Question 12: Discuss impacts of hydrotreating operations required to meet Tier III regulations. Highlight the benefits and concerns of pretreat versus post treat operations including; impacts on cycle length, FCC yields, octane from post treating options, and gasoline blending.
JEFF CATON (Axens)
Regulatory specifications for the gasoline and diesel pool, which are constantly evolving, have been in the forefront of refiners’ challenges in the last 15 plus years. In particular, the gasoline sulfur regulations have been a main driver for the remodeling of many refineries’ configurations. Specifically, in the US, most refiners have already addressed, or are continuing to address, the challenges to meet the US Tier 3 ultra-low sulfur gasoline (ULSG) <10 ppmw sulfur specification, which became effective on January 1, 2017. Most US refineries now have FCC pretreatment (CFHT) and/or FCC post-treatment unit(s) to ensure compliance with Tier 3 requirements (or Tier 2 requirements for refineries with waivers).
When the US Tier 2 gasoline regulations were initially proposed in the late 1990s and subsequently implemented in the 2000s, many refiners were convinced that CFHT would be the solution of choice. In addition to producing LSG/ULSG and improving FCC performance, additional benefits of volume swell through aromatics saturation and a reduction of FCC SOx and NOx emissions could be realized. A major benefit to producing LSG/ULSG with CFHT alone, with no post-treatment, is the retention of olefins in the FCC gasoline, thus benefiting the overall refinery pool octane balance.
Within the context of producing ULSG, the primary role of CFHT is that of desulfurization and the impact on the FCC gasoline produced. If one were to target a ULSG pool sulfur level of 10 ppm, the CFHT must reduce the FCC feed sulfur to about 200-300 ppm, considering a typical ratio of between 20:1 and 30:1 of the hydrotreated FCC feed sulfur to the FCC gasoline sulfur. When looking at the sulfur in FCC gasoline, the gasoline cut point and the distillation tail on the produced gasoline product is of high importance. In the US market, gasoline has been traditionally over-cut relative to the standard 430°F (220°C) cut-point and often extended to 450-480°F (230-250°C), thereby including not only benzothiophene but also some methyl-benzothiophenes in the gasoline (Refer to Figure 1 - FCC Gasoline Sulfur Profile). By over-cutting, these more difficult sulfur compounds, which will remain at a significant level following CFHT, will subsequently find their way into the FCC gasoline and make it difficult to produce ULSG. Undercutting the gasoline to less than 430°F will significantly help control the sulfur level when producing ULSG.
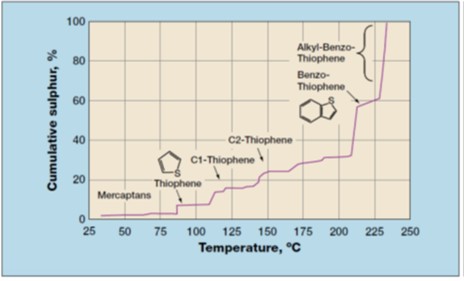
Considering the dependence of FCC gasoline on both CFHT performance and the need for precise fractionation of the FCC gasoline product, meeting ULSG targets through CFHT alone is possible, but challenging. There is little room for error or deterioration in CFHT performance over the course of a production run or cycle. Further, there can be limited flexibility in crude slate, thus reducing the refiner’s ability to process opportunistic crudes. These deterrents along with the relatively high capital cost for CFHT coupled with low refinery margins have resulted in the wide application of FCC post-treatment to reduce FCC gasoline sulfur. In fact, many refiners with CFHT have found it necessary and/or economically advantageous to also have a post-treatment unit.
Most refiners have already invested in an FCC post-treatment unit. For a refinery with relatively high sulfur FCC gasoline, the post-treatment severity will be higher in order to produce ULSG (Refer to Figure 2 - Prime-G+TM Designs at 10ppm Product Sulfur). This higher severity can lead to an unwanted high-octane loss through the undesirable saturation of olefins in the post-treatment unit. However, depending on process technology and process flow scheme selected for the post-treatment unit, the concern over octane loss can be managed. Axens Prime-G+ process technology has been applied extensively with varying flow schemes (with corresponding varying capital cost investment) to produce USLG with an octane loss that is within the constraints of the refiner’s pool octane balance (Refer to Figure 3 - Prime-G+™ Tailored Scheme). In short, a simplified process flow scheme with a single reactor combining selective hydrogenation (SHU) and hydrodesulfurization (HDS) can be utilized when FCC gasoline sulfur is relatively low while yielding a very low octane loss. Conversely, a more complex process flow scheme with a SHU reactor, splitter, and HDS reactor can be utilized to treat a higher sulfur FCC gasoline while still minimizing octane loss to within the constraints of the refiner’s pool octane balance.
Figure 2 - Prime-G+TM Designs at 10ppm Product Sulfur
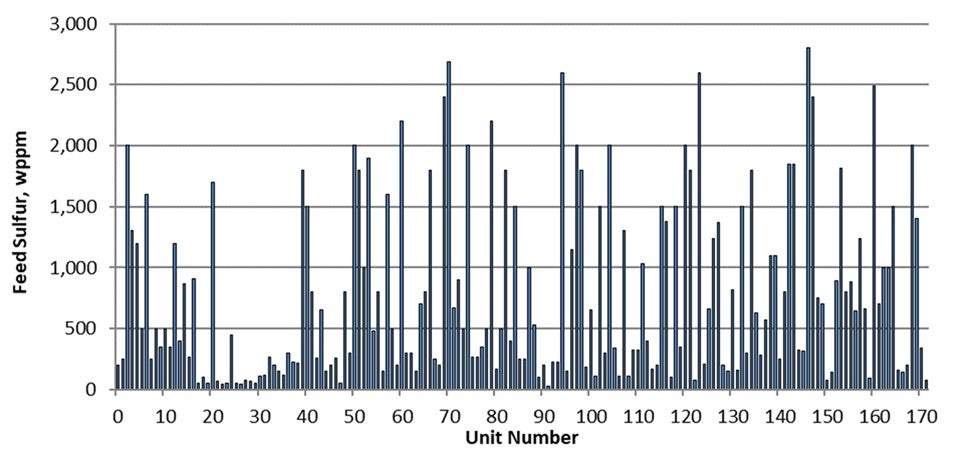
Figure 3 - Prime-G+™ Tailored Schemes
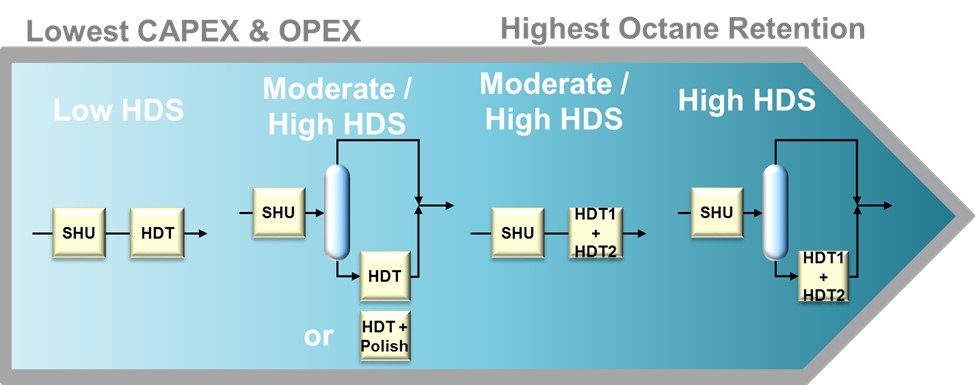
Where a refiner is producing ULSG through CFHT alone, the CFHT’s operating severity will be heavily dictated by the CFHT feed sulfur. In this scenario, if the refiner were to purchase a more opportunistic heavier and higher sulfur crude, there would be a resultant CFHT severity increase and a negative impact to the CFHT’s cycle length. Depending on the CFHT’s original design constraints, there may even be limits on what crude slate can be ran while still allowing production of ULSG. Similarly, with post-treatment alone, there would be an increase in post-treatment feed sulfur thus resulting in an increased severity requirement in the post-treatment unit. This would directionally have a negative impact on the post-treatment unit’s cycle length and would also result in a higher level of olefin saturation and corresponding octane loss. Having both CFHT and post-treatment, there is more potential to balance the overall higher severity requirement between both units thus having a lesser impact on cycle lengths and octane loss. Further, with both CFHT and post-treatment, through feed management and altered operating conditions, it may be possible to continue operations and production of ULSG while either the CFHT or post-treatment unit is off-line. Unfortunately, having both a CFHT and post-treatment unit comes at a high capital investment, and this can be a prohibitive barrier.
WENDY WILDENBERG (Flint Hills Resources)
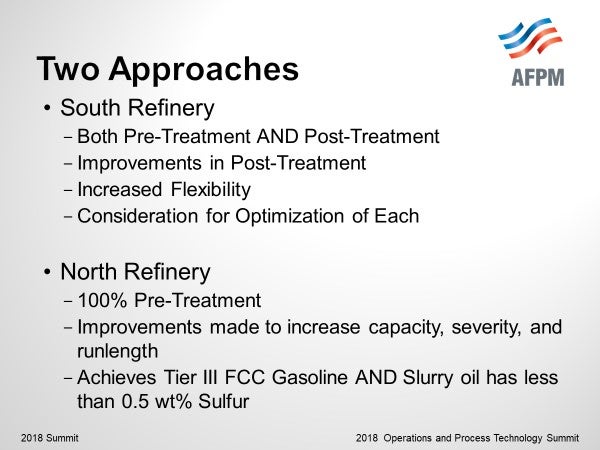
I can share two different approaches of use of hydroprocessing to meet Tier III regulations within the Flint Hills refineries.
A southern refinery has both an FCC Feed hydrotreater as well as an FCC Gasoline hydrotreater. Upgrades to the gasoline hydrotreater have been made in the last several years to achieve higher capacities and severities to lower sulfur levels in gasoline. The FCC Feed Gasoil hydrotreater has a lower severity, may hydrotreat 40 to 90% of the FCC Feedstock – and may even be bypassed if gasoline hydrotreating can be increased for lower opportunity cost maintenance as needed. Attention is necessary to balance the severity of the pre-treatment and post-treatment as Jeff mentioned to balance yield, severity, and runlength of the FCC Pretreater with olefin/octane loss of the post-treater. Feedstocks can be chosen to be processed in the Gasoil hydrotreater to maximize yield of the GOHT/FCC combined while allowing the easier feedstocks to feed the FCC directly.
Prior to the Tier II regulations, our northern refinery was already hydroprocessing 100% of the FCC feed to meet environmental emissions targets as well as for the increased LV yield. Severity increases were necessary to meet the lower sulfurs of Tier II and Tier III since the FCC gasoline is not further processed before gasoline blending. Improvements in catalyst activity were beneficial to lowering start-of-run temperature as well which is very helpful to increase runlength. Established guidelines and attentive monitoring for key parameters such as feed line-ups, hydrogen recycle rate, hydrogen purity, and temperature adjustments allow this refinery to process a large concentration of opportunity feedstocks and achieve longer runlengths (3-4 years). In this refinery, not only is the FCC Gasoline octane maintained without further processing, but the slurry oil sulfur has been < 0.5 wt% for the last several years.
GEORGE HOEKSTRA (Hoeskstra Trading LLC)
Hoekstra Trading sponsored a three-year program of pilot plant testing, catalyst testing, field testing, and market analysis, all aimed at answering the question, “How much octane will be destroyed when post treating severity is increased to make Tier III gasoline?”
The answer from our pilot plant testing is displayed in what we call the post-treater “performance curve” which is a chart of octane versus product sulfur:
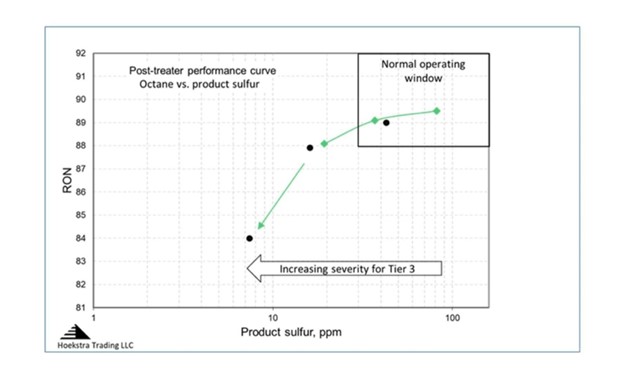
In this chart, post treater reaction severity is being increased as you move from right to left. As severity increases, gasoline sulfur decreases, and so does octane. This feed is from a US refinery, it is a full-range FCC gasoline with 443 ppm sulfur that has been pretreated in a diene saturator. The green and black data points are for two different catalysts. The normal operating window for post-treaters has historically been in the upper right region of the chart where the curve is flat, meaning little octane is lost as you increase severity to decrease product sulfur; but now, we are moving left into a new operating region for Tier III gasoline where the rate of octane loss accelerates. The acceleration is much higher than the industry expectation which says that octane will go down by 0.5 RON when severity is increased to make Tier III gasoline. Our pilot plant data shows it is much higher than that, which was an important new finding in 2015.
The next step was to see whether this important finding holds true in commercial post-treaters in North America. Our client group has run detailed chemical analyses on post treater feed and product samples from field tests on eleven commercial FCC gasoline desulfurizers. The results confirm our pilot plant findings — commercial post-treaters also lose 5 octanes when severity is increased to make Tier III sulfur gasoline.
Not all refineries will lose 5 octanes, only those that are not well-equipped to make Tier III gasoline reliably and profitably. The octane loss in each case depends strongly on the configuration of the FCC process train, the design of the post-treater, and the composition of the raw FCC gasoline. We have seen octane loss over 10 on some commercial units. It is highest for units that have no FCC pretreater and that run heavy, high sulfur feeds.
This chart shows how the performance curve will change for one refiner who decided to add a splitter to his post-treater for Tier III gasoline.
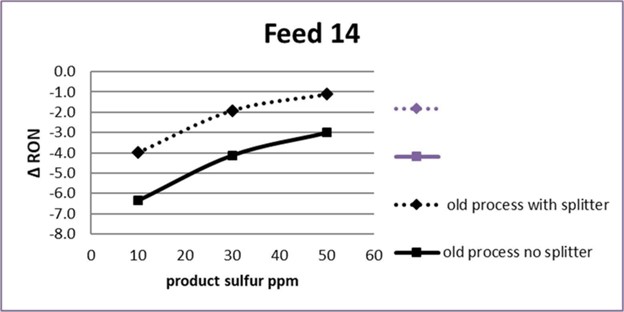
The dashed curve shows, at 20 ppm product sulfur, the octane loss will be 3 with the new splitter, compared to 5 (solid curve at 20 ppm) today.
These curves can be shifted up by cutting heavy tail out of the post treater feed. This chart shows the performance curve in the form of a spreadsheet model that is being used today by refiners and process licensors to estimate and optimize post treater performance for different feeds, process designs, and operating strategies. The dashed curve shows that, with a splitter and endpoint cutting, octane loss can be reduced to 2 RON (dashed curve at 20 ppm sulfur).

The controls at the bottom left of the worksheet permit varying the splitter efficiency, the heavy tail percentage, and the process selectivity to see the effects on the performance curves.
It is possible, with new catalysts and processes, to improve sulfur/octane selectivity by as much as 40% from historical levels. The purple curves show this effect:
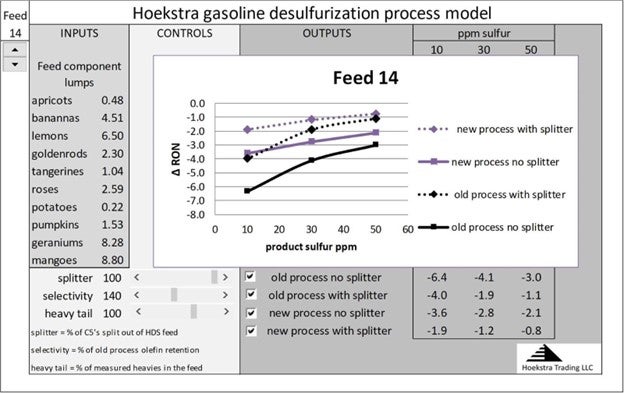
This full range of process improvement is available to refiners today through improved process design, catalyst selection, and feedstock management.
These curves are calculated accurately for any unit by entering the analytical data for that unit’s feed into the spreadsheet model. The model uses reaction rates that have been measured in pilot plant and commercial field tests on real feeds over a wide range of conditions.
The spreadsheet model and all the pilot plant and commercial test data are available to anyone for a small fraction of the cost of this work, which has been done by our client group over the last 3 years.