Question 13: In chlorided isomerization units, what procedures are you using to shut down caustic-free and make the net gas scrubber safe for maintenance?
SABITOV (Phillips 66)
After initial purging with N2, the following considerations would apply. The caustic scrubber vessel and the majority of piping are both typically constructed of killed carbon steel and have post-weld heat-treatment requirements as the whole section operates in 2 to 15 wt.% (weight percent) caustic environment. There might be a risk of caustic embrittlement at elevated temperatures. This embrittlement would potentially also be applicable to sections where – over the years of service and maintenance compliance with all aspects of post-weld heat-treatment – [Best Practices?] may not have been consistently followed. To minimize those risks, we are recommending following maximum temperature limits set by the caustic service graph included in API RP 571 to ensure that the scrubber section will become caustic-free. Therefore, our sites would typically use warm fire water or industrial water to flush and clean the scrubber section before opening it up for maintenance with a water temperature limit of about 170°F. Some of our sites would opt to continue using a cleaning scrubber with low-pressure steam upon verification of caustic removal.
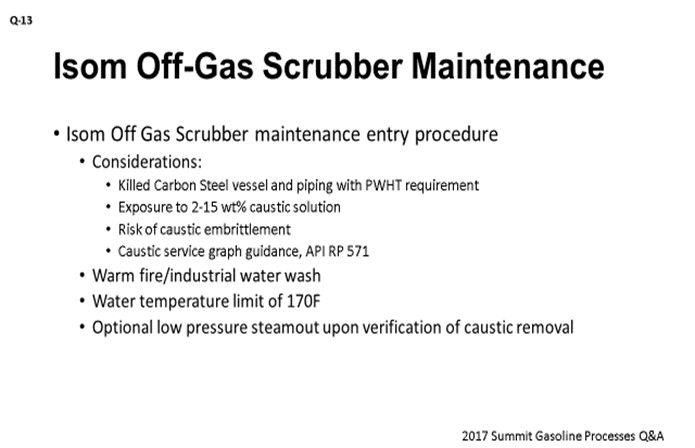
HEIDI FRASER (Honeywell UOP)
The following steps are necessary to shut down – caustic-free – and make the Honeywell UOP Penex™ or Butamer™ net gas scrubber safe for maintenance:
-
Follow the normal shutdown procedures in the UOP General Operating Manual to shut down the reactor section, bypassing feed around the reactors, and cooling the catalyst by sweeping it with hydrogen. Once the catalyst has cooled, hydrogen flow can be stopped.
-
Shut down the stabilizer (if desired), then block in the off-gas line to the net gas scrubber before depressuring the stabilizer.
-
Depressure the scrubber to flare, then purge with nitrogen to remove hydrogen from the vessel.
-
Pump and/or drain the caustic from the scrubber. Maintain pressure on the vessel as the caustic level drops by adding nitrogen as needed.
-
Upon removal of caustic from the scrubber, the vessel can be water-filled and/or water-washed to completely remove residual caustic from the vessel. Circulate water through the caustic circulation lines to ensure complete removal of caustic. UOP recommends the use of cold, clean condensate for the wash water. Drain the water and repeat as needed until the water is a neutral pH.
Note: Some refiners want to steam out the scrubber to confirm that all caustic has been removed. This step is not necessary if the scrubber has been water-washed since caustic is soluble in water and there is no heavy hydrocarbon present in this vessel. In addition, UOP typically does not design the scrubber for steam-out conditions due to concerns with caustic embrittlement. If it is not designed for steam-out, steaming the scrubber with caustic in the system will lead to embrittlement of the carbon steel vessel. However, some refiners have designed their scrubber to be post-weld heat-treated (PWHT) so that it can be steamed. Please confirm your scrubber design conditions before attempting to steam out.
-
Prepare the net gas scrubber for entry by blinding off all process lines to the vessel and then purging with air, followed by a check by the Refinery Safety Department.