Question 14: For units that feed hydrocracked naphtha directly to the reforming unit, what is the typical concentration of sulfur in the feed? How does the concentration change over the hydrocracker catalyst cycle, and what are the impacts to the operation of the reformer?
SABITOV (Phillips 66)
Many of P66 sites are feeding hydrocracker naphtha to reformers. I have two case studies to provide details.
In the first case, we have Cyclic Reformer A where we are processing about 10% of deisohexanized (DIH) light hydrocracker naphtha directly from hydrocracker without treating in the sulfur guard bed. Sulfur in DIH bottoms varies from about 6 ppm at hydrocracker SOR (start-of-run) to about 12 ppm at hydrocracker EOR (end-of-run). As this stream is blended with hydrotreated naphtha, reformer is only seeing about 1 to 1.5 wt ppm S (sulfur) in the feed. We can send little slipstream of DIH bottoms upstream of the hydrotreater if S in reformer becomes excessive. In general, we estimate 0.5 vol% (volume percent) C5+ yield debit in the reformer per each ppm S increase in reformer feed. To minimize reformer yield loss and potentially free up some HTU capacity, we are evaluating the installation of a sulfur guard bed on the DIH bottoms stream.
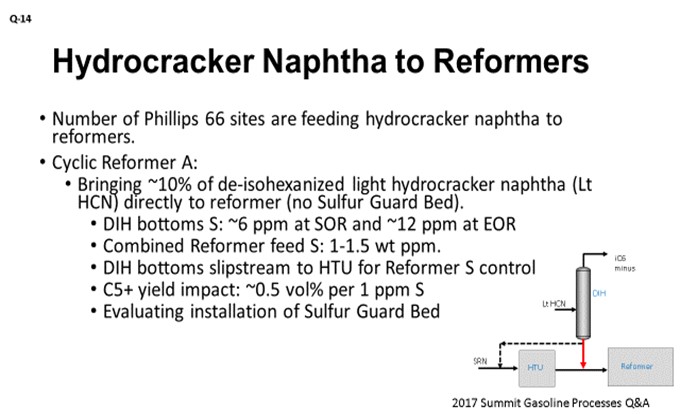
In the second case study, we have Semi-regen Reformer B running on 100% dehexanized hydrocracker naphtha. In this case, hydrocracker naphtha is treated by the sulfur guard bed to S levels less than 0.1 ppmw. We are getting very good performance from this reformer.
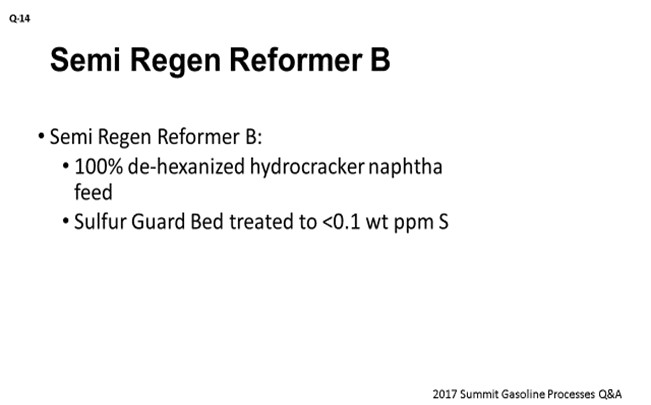
KOLAPO ALADE-LAMBO (Honeywell UOP)
At start-of-run conditions in a hydrocracking unit, the sulfur in hydrocracked naphtha can be between 2 and 5 ppmw. At end-of-run conditions, the sulfur can be between 10 and 20 ppmw. As high 40 ppmw has been observed at end-of-run conditions for one customer. If the hydrocracked naphtha is processed through the hydrotreating unit before the Honeywell UOP Platforming™ unit, the operation of the platforming unit will not be impacted. If it is not processed through the hydrotreating unit and is fed directly to the platforming unit, the amount that can be processed will depend on how much sulfur is in the hydrocracked naphtha and how much treated naphtha is being combined with it to dilute the sulfur content. Keep in mind that there are other factors, such as other contaminants and intermediate storage for the hydrocracked naphtha.
If the hydrocracked naphtha is being fed to the reforming unit undiluted and not processed through a hydrotreating unit, then there would have to be a sulfur guard bed installed upstream of the reforming unit to remove the sulfur down to tolerable levels. The consideration for a sulfur guard bed can also be made if the hydrocracked naphtha will be diluted.
RICHARD TODD (Norton Engineering Consultants, Inc.)
Sulfur in hydrocrackate used as reformer feed can increase from undetectable to 2 to 3 ppm at the end of the hydrocracker cycle, when temperatures are high enough to cause mercaptan formation in the hydrocrackate boiling range. Impacts on reforming catalyst include some deactivation and the potential to form sulfates on the catalyst during regeneration.