Question 15: ULSD reactor feed/effluent heat exchanger leaks can be a big problem meeting product specifications. What are best practices for detecting and preventing leaks? Are there new technologies or mechanical specifications to prevent cross contamination?
Michael Chuba (Sunoco)
With regard to feed/effluent exchanger leaks there are a number of actions that can be taken during the initial design phase of the unit. First, if feed/product exchangers are employed, the design should be such that the product side of the exchanger is higher pressure than the feed side. To accomplish this the exchanger would have to be located upstream of the unit’s high pressure charge pumps. If the unit has a feed surge drum this will require the drum to be designed for hot feed since it is recommended that the drum be located up-stream of the unit’s high pressure feed pumps in case of vaporization of the feed or water. It may also require relocating the product control valve downstream of this exchanger and designing the exchanger for a blocked-in pump discharge case. In any event the arrangement of having high pressure feed against low pressure product should be avoided.
As for the design of the feed/effluent exchangers where both sides are in the high-pressure loop, the driving force for leaks is much less and consists of just the reactor and exchanger delta P. When specifying the design of the tubes, they should be called out as being seal welded to the tube sheet. During turnarounds the tubes and seal welds should be inspected. Tube thickness can be checked using eddy current technique. Any tubes found thinning below acceptable levels should be plugged to ensure they don’t open up during the next cycle. In addition, seal weld integrity may be checked by performing a shell side hydrotest with the channel cover removed to look for wet seal welds. Liquid penetrant (PT) of seal welds is sometimes performed as well to look for seal weld cracks. Leaking seal welds are repaired by re-rolling, or by re-welding as a last resort.
As for identifying exchanger leaks, typical methods involve detecting the presence of a target molecule in the feed going into the exchanger and the product coming out of the exchanger. The target molecule can be an injected chemical, dye, or radioactive tracer or an indigenous molecular species that undergoes 100% conversion in the hydrotreater and can be easily detected.
As a first step we typically use sulfur speciation and track the easiest to convert sulfur species present in the greatest amount in the feed that gets completely converted at the operating conditions of the unit being run. The presence of this target molecule in the product from the exchanger (and its relative amount) would indicate a leak within the exchanger.
If a leak were indicated, our next step would be to identify the exact exchanger bundle/pass which is leaking. To date we have not had any leaks in any of our ULSD units.
Vern Mallett (UOP)
Hydroprocessing units employ a series of feed/effluent heat exchangers to recover heat from the reactor effluent and pre-heat the reactor feed. In these reactors, the reactor effluent is at lower pressure than the feed. As such, a tube leak will result in a partial bypass of feed material directly into the reactor effluent. When treating requirements are severe, small leaks will impact the product sulfur levels and potential adversely impact product yields and catalyst activity:
Methods that are currently used to determine if there is an exchanger leak.
1. Method A – Direct Sampling
2. Method B – Radioactive Tracers
3. Method C – Helium Tracers
4. Method D – Gasoline Dye Testing Method A – Direct Sampling
This method is based on measuring the sulfur content between the reactor outlet and the heat exchanger. If sulfur content upstream of the exchanger is higher than downstream, the most likely primary cause is a leaking exchanger. The sample line consists of small diameter, stainless tubing. During the sampling the operator should wear breathing apparatus because of H2S and hydrocarbon release. Samples should be taken at the following locations:
1. Between reactor outlet and first exchanger,
2. Directly after last exchanger, and
3. At the bottom of the stripper.
Method B – Radioactive Tracers.
Radioactive tracers can give excellent results in detecting leaking heat exchangers. The method is based on differences in residence time between feed passing and bypassing the reactor through the leaking exchanger. A disadvantage in using radioactive tracers is that it is done by specialized companies usually requiring permits. However, this method can give a reliable indication of a leak.
Method C – Helium Tracers
Similar to the radioactive tracer methods, helium is injected upstream of the suspect exchanger network. A helium detector is tied in downstream. Helium is spiked into the process. Based on time and concentration at the detector after the spike, the presence and magnitude of a leak is identified. The accuracy of this method has been consistently verified and is commercially available.
Method D- Gasoline Dye Testing
The gasoline dye test is effective on light-colored feeds such as naphtha, kerosene, or distillate. Sufficient dye is introduced into the feed such that enough dye passes through the leak to color the product. The dye is a nitrogen compound that will be rendered colorless when run through the catalyst bed. The reactor effluent is sampled before the suspect heat exchanger, if possible, and after the heat exchangers. If both samples are not colored by the dye, the heat exchanger is most likely tight. If the heat exchanger effluent is colored, the exchanger is leaking.
Dave DiCamillo (Criterion Catalysts & Technologies)
While there are several methods that can be used to detect feed/effluent heat exchanger leaks, sulfur speciation is the best method for detecting leaks in ULSD service. As the table below shows, only sulfur speciation has the precision to detect the potentially low levels of sulfur for suspected ULSD leaks. The basic approach is to use sulfur speciation to detect the most reactive sulfur species that normally would not be found in ULSD product.
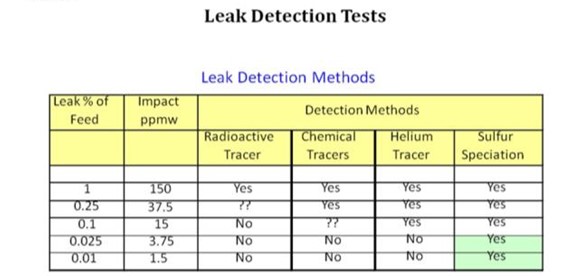
While waiting for these analytical results, a quick field test would be to increase reactor temperature and measure the product sulfur response, if any. For example, increasing reactor temperature 10°F should result in a product sulfur decrease in the range of 5 to 10 ppm sulfur under normal operation. No response to successive temperature changes could be an indication of processing problems like a heat exchanger leak.
Dave Ferguson (Tracero)
Online heat exchanger leak tests can be accomplished in a couple of different ways. One method involves the use of radioactive tracers. A very small volume of radiotracer is injected into the high-pressure side of the heat exchangers. Sensitive radiation detectors are placed on the low-pressure outlet of the exchangers. In an exchanger where a leak occurs the “leak” detector detects radiation on the low-pressure side, having leaked from the high-pressure side. This technique will find leaks greater than 0.5%. If samples can be collected, radioactive tracers can be used to find leaks as small as 100 ppm.
In many cases of ULSD exchangers very small leaks can cause a product to be off- specification. The leak size expected may be below the detection limits of the radiation detector. Tracerco has developed a family of chemical tracers which can be detected in hydrocarbon streams down to the ppb (part-per-billion) level. A small volume of chemical tracer is injected into the high-pressure stream to an exchanger. For this test the low-pressure side must be sampled. The samples are tested for the presence of the chemical compound and the exchanger was leaking if the test is positive. This technique can identify leaks as small as 10 ppm.
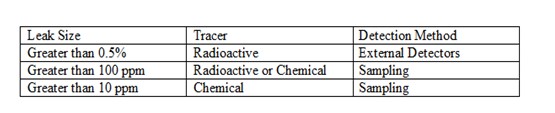
Meredith Lansdown (ART)
Even small leaks in the feed/effluent heat exchanger in ULSD units can cause problems with meeting product specifications and can shorten cycle lengths. Seal welding the exchanger tubes to the tube sheet in the design phase can help prevent leaks from developing in the first place. When the unit is online, several different methods exist for detecting leaks. Often times, the challenge lies not only in figuring out whether or not there is a leak, but actually locating it.
Sulfur speciation of feed and product is one of the more common methods for determining whether or not there is a leak. When carefully implemented, this method can be used to detect extremely small leaks in ULSD. Since the easily converted sulfur species are supposed to be removed in the hydrotreater, their presence in the product stream indicates that a leak in the feed line is allowing them to pass into the effluent. Sulfur speciation does not require sampling the reactor effluent or other samples points from which samples are not routinely taken; however, it also does not allow the refiner to pinpoint which exchanger is actually leaking.
Radioisotope tracers with external detectors mounted on the external lines of the exchangers can be used for feed leaks greater than 0.05-vol%. In this method, the isotope is injected upstream of the exchanger on the feed side, and the detectors measure the response time downstream. Having detectors on the effluent side of each exchanger is helpful in identifying which exchanger is leaking. Since sometimes a pickup of the tracer on the feed side of the exchanger can show up as a leak, in this method secondary leak detectors are often used as well. When using radioisotope tracers, it is important to ensure that the residence time is sufficient to notice the delay in picking up the signal. It is also important to sample the exchanger effluent lines in order to determine whether the leak is tracer pickup or an actual leak.
Feed leaks as low as 100-vol-ppm in the product can be detected using radioisotope tracers with effluent sampling instead of mounting external detectors. The tracer is injected into the feed inlet of one exchanger at a time and samples are obtained and analyzed onsite from the effluent side. The radiation counts from the exchanger effluents will indicate which exchanger is leaking.
Gas tracers, such as helium, are useful in determining whether or not there is a leak, but it may be difficult to quantify the leak size under 0.1-vol% because it may be difficult to obtain a representative sample.
TRACERCO has developed a group of chemical tracers that have even better limits than radioisotope tracers to find very small leaks, which do pose a threat to catalyst run lengthand product quality. These chemicals are selected to closely match process fluids. Since they are very stable, they flash in the presence of high temperatures in a hydrotreating reactor but then condense with the effluent without actually reacting themselves. They can be detected in the product at levels as low as 1-ppm, so theoretically, a leak as low as 1-ppm can be detected using this method. In using these chemicals as tracers, though, the samples must be sent to a laboratory for analysis. Also, this method does not indicate which exchanger is leaking