Question 12: Now that ULSD production has seen several cycles, what are the SOR and EOR operating conditions? What catalyst formulations are you using (NiMo, CoMo, regen, various blends)?
Brian Moyse (Haldor Topsoe)
The operating conditions for ULSD vary and will depend on the feed to be processed as well as specific requirements to the product quality. This is apart from the typical US and European standards for ULSD, such as low aromatics, color, cold flow properties or other additional specifications.
Topsoe has been involved in the design and/or revamp of more than 80 ULSD units, plus our catalysts are the most widely used in ULSD service worldwide. In the study phase for a grassroots unit one of the first decisions we make is the choice of operating pressure. Once the pressure is fixed, all other operating parameters (LHSV, H2/oil, reactor temperatures) including catalyst are chosen. All of the process parameters inter- correlate and the final solution should also be able to function with up-stream and down- stream equipment. If an existing unit is revamped into ULSD the refiner may want to use as much of the existing hardware as possible to reduce CAPEX. In this case the unit pressure is fixed.
In case of a simple catalyst replacement in an existing unit, the catalyst system is optimized to provide the client with highest NPV over the lifetime of the catalyst. The prime objective is to meet the product specifications for fixed cycle length, and once this is met, we look into factors that will reduce cost. Low H2 consumption, low operating temperature, high diesel yield, use of second generation ULSD catalysts, regenerated catalysts, etc are some of the secondary objectives that will reduce the cost. In a time when the refinery margins are low, many ULSD hydrotreaters are using from 30 to 100% regenerated or reactivated (ReFRESH TM) catalysts at the cost of cycle length or feed capacity. With the current lower demand on the ULSD supply this is an acceptable solution.
Below we will present some very general operating conditions and catalyst solutions for three ranges of the operating pressure:
· Low H2 pressure: < 600 psi
· Medium H2 pressure. 600 to 950 psi
· High H2 pressure: > 950 psi
Low H2 pressure: < 600 psi
At low pressure it will often not be possible to remove the basic nitrogen compounds that inhibit desulphurization via the hydrogenation route, and as a consequence a CoMo catalyst is preferred. It is possible to co-process some cracked feed, but since the reactions are slow the LHSV will have to be reduced. The hydrogen consumption will be modest compared to operation at higher pressure due to less aromatic saturation, and the
unit can therefore operate with a low H2/oil ratio. Topsoe’s industry leading CoMo BRIM™ catalysts are installed in units that operate at an H2/oil ratio as low as 250 SCF/bbl at a reactor outlet hydrogen pressure of less than 150 psi. With such low hydrogen availability and pressure, a CoMo catalyst with a high activity for the direct desulphurization route is required, and use of NiMo will only lead to both poor start-of- run activity and high deactivation rate. The temperature during the cycle is ranging from 610 to 740°F, but we have experience with units that start at 715°F and reach end of the cycle at 770°F. The LHSV can be anywhere between 0.5 to 5 hr-1.
Medium H2 pressure: 650 – 950 psi
Operating at medium pressure is not well defined. If the inhibiting N species in the feed are removed the fast hydrogenation route can be used with NiMo preferred and if they cannot, the slower direct route will predominate and CoMo is selected. Since cracked feedstock’s have a high N content, the ratio of these in the feed blend will in essence be dictating the choice of NiMo or CoMo. If the hydrogenation route can be used but the H2 availability is too low to cover the consumption, it is possible to load some CoMo together with the NiMo, but this will reduce cycle length.
This is illustrated in Figure, 1 based upon testing of 100% CoMo, 100% NiMo and three stacked bed configurations of CoMo/NiMo at 640 psi H2 on a feed containing 70 wtppm
N. In this test all N is removed and the 100% NiMo loading, which has the highest hydrogenation activity, also shows the highest HDS activity and the highest H2 consumption. The lowest activity is obtained with 100% CoMo, but this system also consumes less H2 than any other loading. The three stacked bed solutions are in between these two extremes, both in terms of HDS activity and H2 consumption. It is therefore possible to balance activity and H2 consumption as needed for a specific unit.
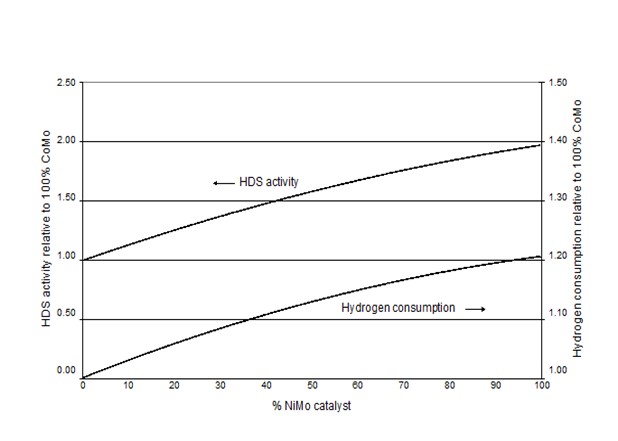
Figure 1: Pilot plant testing of 100% CoMo, 100% NiMo and three combinations of CoMo/NiMo at 640 psi H2.
From the above it is obvious that the required H2/oil ratio is highest when using NiMo and lowest with CoMo.
The EOR temperature is generally lower when a NiMo catalyst is used compared to a CoMo solution. This is because the N cannot be removed due to equilibrium constraints at high temperatures, and with higher contents of organic N in the oil the hydrogenation route cannot be used. Since the NiMo has a low activity for the direct desulphurization route it is not recommended to operate at these conditions. In some Asian countries there are specifications on product color, which also deteriorates with temperature. Some of the units Topsoe have designed for this part of the world are equipped with our color removal technology (polyshift) downstream the HDS section in order to operate the HDS catalyst at a higher EOR temperature.
High H2 pressure: > 950 psi
In high pressure operation a NiMo is in general the preferred choice due to its high hydrogenation activity. Despite the favorable pressure the LHSV is still in the same range, but as the aromatic saturation increases with pressure these units need to have a high H2/oil ratio, sometimes higher than 6,000 SCF/bbl. High pressure units are used when very difficult feedstocks are treated, e.g.,
crudes of South American origin or any feedstock containing more than 50% cracked LCO.
Michael Chuba (Sunoco)
Sunoco has multiple hydrotreating units including one hydrocracker that produce ULSD. These units' range in operating pressures from 475 to 1450 psig with EOR temperatures ranging from 670-770F, depending on pressure, feed, heater RACT limitations, and/or metallurgical temperature limitations.
The majority of our ULSD units use high efficiency CoMo catalyst. Now that we are into our second and third loads, we have begun using a combination of regenerated and fresh catalyst loads. Initially we had limited the use of regenerated catalyst to the top beds or in applications where the service was not as severe. With experience, we have found good activity with the regenerated material and have pushed more and more regenerated material into the mix with as much as 100% regenerated catalyst in some of reloads.
As for how many times ULSD catalyst can be regenerated, this depends on the condition of the catalyst. The main limitation to multiple catalyst regenerations is catalyst L/D. In applications employing vacuum catalyst unloading the abrasive handling of the catalyst can result in particle L/D of less than 2. Below this range we would typically not reuse this material. Other criteria for not reusing catalyst are high metals and other contaminate levels. Overall, multiple regeneration of ULSD catalyst can be done.
Charles Olsen (ART)
The types of catalysts being used in ULSD are typically current generation, high activity Type II catalysts, and the catalyst loadings cover the range from 100% CoMo catalysts for lower pressure units to 100% NiMo catalysts for higher pressure units with no H2 constraints. A large percentage of units have been using a combination of NiMo and CoMo catalysts as in the SmART Catalyst System® from Advanced Refining Technologies. The SmART system is based on a staged catalyst approach utilizing a high activity CoMo catalyst like 420DX for efficient removal of sulfur via the direct abstraction route and a high activity NiMo catalyst like NDXi which effectively removes the multisubstituted dibenzothiophenes via the hydrogenation route.
One of the big advantages of using a staged catalyst approach like this is illustrated in the figure below. The figure shows that as NiMo catalyst is added to the catalyst system there is a large increase in HDS activity relative to all CoMo reference, and eventually, a maximum in HDS activity is reached.
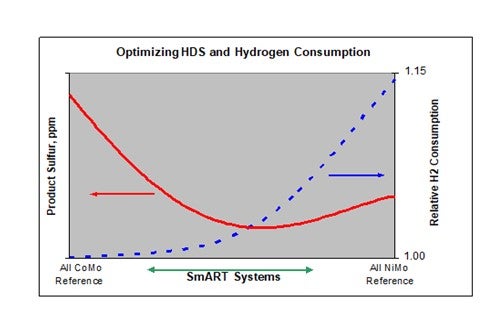
The position and magnitude of this optimum varies with feed and operating conditions, especially H2 partial pressure. The figure also includes the relative H2 consumption, and again, as the percentage of the NiMo component increases, the H2 consumption relative to the base CoMo system increases. Notice, however, that in this case the relationship between H2 consumption and the fraction of NiMo catalyst is nonlinear. In the region where the system shows the highest activity the hydrogen consumption is only slightly greater than that for the all CoMo system, and well below that for the all NiMo catalyst. It is this ability to balance HDS activity and H2 consumption to meet individual refiner requirements that sets SmART apart.
Exact start of run conditions will of course vary with feed and operating conditions, but a typical SOR WABT is around 640-660°F. The typical ULSD unit has a LHSV around 1 hr-1 with an inlet pressure of around 850 Psig, although ULSD unit pressures vary from a low of around 500 Psig to a high around 2000 Psig. Observed deactivation rates have been in the range of 1-3°F/mo depending upon the feed and operating conditions.
End of run conditions have been determined by a unit constraint such as a reactor inlet temperature limitation or some product attribute, most commonly product color. We’ve observed, as an average, an EOR WABT around 730-740°F. It’s important to note that for diesel product color it is the reactor outlet that is important. We’ve observed reactor outlets as high as 760°F in some cases with no detrimental impact on product color.
There are also a number of ULSD units which suffer from Silicon and Arsenic poisoning. These units tend to have shorter run lengths and will include a sizeable bed of guard catalyst to protect the active catalyst below.
Perhaps somewhat surprising is the number of ULSD units which have exceeded expectations in terms of cycle length. Many grassroots and revamped units were designed for 2 year cycles and actually ran 3-4 years. For the units which have changed out we’ve seen catalyst loadings which include adjustments to the relative amounts ofNiMo and CoMo catalysts, the addition of new, higher activity catalysts which weren’t available when the unit started up, and in some cases a portion of catalyst load is made up of reactivated catalysts. These reactivated catalysts are regenerated and further processed to redisperse the active metals using proprietary processes such as PHOENIX™ which was developed by ART and is now currently offered by TRICAT. In most of the latter cases reactivated catalyst makes up only part of the reactor fill with the remaining volume new catalyst.
Dave DiCamillo (Criterion Catalysts & Technologies)
Actually, some ULSD units containing Criterion catalysts are still on their first cycle, some due to use of 2nd generation ULSD catalysts in units designed on 1st generation products or operating with a significantly easier feed than assumed in the design basis. Each ULSD operation is unique, so there is not a single answer to the first part of this question (See also response for Question 22).
· SOR operating conditions are dependent on the unit design and feed quality. We have observed SOR temperatures ranging from 600 to 700°F. Obviously the more robust the unit design, the lower SOR temperature is likely to be.
· EOR operating conditions are dependent on refinery objectives for things like fixed or flexible turnaround/catalyst changeout date. With a flexible EOR date, the refiner can run the normal ULSD feed until the run becomes limited by reaching charge heater or catalyst activity limits. In many units, aromatic saturation thermodynamic equilibrium still limits the ability to make sulfur or color specs at EOR, however the maximum temperatures achievable are higher than originally anticipated, particularly in units processing only straight run feeds. Maximum reactor outlet temperatures remain a strong function of feedstock type, operating pressure (H2 partial pressure), catalyst type and LHSV.
There is also no single answer to the second part of this question - catalyst selection. Catalyst selection can depend on many factors such as:
· Unit design
· Feed quality
· Product quality requirements
· Hydrogen consumption and availability
· Cycle length targets
· Cost
· Refinery philosophy on catalyst type, e.g., fresh only, internal reuse, resale catalyst, etc.
Discussion of next cycle expectations with your catalyst supplier will help to formulate objectives, especially if they differ from the current operation. The best approach is to be clear on processing objectives (minimum requirements and desired targets) and prioritize them in the catalyst RFQ (request for quotation) so that vendors can provide some options to consider. A catalyst supplier will typically have a portfolio of products that can be customized for different operating modes such as maximum cycle length, maximum feed rate, minimum hydrogen consumption, etc.