Question 13: What equipment size limitations set the maximum capacity for a single-train, high pressure, heavy feed hydro-conversion unit (HCU ebullated-bed resid)? What are the other considerations?
LEICHTY (Chevron USA, Inc.)
The answer to this question primarily centers around the type of reactor, but there are some additional considerations.
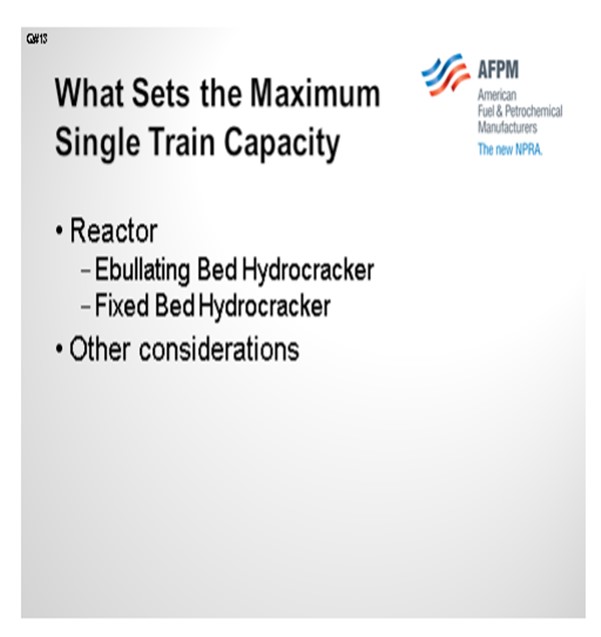
With an ebullating-bed reactor, the primary throughput limit is set by the superficial velocity, which is a function of reactor diameter and throughput. The superficial velocity is what determines the ability to separate gas from liquid going to the recycle pump. The largest diameter reactor in service today is 13.5 feet ID (inside diameter), which allows for a feed rate of 47 kbpd (thousand barrels per pound) to 50 kbpd. It is now possible to build a 15-foot inner diameter that would allow the feed rate to increase between 65,000 bpd and 85,000 bpd, depending on the conversion level desired.
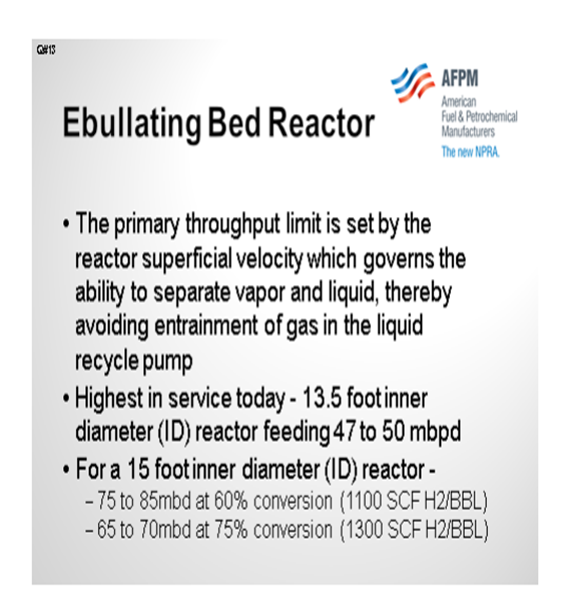
With a fixed-bed reactor, the throughput limit is set by the desired reactor flux which, again, is a function of reactor diameter and throughput. The next step is to calculate pressure drop across the reactor and each piece of equipment to ensure a good design. It is also important to consider the ability to distribute the reactants in a very wide bed and to uniformly mix quench hydrogen for temperature control. The ASME 2000 code does provide for higher allowable stress, which makes larger reactor diameters possible. With that change in code and CLG’s latest ISOMIX internals, a 70,000-bpd hydrocracker or 85,000 bpd hydrotreater can be designed in a single-train unit.
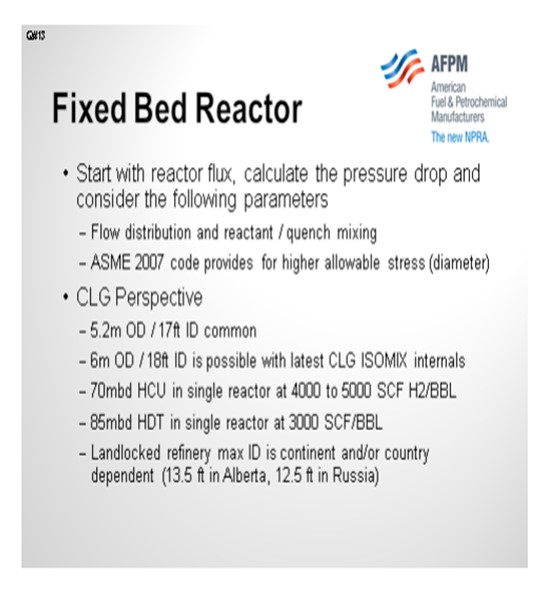
The reactor diameter and throughputs discussed thus far assume that there are no other limitations or restrictions. There are other considerations that could reduce the single-train capacity. For instance, if a refinery is landlocked, there may be diameter and/or weight limitations set by roads, port infrastructure, or bridges. Additionally, not every manufacturing shop is capable of fabricating to the maximum diameter. There may also be some site-specific erection limitations.
Aside from the reactor, there are other practical limits that may prevent reaching the aforementioned throughputs. Pressure drop through the high pressure loop can increase to the point where a recycle compressor cannot deliver the desired capacity. If that is the case, care must be taken during the design due to the fact that heat exchanger tube bundle diameters max out at 60 inches and that the maximum furnace tube diameter is about 10 inches as a result of heat flux. CLG prefers to design with two-pass furnaces, but four-pass has been done and would allow a reduction in pressure drop. High-pressure loop-piping diameter limitations can also become a significant source of loop pressure drop.
Finally, it is important to think about the desired cycle length, onstream factor, and future debottlenecking capability. With a single-train design, there is no ability to take down one module at a time for a catalyst change while increasing rate on the sister module. It may also be harder to manage oil movements during catalyst changes with a single-train than with a dualtrain design. If future debottlenecking is anticipated, then it might be easier to go with multiple modules rather than a single reactor given that a single-train design may be stretched closer to all of the aforementioned limits.
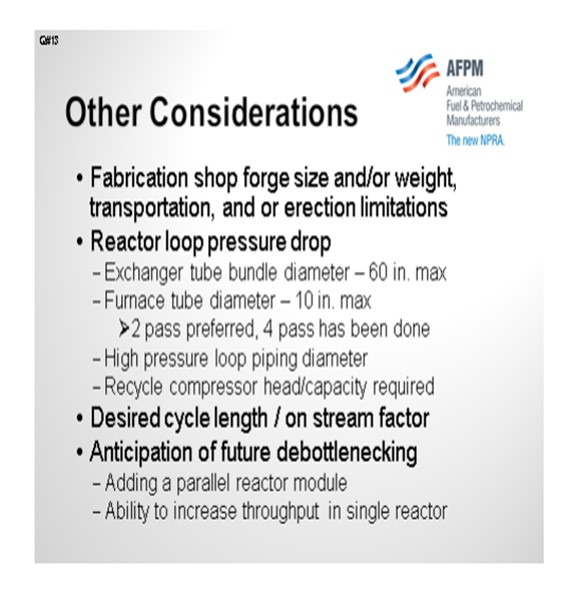
OHMES (KBC Advanced Technologies, Inc.)
I want to add a couple points to what Steve said. In the mid-2000s when everyone was trying to build all of these new units, it was not just the reactors that were causing problems for the CHPSs (cold high-pressure separators). Often, you could not find the pumps and compressors of a desired size to put into these units, which would somewhat dictate whether you did multiple-train units or went one of two or two of three in your makeup compressors.
We primarily focus on ensuring that our clients understand what will happen during a future shutdown; because early in the FEL (front-end loading) process, someone wants to minimize capital. So yes, that may be the right decision, but you will need to put in a kit that will function in the refinery. So, if that unit is down and you have all your eggs in that basket, then what will happen to that feed? Do you have to shut down the whole plant? Do you have to change your crude slate or whatever it might be? Do you have the ability to sell that feed, or are you landlocked and cannot do so? Are you going to be able to meet product specs? In our cases, we are often able to justify two smaller parallel trains in order to keep one online to sustain the entire facility operational. I will not go through these in a lot of detail because there is more in the Answer Book.
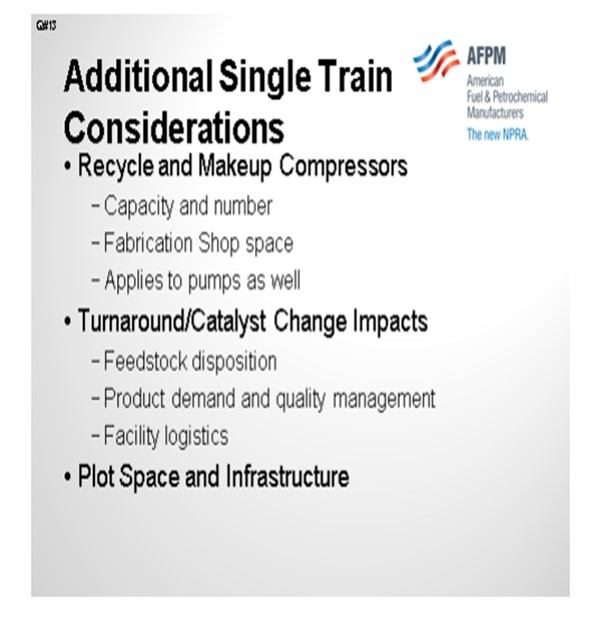
We have worked with a few clients to do some Monte Carlo scenario analysis to help them understand the implications of one versus two trains. Also, the ebullated bed units typically, unfortunately, have a slightly lower on-steam factor than do some of the conventional hydrotreating technologies. So, you need to understand the implications to the plant and what the units can achieve. You also need to get down to the equipment level to really understand that if you recycle or makeup compressors are going to be more problematic, then you will want to focus more attention in those areas during the design phase. In summary, you want to balance not only the capital needs, but also the overall operating constraints to the facility so that when you do start-up and run this, you will be able to achieve the targets you wanted.
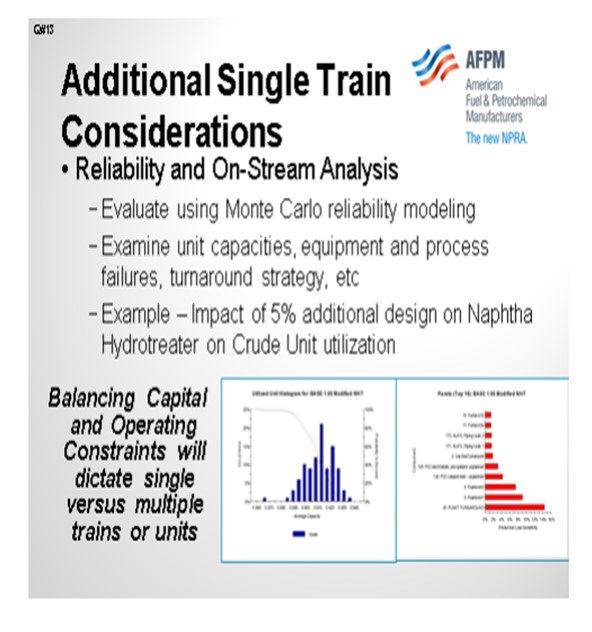
BODOLUS (CVR Energy)
We have already licensed a unit of 70,000 bpd unit, single-train, and fixed-bed reactors. It will have a single makeup gas compressor because it has a centralized hydrogen compression system. So that is not considered a bottleneck. What I do understand is that the constraint to limit the feed to 70,000 barrels was max flux rate. I am not able to understand how this it is related to the superficial velocity; so, if you have any answers to that situation, please respond.
OHMES (KBC Advanced Technologies, Inc.)
We agree with Steve’s points. I know there are some in Asia that are in the 70,000 bpd to 75,000 bpd range. So it is possible.
SUBHASH SINGHAL (Kuwait National Petroleum Company)
Reactors’ size and weight may limit the capacity of a single-train reactor within maximum mass flux constraints.
OHMES, DAVID WILLIAMS, and MIKE VOIGT (KBC Advanced Technologies, Inc.)
We agree with the stated size limitations and considerations made by the other panelists. However, several other aspects outside of reactor design come into the decision-making process. For instance, the ability to secure pumps and compressors (recycle and makeup) becomes a more difficult challenge as the unit’s size increases. Though the normal convention is to have a single recycle compressor with two makeup compressors with some multiple of expected capacity, large units may need to consider more makeup compressors at lower capacity per machine to be able to have the machines constructed in the time required for the project. Similarly, large multi-stage pumps can be difficult to secure during busy construction periods.
In the early stages of the front-end loading (FEL) process, capital is a major constraint and consideration. Therefore, most refiners strive for the configuration and unit size that minimizes capital outlay. However, as the project progresses through the FEL process, the practical operation of the unit and facility comes into play. Therefore, KBC normally stresses to clients that the impact of single versus multiple units/trains should be included early the FEL process, particularly on how the facility will operate during catalyst changeouts and turnarounds. For instance, if the hydrocracker will have a catalyst changeout every two years and full turnaround every four years, where will the hydrocracker feed go for that 15- to 45-day period each time? Will the feedstock be sold, stored in tankage for later processing, or will facility throughput have to be cut back or even severely curtailed? Depending on the facility location and market conditions, the lost opportunity cost for these situations may drive the refiner to consider two trains or two units to mitigate the lost revenue. In addition, how will the loss of the unit’s product affect product blending? For instance, can the facility still produce jet and diesel products without the high-quality hydrocracker streams? An analysis of additional capital versus lost opportunity savings should be completed early in the process and communicated to the respective licensors.
Equipment and unit reliability have a similar impact on this decision. Therefore, the effective onstream factor should be generated to determine how the overall facility will operate when respective equipment is down for regular and unanticipated maintenance. For instance, ebullated bed hydrocrackers have significantly improved in onstream factor in recent years. However, by comparison to most modern refining technologies, those units struggle to consistently achieve greater than 90% onstream factor. Therefore, for roughly one month per year, the ebullated bed unit will be out of service. This outage will have a significant impact on the overall facility and may drive the decision to reduce the size of the ebullated bed unit. The ebullating-bed process requires evaluation and selection of the optimal downstream processing scheme to maximize yield and product quality at the minimum investment cost. The investment ultimately will depend on the capacity and utilization of the ebullating-bed unit in conjunction with the capacity and utilization of the existing units to process the products and residual oil from the ebullating-bed unit. Options for the residual oil include for example: coking and gasification. Typically, additional hydrotreating of the ebullating-bed products is required for both sulfur and hydrogen content. The optimal design for the complex system can be determined with the application of reliability modeling using the Monte Carlo method.
As an example, KBC completed a detailed system analysis as part of a major capital expansion project for a complex refinery. Through stochastic reliability modeling, multiple scenarios were evaluated based on various system configurations, unit process technologies, unit sizing and turn-up capacities, equipment and process failures, and turnaround strategies, to determine the optimal process design.
From the system analysis, individual unit performance, overall system performance, and sensitivities for each scenario were appraised. To illustrate this approach simplistically, a naphtha hydrotreater (NHT) is examined. This particular scenario has a modified NHT unit with turn-up capacity to 105% of design. The following graph represents the crude unit utilized production capacity over a mission time of 10 years for this scenario. The two major interruptions are the result of a plant-wide shutdown on a four-year cycle. In this scenario, the average utilized capacity for the crude unit is 91.4%.
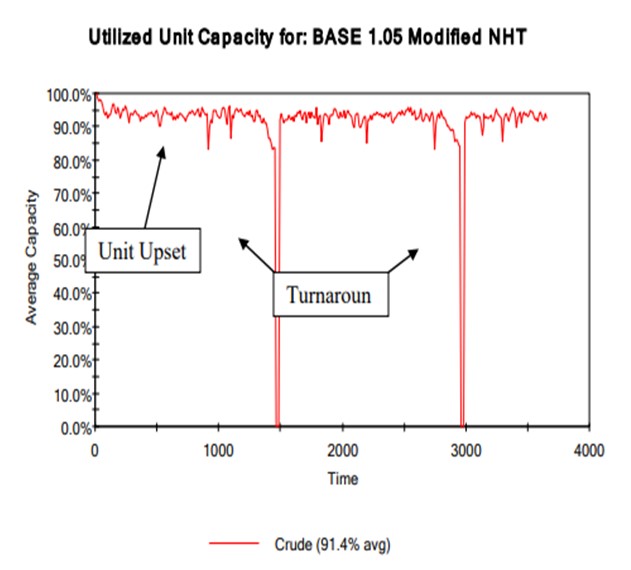
The production distribution over this same 10-year mission time is presented in the following graph. The crude production utilization distribution indicates that the performance of the crude unit is between 89% and 93% with a 50% probability of exceeding 91% of design capacity.
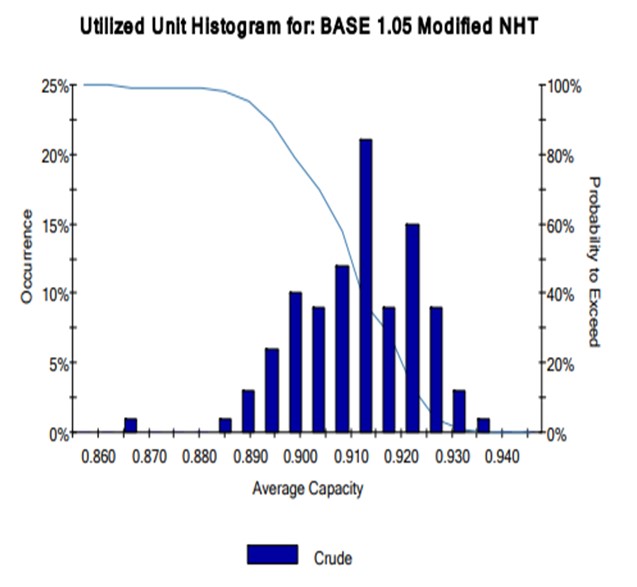
For this example, the top ten major events that contributed to production loss for this complex refinery are represented in the graph for Production Loss Sensitivity. The plant-wide turnaround (TAR) is the major contributor to production loss accounting for 14.2% of the total losses. TAR strategies and alternatives for sequencing can then be evaluated to reduce this sensitivity and quantify overall system performance improvements. Other high probability production loss scenarios can be reviewed in a similar fashion to determine how design or configuration changes will impact overall availability and onstream factor.
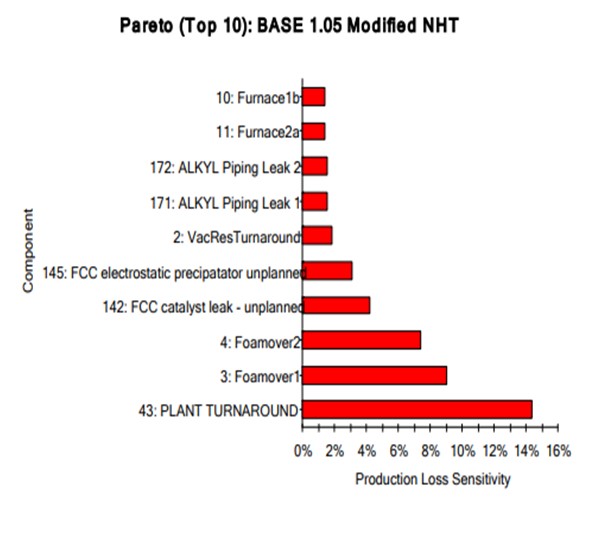
Finally, facility plot space and infrastructure have an impact on unit sizing. Though the facility may want a large single-train unit, the plot space may not be available for the unit and the associated support units (hydrogen plant, utilities, etc.). Emergency flare size can also impact this decision, as larger units require larger flare systems. Based on the relief scenario analysis and reliability analysis, the size of the flare lines and flare itself may make a large unit difficult to build.
Therefore, in addition to examining the issues associated with designing and constructing the reactors for large single-train units, the refiner should also consider the implications of unit size on pump and compressor sizing and construction, managing planned and unplanned outages, equipment reliability, and overall facility plot space and infrastructure needs. Ultimately, the refiner should strike the right balance between capital outlay and operating costs and constraints