they purify the hydrogen from our purge gas stream before it goes to fuel, and the purified hydrogen stream is sent out to the suction of the makeup compressor; but typically, we operate the unit at makeup capacity limits.
That being said, the membranes themselves are fairly simple to operate and can have extremely long lifecycles. The primary issue that has caused us to replace our membranes has simply been how we treated them rather than the overall operation of the membranes themselves. So, in order to have solid membrane performance, we have found that particulate filtration, liquid coalescing, and operating temperature are key.
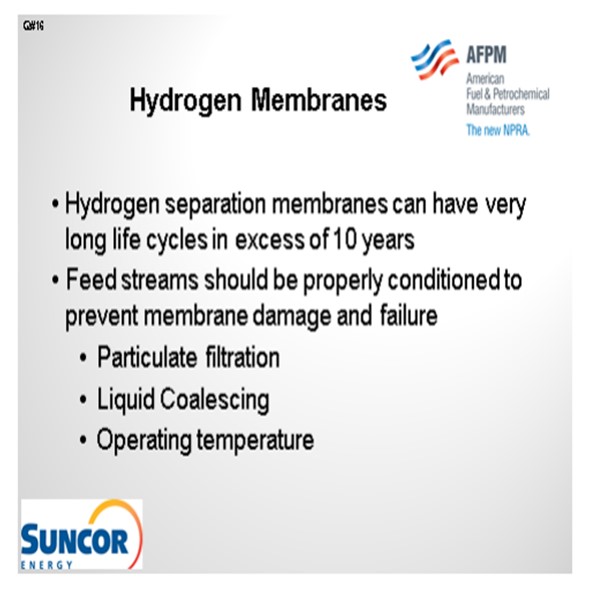
So it is a gas-conditioning issue more than an issue with the membrane itself. These membranes typically come on skids, which is the location of both of our membranes units. On the skids, you need to pay attention to the coalescing filters, and then the heat exchange that is used to condition the gas upstream of the membrane, in order to get the efficiency according to the design. We have been able to achieve efficiency in the 99% pure range, but that comes with a large purge stream to our fuel system. That is why we do not necessarily operate them today the way they were designed.
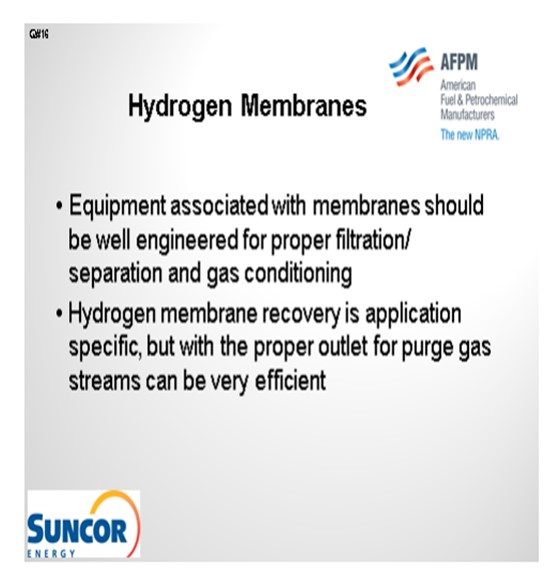
OHMES (KBC Advanced Technologies, Inc.)
I want to make a quick comment to build on what James said. Based on our experience, the main issue, again, is making sure you do not have a liquid phase form on the membrane. So do a quick simulation check, and make sure that the preheat temperature is sufficient to stay keep your vapor-phased throughout the membrane.
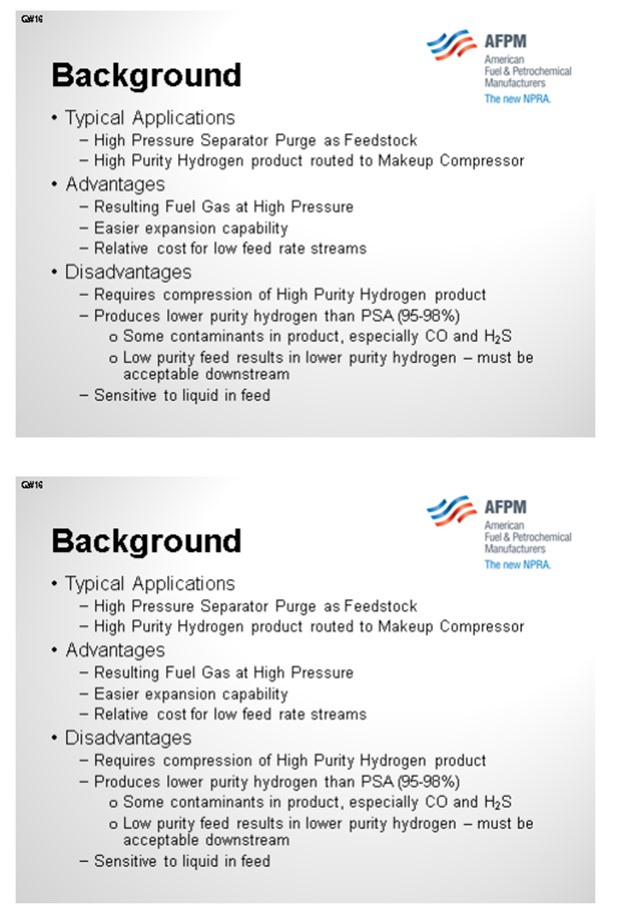
ESTEBAN (Suncor Energy, Inc.)
Hydrogen membranes in the right application can be very valuable for recovering hydrogen in hydroprocessing units. The actual recovery membrane requires very little maintenance and can provide extremely long life cycles provided the feed gas is treated and conditioned properly. The Suncor Energy, Inc. Denver Refinery has a membrane system used to recover hydrogen from a purge gas stream off of the #3 HDS, a high pressure hydroprocessing unit. The hydrogen purification unit (HPU) is fed gas from downstream of the amine contactor in the high pressure loop of the #3 HDS, where the recovered hydrogen is fed to the makeup compressor for reuse in hydrotreating and the residue gas is sent to fuel. The HPU (hydrogen purification unit) was installed with the #3 HDS when it was constructed in 1990 and was in continuous operation until a revamp of the unit in 2006 to swap services from gas oil hydrotreating to ULSD. Up until 2006, the #3 HDS was fed reformer hydrogen as makeup gas and the makeup compressor had excess capacity to accommodate a purge stream to operate the HPU. Under current operating conditions the makeup compressor is fed hydrogen plant hydrogen and is at maximum capacity, unable to accommodate a purge stream from the unit. That being said our experience with regard to membrane reliability has been good. We have had to replace the membrane on a few occasions due to poor gas filtration and elevated operating temperatures. While the membrane itself is not a maintenance concern, care should be taken to ensure that the feed gas is free of liquids and particulates. In addition, the feed gas must be conditioned to the proper operating temperatures and proper operating pressure differentials as specified by the manufacturer. In our experience, poorly designed equipment and systems situated around a good membrane result in unsatisfactory performance and cause us to address filtration, heat exchange, and instrumentation issues to improve HPU performance.
OHMES (KBC Advanced Technologies, Inc.)
KBC has had experience with refiners applying membranes in the hydrogen recovery scheme. Typically, membranes are used on high hydrogen content streams that are already at high pressure, such as a high pressure recycle gas purge stream on hydrocrackers, resid processing units, or gas oil hydrotreaters. For these applications, the high-pressure purge is taken from the amine scrubber and routed through a pretreatment scheme prior to going through the membrane. The resultant high purity hydrogen is routed back to the unit makeup gas compressor, due to its low pressure, and the higher pressure reject gas is sent to downstream fuel consumers.
Compared to other hydrogen recovery options, such as PSA or cryogenic, membrane recovery units have the following advantages and disadvantages:
• Advantages:
o Resulting fuel gas at high pressure
o Easier expansion capability
o Relative cost for low feed rate streams
• Disadvantages:
o Requires compression of high purity hydrogen product.
o Produces lower purity hydrogen than PSA (95% to 98%) due to the existence of contaminants in the product, especially CO and H2S.
o Low purity feed results in lower purity hydrogen, which must be acceptable downstream.
o Sensitive to liquid in feed.
KBC’s experience is that membranes can be part of a refinery hydrogen recovery scheme, but they are not typically used. The application of membranes is strongly driven by the hydrogen system configuration. Most often, membranes have been applied in configurations where relatively small volumes of high hydrogen contact gas are available, where hydroprocessing units have spare makeup gas compressor capacity to re-compress the resultant membrane hydrogen product, and where the high-pressure hydroprocessing units receive all of the facility hydrogen “as-is” and can use membranes to do “slipstream” purification.
Typical experience is that the membranes last at least 10 years, as long as the feed is properly conditioned prior to processing through the membrane. The recommended practices for feed preparation are:
• Include cooler and knockout drum with demister to remove bulk liquids and condensables.
• Consider feed filter/coalescer to remove solids and liquids.
• Reheat feed above dew point to vaporize trace liquids directly before the membrane and avoid liquid deposition on the membrane.
So, membranes can be a reliable part of an efficient hydrogen recovery scheme. Additional details on hydrogen system optimization can be found in the materials from the 2011 Principles & Practices Hydrogen Management Issues session, which was conducted by Rick Manner with KBC Advanced Technologies, Inc.
TIM LEBRECHT (Air Products and Chemicals)
Membranes have been used for hydrogen recovery from hydrotreaters and hydrocrackers since 1980. Air Products has provided nearly 90 PRISM® Membrane systems for hydrogen recovery within oil refineries and, including systems sold by its competitors, there are probably more than 150 systems installed around the world. In fact, the membrane process within hydrocracking has been promoted from just an add-on process to an integral part of the process where membrane failure would mean failure of the whole hydrocracking process. With a correctly designed system to cope with non-permeate hydrocarbon dew points, Air Products expects at least seven years of operation before a partial (10%) membrane replacement begins.