Question 16: How are you performing in-situ sulfiding for hydroprocessing catalysts protecting your waste water units from water soluble organic chemicals and their fuel gas system from non-decomposed mercaptans?
RANDY ALEXANDER and JIM ROBINSON (Reactor Resources LLC)
DMDS decomposes over a CoMo or NiMo catalysts at reactor temperatures in the range of 400-460F, forming H2S and CH4. The exact temperature needed to achieve complete decomposition is dependent on the pressure, the catalyst type, and the space velocity in the reactor. For example, full decomposition is achieved above 430F with a pressure of 300 psi and a space velocity of 1.0 hr-1. At a lower pressure and a higher space velocity, the full decomposition temperature for DMDS will approach 445F.
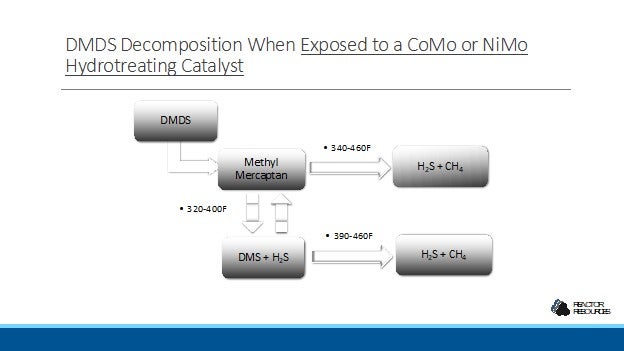
.
There are several approaches that can be utilized in order to avoid issues with non-decomposed mercaptans in wastewater and fuel gas systems.
The easiest solution to this issue is a carefully controlled sulfiding process which begins with updated procedures that include modern control technologies and real-time measurements to manage the process.
Essential control elements include:
-
Real-time H2S measurement.
-
Transparent and accurate real-time sulfiding agent measurement.
-
A reliable means to control the injection rate.
Secondary elements that may also be of benefit:
-
Real-time Hydrogen Purity measurement
-
Total Sulfur measurement
-
Properly deployed, these elements will provide the sulfiding team with enough information to control the in-situ sulfiding activities during start up and avoid the release of non-decomposed (non-H2S) mercaptans to the fuel gas or flare header. This goal can be achieved with any of the sulfiding chemicals normally used (DMDS or TBPS).
It is imperative that the sulfiding team resist the temptation to inject DMDS at a high rate early low temperature stage of sulfiding. Over injection at low temperatures can lead to excessive recycle gas density and low hydrogen purity, driving the need to purge sour gas and add make up hydrogen in order to avoid a compressor trip or catalyst damage due resulting from low hydrogen partial pressure. The sulfiding team should consider moving bed temperatures up to 450F as soon as is practical in order to facilitate full decomposition of mercaptans in the recycle gas.
Purging of sour gas should be avoided if reactor beds are below 450F. Instead, the pressure of the recycle stream should be increased, if possible, in order to facilitate decomposition. if an increase in system pressure is not possible, DMDS injection should be paused while temperatures are increased.
Of secondary concern is the H2S concentration in the recycle gas stream after breakthrough. There is no technical reason to allow H2S concentrations to rise above 10,000 ppm. In fact, any H2S in excess of 1000 ppm is not necessary for good catalyst activation. Levels above 1000 are artifacts of a “safety net” approach developed when older, less timely and less accurate methods of H2S measurement were utilized (e.g., Draeger tubes).
In the absence of the above essential elements, there are other sulfiding chemicals, such as polysulfides or polysulfide blends, that do not produce mercaptans during decomposition. These poly-sulfides, such as di-tert-butyl polysulfide (TBPS), have both positive and negative attributes, but can be used alone or in conjunction with dimethyl disulfide to effectively mitigate mercaptans in fuel gas or flare systems. Full decomposition of TBPS will occur at 325F to form H2S and isobutane. However, due to the lower sulfur density of TBPS (54% versus 68% for DMDS), 25% more chemical will be required to completely sulfide the catalyst bed. Furthermore, due to supply interruptions and erratic market demands, poly-sulfides are typically more expensive and require a longer lead time to be assured of availability.
The last option for avoiding mercaptans downstream of the process, ex-situ catalyst sulfiding, is also the most expensive option. The ex-situ sulfided catalyst is loaded in the active form. Therefore, no sulfur spiking agents need to be injected into the process and the possibility of mercaptans generation during start up is virtually eliminated.
In closing, there are no technical reasons why a modern refinery using current sulfiding techniques should experience issues with mercaptans in the fuel gas or flare header unless there is a unit upset. Over-injection of the sulfiding agent below 450F will exacerbate the problem. Good planning prior in advance of start-up and close attention to detail during injection will typically lead to a successful result.
ROBERT STEINBERG (Motiva Enterprises)
During in-situ catalyst sulfiding di-methyl disulfide (DMDS) or other chemicals like tertiary butyl polysulfide (TBPS) are used to generate H2S to activate the catalyst. These chemicals break down to form H2S and light hydrocarbons. However, the breakdown is not complete. DMDS will decompose to methyl mercaptan and some dimethyl sulfide as well as methane and H2S. TBPS will decompose to tertiary butyl mercaptan as well as butane and H2S.
A small amount of the sulfur in sulfiding agent stays as mercaptans when it leaves the reactor, particularly at initial sulfiding temperatures. While much of these mercaptans are recycled back to the reactor some may leave the unit in:
-
High pressure recycles gas vent.
-
Low Pressure Separator vent
-
Stripper vent
-
Charge Surge Drum vent
-
Sour water from Cold Separator
-
Sour water from Stripper Reflux Drum
-
Stripper bottoms sent to tankage and tank vents.
Gas vents to fuel gas are normally scrubbed with amine before being used in furnaces. Amine will remove H2S but not mercaptans. These mercaptans contribute to total sulfur in fuel gas. H2S analyzers on fuel gas will not detect these mercaptans but SO2 analyzers on flue gas will. Regardless of whether the sulfur is detected it will be present in heater flue gas.
If the mercaptans are water soluble they can leave the hydrotreater unit in sour water or get knocked out upstream of the fuel gas scrubber. If such knockout streams are sent to slop, water soluble chemicals can be drawn off from tanks and routed to wastewater treating or routed to crude units and end up in desalter water. Regardless of how the chemicals get into water they will end up in the wastewater treating plant.
DMDS and TBPS are both insoluble or only slightly soluble in water as are decomposition products dimethyl sulfide and butyl mercaptan. However, methyl mercaptan is soluble in water.
There is limited data on how much DMDS will not break down to H2S during sulfiding. It is clearly dependent on operating pressure, LHSV, type of catalyst and maybe other variables as well. As reactor temperatures are raised above 460-500°F for high temperature sulfiding, essentially all the DMDS decomposes to H2S.
There is some indication that sulfiding hydrocracking catalysts without hydrotreating catalysts, such as in a 2nd stage reactor, results in more of the DMDS sulfur getting into fuel gas as mercaptans. The reason for this is not clear but possibilities include:
-
Catalysts containing tungsten do not break down DMDS as well.
-
Zeolite catalysts do not breakdown DMDS as well.
-
Hyper-active sites that have not yet been titrated crack feeds even at initial sulfiding temperatures while temperatures are too low to hydrotreat these products, this implies the mercaptans come from sulfur in feed and not the sulfiding agent. On some occasions, mercaptan species that would not be created by breaking down sulfiding agents have been detected in fuel gas when sulfiding hydrocracking catalysts, this can be explained by assuming they come from hydrocracking feeds instead of decomposition of sulfiding agents.
-
There are several approaches that can be taken to minimize the impact of these mercaptans on fuel gas and sour water.
-
Reduce the rate that sulfiding chemicals are injected and sulfide one reactor at a time instead of multiple reactors at once. This will spread out the mercaptans in fuel gas over a longer time and reduce the peak impact. Unfortunately, this can extend the time to sulfide and get units up and running. Also, it won’t reduce the total amount of mercaptans sent to fuel gas, just the peak concentration. Plus, it will likely have minimal impact on mercaptans sent to wastewater treating.
-
Route the vents to fuel gas into the largest fuel gas system available. While this does not reduce the total SO2 in flue gas it will reduce the peak concentration.
-
Gas phase sulfide. This eliminates low pressure bleeds and may reduce the amount of mercaptans in contact with sour water. In a hydrocracker it also eliminates the risk of producing mercaptans from hydrocracking during sulfiding. However, it requires use of DMDS as TBPS cannot be used with gas phase sulfiding.
-
Use the highest purity make-up H2 available to delay the build-up of high concentrations of methane and heavier hydrocarbons in the recycle gas, this will minimize and possibly eliminate the need for a high-pressure gas bleed during the initial low temperature sulfiding. If a bleed is required, route the high-pressure bleed to another hydrotreater instead of to fuel gas. At normal operating temperatures, essentially all the mercaptans will be converted to H2S in hydrotreater reactors.
-
Use TBPS instead of DMDS. This has several advantages:
-
Since TBPS breaks down at lower temperatures than DMDS there may be less non-decomposed mercaptans at sulfiding temperatures.
-
Since byproducts are C4 mercaptans instead of C1 mercaptans they boil at higher temperatures and are less likely to be vented from either the high-pressure separator or from oil being circulated through low pressure equipment.
-
Using TBPS greatly reduces or eliminates the production of methyl mercaptan which is the only decomposition product with much water solubility, this should minimize mercaptans getting into the sour water treating plant.
-
Keep the Stripper and Charge Surge Drum as cold as possible to keep mercaptans in solution and recycle to the Reactor instead of venting. Also, keep stripping steam out of the Stripper. These steps also increase recycle of H2S to the reactor and reduce DMDS or TBPS injection requirements.
-
Route Stripper bottoms back to the Charge Surge Drum instead of to tankage to recycle mercaptans and H2S back to the Reactor. Mercaptans can be vented from tanks. If captured in a gas recovery system instead of going to atmosphere they will normally be routed to fuel gas.
-
Perform the low temperature sulfiding at a higher temperature than catalyst vendors recommend. Or if unwilling to do this, raise the first bed to around 460-500°F when the initial temperature wave reaches the second bed and use quench to keep the lower beds at recommended temperatures; this will increase mercaptan decomposition in the first bed after it has sulfur on it without the risk of reducing catalyst in the lower beds. Even if the sulfiding of the first bed is less effective this will often have minimal impact on the whole reactor especially if the top bed is used mostly for demetalization, olefin saturation and removal of the easiest sulfur species.
-
Caustic treats the vents to fuel gas to remove mercaptans.
-
Pre-sulfide the catalyst instead of sulfiding in-situ. This saves time during start-up and eliminates the need to deal with mercaptans. However, it is more expensive, requires obtaining the catalyst 1-2 months earlier to have time to pre-sulfide it and may mean inert entry is required in the reactor during catalyst loading.
The most significant steps that can be taken to reduce mercaptans getting into fuel gas will often be to either gas phase sulfide with DMDS and route high pressure bleeds to another hydrotreater or liquid phase sulfide with TBPS. Use of TBPS will likely be the most effective method of reducing mercaptans in sour water.
In the last several years Motiva has done a lot more presulfiding than in the past. Avoiding sulfur excursions in heater flue gas is one of the reasons we have been doing this.
SOREN MARKLUND (Chem32 LLC)
This may not directly address the issue at hand, but if wastewater mitigation is a serious issue, consider the use of pre-activated catalyst. In this case the hydroprocessing catalyst is delivered to the refinery already in its fully sulfided and activated state, meaning that activation inside the reactor will no longer be required. In this case, upon startup, there will be no water formation because of the sulfiding reaction. Since there will be no water formation, there will be no issues with contaminated wastewater, nor non-reacted mercaptan species. Starting up using pre-activated catalyst is comparably a very easy process, where the pre-activated catalyst is heated up under hydrogen/oil (or feed in gas phase if so required (i.e. Naphtha feed)). No more exotherms, no more requirements to hold at various plateaus, heating up rate only limited to the hydrogen embrittlement curve of said reactor. And, moreover, addressing this question, no foul-smelling water formation. CHEM32 located in Orange Texas can provide THIOCAT fully pre-activated hydroprocessing catalyst for your applications, and if cracked feed is present, THIOCAT CFT (cracked-feed tolerant) pre-activation can be provided to eliminate the 72h break in period under straight run feed, allowing starting up using cracked feed directly.