Question 11: What constitutes adequate quench reserve when you process cracked feedstocks in hydrotreating units? In hydrocracking units? What if a mixture of both gas and liquid quench is used?
WENDY WILDENBERG (Flint Hills Resources)

We will start out this session on Hydroprocessing with an analogy to begin to provide the answer.
Have you ever watched a child walk a dog? Maybe a big dog?
The dog may be obedient and staying with the child for a while – as long as the dog wants to go the direction that the child is leading. The child has the illusion of being in control of the dog.
But if the dog gets distracted – say by a passing squirrel – the dog may take off and hurt the poor child.
Maintaining control means that the dog walker – needs to be able to hang on to the dog – even if it starts to walk or run away. This takes adequate reserve strength - and an early detection and response when the dog just begins to become distracted or when we begin to feel the pull on the leash.
Same with a hydroprocessing reactor. We need to maintain enough recycle hydrogen to provide sweeping of the oil and cooling of the heat of reaction. We need to provide adequate reserve cooling to handle the size of the reactor duty that we allow. Hydrocrackers are big dogs – and ready to pull away and run. Hydrotreaters will walk away until the temperature reaches Hydrocracking temperatures (>800°F).

At that point – we have the increased duty of a Hydrocracker running away – we have measured accelerating at over 10°F per second increase. This slide shows the acceleration measured on a highly active zeolite cracking bed when the quench was decreased by a faulty temperature indication.

Hydroprocessing Units therefore need reserve cooling and good detection and control to be able to regain control of a reactor and stabilize the temperature in case of higher heat of reaction. One addition of increased heat of reaction is more feed olefins. A unit that has more coker feedstocks, with swings or increases in these olefinic feedstocks will require higher reserve cooling duty to compensate than a virgin hydrotreater that has hardly any change in exotherm from feed changes.

A simple definition of a temperature excursion is that the Heat of Reaction is increasing at a rate faster than the ability to increase cooling to balance the reactor. Unlike our dog story – our reactors increase in size of reaction duty as they increase in temperature. It is harder to regain control once they start to get away.

Several causes of increased heat of reaction for your unit during normal operation need to be considered when determining the amount of reserve cooling or quenching.
-
INCREASE in Cracked Stock (increase in olefin and aromatics)
-
INCREASED TIME in REACTOR (partial loss of feed or reduced feed rates)
-
INCREASE in reactor temperature (planned or unplanned like heater over-firing)

Considerations for Hydrotreaters vs. Hydrocrackers:
Differences between Hydrotreating and hydrocracking (catalyst contains acid function) exist that must be accounted for in determining where to maintain reserve quench and determination of safety interlocks / response.
Hydrotreaters can have temperature excursions, but there are a few other factors to consider that allow reserve cooling to be applied in other areas as well or even instead of the reserve quench. Until the high temperature is reached, hydrotreaters will “walk away”. Therefore, reducing firing / tripping the heater fuel gas and stopping feed may stop the growing heat wave in time to prevent temperatures from exceeding design limits.
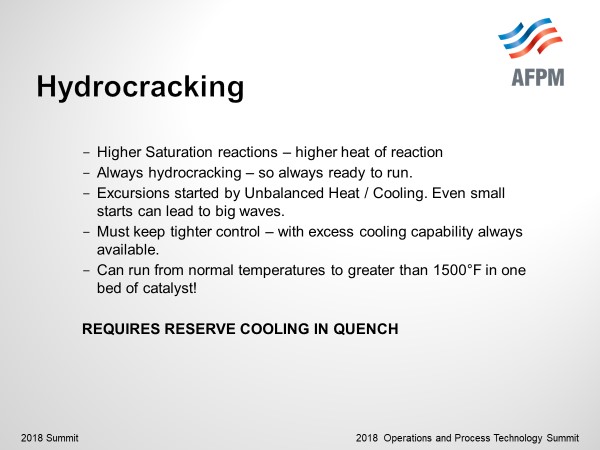
Hydrocrackers have higher heat of reaction from saturation reactions as the cracking function creates olefins that are then saturated. There are plenty of reactants available. Reactor catalyst beds with cracking catalyst must have the ability to apply reserve cooling directly to the bed as well as the ability to cool from upper beds. We have witnessed from a sudden loss of quench, hydrocracking beds rising from normal temperatures to > 1500°F in that bed.
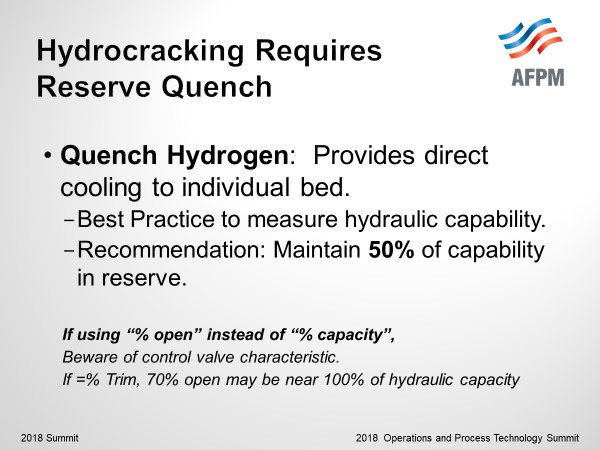
Reserve quench hydrogen provides direct cooling to the individual bed for the fastest response and is required for all hydrocracking beds. Best practice for quench hydrogen is to measure the hydraulic capability and then hold 50% of that capability in reserve. Use caution if setting limits for normal quench on % opening of a control valve. If the control valve has equal percentage trim, 70% open may be near 100% of hydraulic capability. Also ensure that the control system is designed to use the full capacity of the control valve, and not limit the valve opening based on the flow meter span.
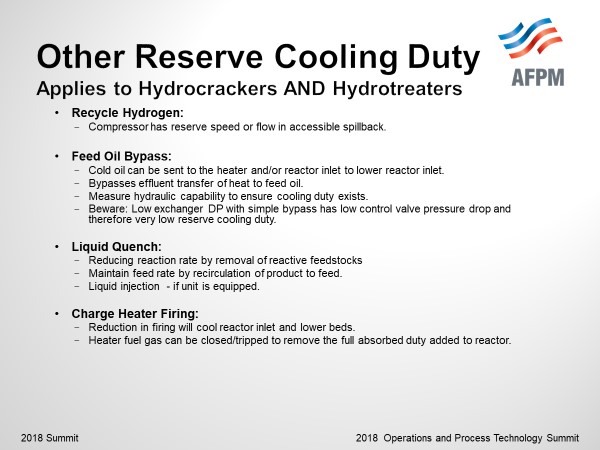
Other cooling knobs that may be applied to reduce the temperature of the reactor include Reserve compressor capacity, feed oil bypass, liquid quench (includes recirculation of product to feed) and reductions in charge heater firing.
Cold oil may be sent to the heater and/or reactor inlet by bypassing the feed/effluent heat exchange. To ensure adequate reserve is maintained, measure hydraulic capability with valve fully open to determine range of cooling available. Beware of the design of low exchanger train pressure drop with a simple control valve bypass. As the bypass control valve is opened, the driving force for flow through the bypass decreases leading to lower hydraulic capability for providing cooling.
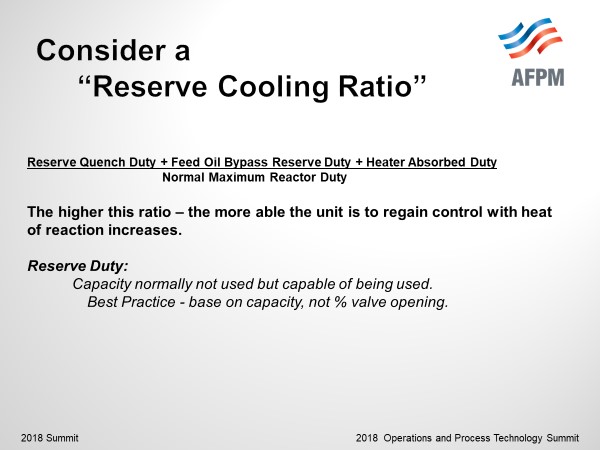
The higher this ratio, the more the unit is capable of regaining control with heat of reaction increases.
Reserve duty is defined as capacity not used for normal operation, but capable for use. Best practice is to set normal operational limits based on % of capacity, not on % opening of control valves.
An important point I need to share in case of recycle compressor failure, no reserve capacity for quench is available. Use Risk assessment in your units to determine procedural and safety interlock responses necessary.