Question 11: What is the minimum hydrogen sulfide required in the recycle gas for units with low sulfur feed? Do you inject sulfur compounds to maintain a minimum concentration?
Kaspar Vogt (Albemarle)
In some processes, hydrotreating catalysts are used to treat feedstocks containing very low sulfur (below 20 ppm). These processes can include the following:
1. Gulf HPG process for treating pyrolysis naphtha (second stage).
2. Two step naphtha hydrotreating process in steam reforming (ammonia synthesis process).
3. Treating olefinic fuel gas prior to reforming to make synthesis gas for methanol manufacturing.
4. Wax and certain lube hydrofining operations
It appears that in these processes the catalyst slowly loses its HDS activity. This is due to the transformation of the Molybdenum present as activator, and Nickel/Cobalt present as promoters, from their active sulfide form to the inactive metal state. This process is caused by a hydrogen sulfide partial pressure that is too low (see phase diagrams below).
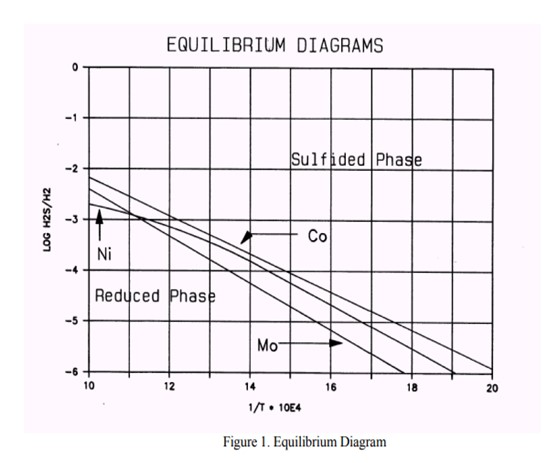
In some cases (usually naphtha units) conditions can arise that contribute to a low H2S partial pressure and could result in metal reduction. Based on the feed properties, operating conditions and product objectives, we can determine whether the unit is or will be operating in a critical operating window. If this is the case, a spiking agent such as DMDS should be added to the feed to boost the H2S partial pressure.
From the phase diagram shown above, we see that the Cobalt is the most critical element. We can begin to move into the Co8S9-phase by decreasing the temperature or increasing the H2S partial pressure by adding sulfur. To move into the "safe" region of the diagram, the Log10 H2S/H2 should be at least -4 at a temperature of 640 deg F.
If the same calculation is done in the reverse order the minimum feed sulfur to avoid metal reduction can be calculated. If we process a 1 ppm sulfur, 70°API naphtha feed at 360 psig at 640 deg F, 80% H2 purity, down to 0.4 ppm sulfur in the product (actual sulfur removal is 0.6 ppm) we conclude that 20 ppm sulfur should be added to avoid catalyst metal reduction. Spiking can be done with a sulfiding agent, e.g., DMDS, DMS.
Minh Dimas (CITGO)
For diesel hydrotreaters, as long as the material being fed to the reactor contains sulfur (i.e., sour feed) and the recycle gas contains 25-50 ppm H2S (by adjusting the amine circulation when necessary), there should not be a need to inject a sulfur-spiking agent into the feed. This ensures a small concentration of H2S at the inlet of the reactor. With reactor temperatures above catalyst activation temperatures, additional H2S is being generated from that point on through the reactor. For us, the sweetest feed is observed when reprocessing off-spec diesel, in which case we may shut down the Recycle H2 Amine Scrubber to preserve the H2S and protect the catalyst.
Tim Lewer (Shell)
In hydrotreating units where the feed sulfur is low and the temperature and H2 partial pressure are low, operation with as low as 20 ppm H2S in the recycle gas has been observed. There is not, however, a universal minimum concentration requirement. The minimum required H2S concentration will vary from unit to unit depending on many factors including, but not limited to: unit feed sulfur concentration, unit pressure, reactor temperature, catalyst type, vent rate, catalyst age, and H2 partial pressure. It is common practice to inject a sulfiding agent such as DMDS to maintain adequate H2S in the recycle gas. In addition, refiners have used sour make up gas streams to provide adequate H2S partial pressure. The guidelines can change based on what catalyst company you talk with, but it all depends on how conservative you want to be. You need to set the H2S low limit to provide a proper buffer zone. It is recommended to discuss H2S concentration requirements for all situations with your catalyst vendor to make sure the catalyst is properly protected against metal reduction.
Gordon Chu (ART)
There is no minimum hydrogen sulfide requirement as long as the feed contains some sulfur as the sulfided catalyst is very resistant to sulfur loss under normal process conditions. We are not aware of any refiners adding sulfur compounds to maintain a minimum H2S concentration during the process cycle.