Question 11: How do you set your maximum endpoint targets (short residue, coker, and FCC) for a two-stage mixed feed HCU operating in distillate mode? What is the impact on catalyst life?
CARLSON (Criterion Catalysts & Technologies)
Catalyst typically deactivates due to an accumulation of contaminants and due to process upset coke formation. It also deactivates due to what I will refer to as routine coke formation. Routine coke formation is two-dimensional, its rate being a function of endpoint, as well as the feed aromaticity and how much polyaromatics you have in it. The coke that we generate from the high endpoint tends to come from cracking, both catalytic and thermal, hopefully not too much thermal in our units, whereas the coke from the aromatic content comes from condensation reactions.
The example on this slide is a bit of an eye chart. It is an example of a noise analysis of an LVGO (light vacuum gas oil) feed. The only reason I have it up there is to demonstrate the two-dimensionality of the feed, endpoint versus its hydrogen, and level of hydrogen saturation. The gray line on the chart show the little arrows going into the coke precursors where the deactivation rate becomes too hard for typical operation. It is somewhat arbitrary as it is also strongly a function of unit partial pressure, space velocity, and your operating temperatures. I put it here just to illustrate the fact that from a rate of coke perspective, straight run feeds, of course, can have much deeper endpoints than the cracked stock feeds with a high amount of PNAs in them.
In a typical operation when our customers are also adhering to reviewing the level of other contaminants, we have good, long operational cycles for VGO (vacuum gas oil) straight run feeds with endpoints of 1050°F and 850ºF for 100% FCC cycle oil. Again, these are arbitrary, depending on the unit configuration, and can be optimized as we are going through our operating cycles. So that is where we would start.
When pushing endpoints, you should carefully monitor the result. For a single-feed component, as the endpoint is increased, it will bring with it more of the difficult refractory material that has a higher propensity for coke formation. It is the “tail” of the distillation that contains most of the undesirable coke precursors. The impact of this “tail” can be managed by setting limits on the maximum 95% or 98% boiling point. Other important feed measurements to monitor include metals (Ni, V, Fe, As, Si, Na, etc.), Conradson carbon, nitrogen, and asphaltenes contents.
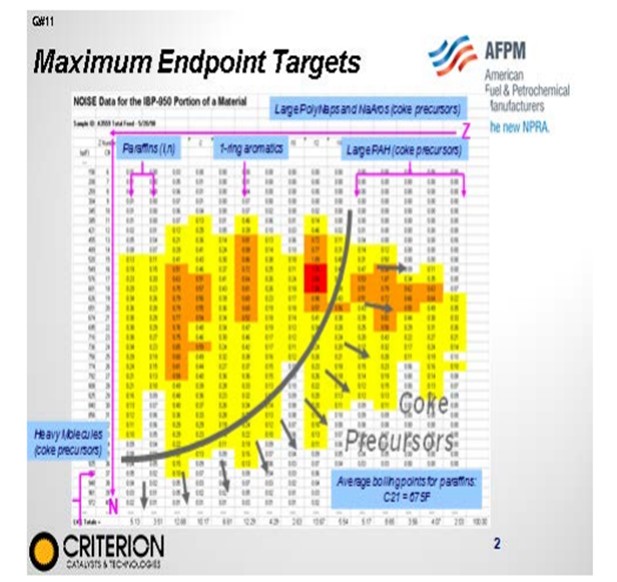
Catalyst deactivation is not the only guiding consideration. This figure illustrates how the polyaromatics can grow into larger polycyclic aromatics, or PCAs, such as coronenes or ovalenes that we run into during hydrocracker operations.
In a high conversion hydrocracker employing a recycle stream, PCAs can accumulate and grow into heavy polycyclic aromatics (HPCAs) due to a combination of the high residence time provided by recycle and the low reactivity of these species. HPCAs are orange-to-red (hence, the name “red death”); and in high concentrations, they cause increased catalyst deactivation, deterioration of yield selectivity, and REAC (reactor effluent air cooler) fouling. FCC cycle oils contain high concentrations of HPCA precursor; and when the feed endpoint is increased, more of these HPCA precursors will enter the unit. “Red death” can be managed with the appropriate amount of unconverted oil purge and/or endpoint control. For optimization, start with something that is reasonable, push until you see your unit’s capability gets a little challenged, and then pull back from there.
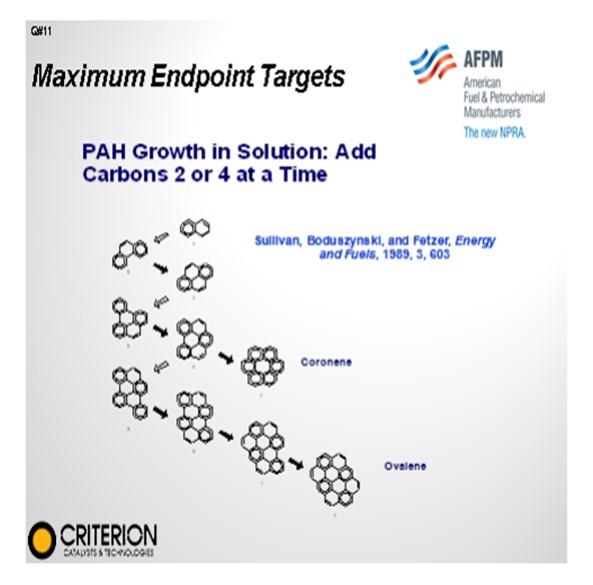
OHMES (KBC Advanced Technologies, Inc.)
I want to add a couple of more points to build onto what Kevin said about really understanding how you are trying to use your hydrocracker. Is it processing all available feed, or are you putting in the really difficult material? What is your ultimate distribution for the incremental cutpoint material? For instance, on the coker, yes, everyone wants to run at minimum recycle, but maybe that is not the best option if the heavy coker is going to the hydrocracker. The same with the gas oil: Are those last few degrees of cutpoint really worthwhile? Because it is really the last 5°F, 10°F, or 15°F of cutpoint that are going to dictate the severity, both in the hydrotreating and the hydrocracking section of the hydrocracker. So, trying to optimize not only the hydrocracker itself but how it fits into the overall refinery is the key.
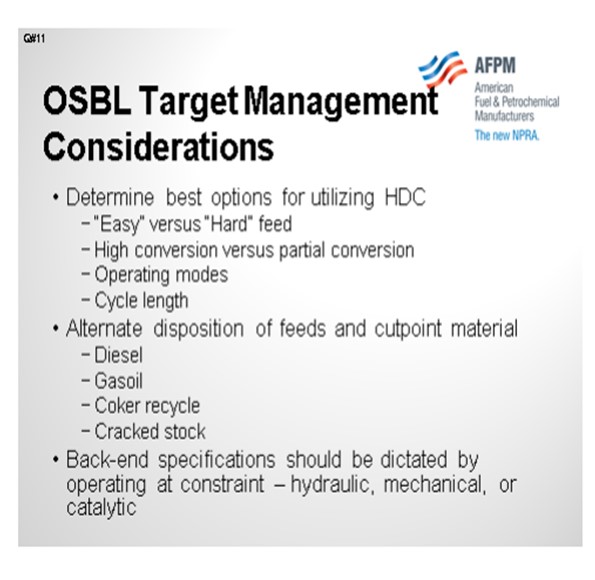
With that as a background, we typically recommend our spec set not only be the blended feed, but you should also look at the individual feeds. So, the old rule of thumb that people would say was, “2 ppm nickel plus vanadium; keeping it less than that and less than 0.5% Conradson carbon.” Again, to Kevin’s comment, those are good starting points, but you need to optimize around that, as well try to understand the distribution in your feeds. I know this is hard to see from the back of the room; but depending on where you are running conventional or unconventional crudes, you can see what those distributions look like. These are generated from Petro-SIM, which we used to help understand these distributions. So, when you are looking at that cutpoint, a simulation tool really helps you figure out what the optimization needs to be. We typically recommend test runs, as well as some model work and proactive catalyst cycle life management, to figure out what that endpoint needs to be.
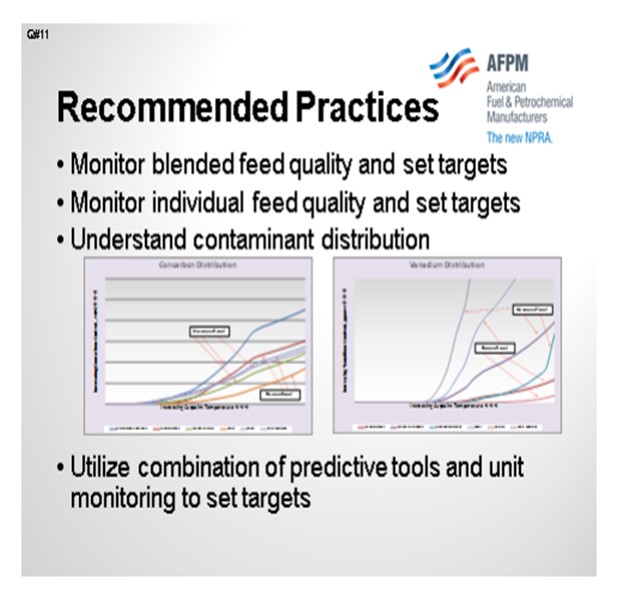
CARLSON (Criterion Catalysts & Technologies)
One other comment to mention is the importance of the modeling. The rigorousness of the modeling is useful as well because an LP (linear program) might show more benefit for going beyond 1050ºF than there really is. You will see that when you put in a barrel of that next cutpoint material, it really does not do anything for your liquid yield gain. So as Robert mentioned, reviewing how you are modeling the impact of that is quite important.
OHMES (KBC Advanced Technologies, Inc.)
One other quick point to the earlier question HPNA (heavy polynuclear aromatics) management: Again, the same principle applies. You have to ask yourself if you really want to go after that last one percent conversion, or would it be better to just bleed that out and maybe give gain the capability of heavying up the feed without plugging everything up with HPNAs. That is an operability and economic decision that each hydrocracking refiner has to make.
KEVIN CARLSON and WARD KOESTER (Criterion Catalysts & Technologies)
When also adhering to other guidelines (limits on trace contaminants and CCR), our customers have achieved long cycles in high-conversion hydrocrackers by limiting the endpoints of straight run VGO to 1050°F and 850ºF for 100% FCC cycle oil. However, the true limit for a given unit and a given feed depends on other factors, such as (a) process configuration, (b) catalyst type, (c) hydrogen partial pressure, and (d) treat gas rate.
When pushing endpoint, you should carefully monitor the impact on unit performance. Just as importantly, you should be sure that your economic models accurately represent the value of higher endpoint. Molecules that boil above 1050ºF produce far more coke and far less liquid than lighter molecules. It is commonly observed that adding a barrel of high-endpoint material gives zero (or negative) incremental yield of converted product.
For a single feed component, as endpoint is increased it will bring with it more of the difficult, refractory material that has a higher propensity for coke formation. It is the “tail” of the distillation that contains most of the undesirable coke precursors and the impact of this “tail” can be managed by setting limits on the maximum 95% or 98% boiling point or the amount of 700+°F or 1000+°F material in the feed. Other important feed measurements to monitor include metals (Ni, V, Fe, As, Si, Na, etc.), Conradson carbon, nitrogen, asphaltenes/heptane insolubles, and aromaticity/paraffinicity.
With a mixed feed, the combined endpoint does not always provide the best indication of that feed’s propensity to coke. That is because from the standpoint of deactivation, you can operate to higher endpoints with straight run material than you can with poly-ring material. This is due to the relationship between endpoint and molecular structure on deactivation.
Figure 1 shows the H2 deficiency (Z value) of the compounds in a straight run LVGO versus the carbon number (N) for those compounds. The boiling points listed on the Y-axis are for paraffins. Paraffins have H/C ratios of (2N+2)/N and Z = +2. Forming a one-ring naphthene removes two H atoms, so Z = 0. Forming a benzene ring removes six more H atoms, so Z = -6. For coronene, a large polyaromatic compound, the formula is C24H12, the H/C ratio is 0.5, and Z = -38. The numbers in each cell represent the wt% of compounds with a given Z and N; components with Z = -12 and N = 16 to 18 are the most concentrated. -As shown by the coke-precursor curve across the middle of the chart, for a given value of N, compounds with low Z (such a polyaromatics) are more likely to form coke than compounds with high Z (such as paraffins).
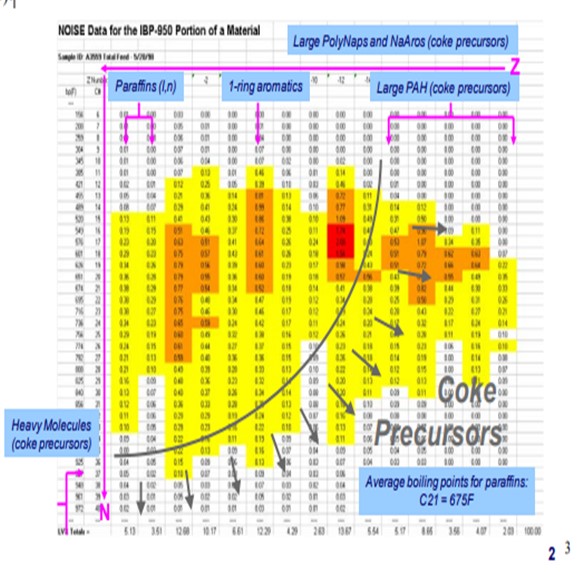
Figure 2 illustrates how polyaromatics can grow to form larger polycyclic aromatics (PCAs), such as coronene and ovalene
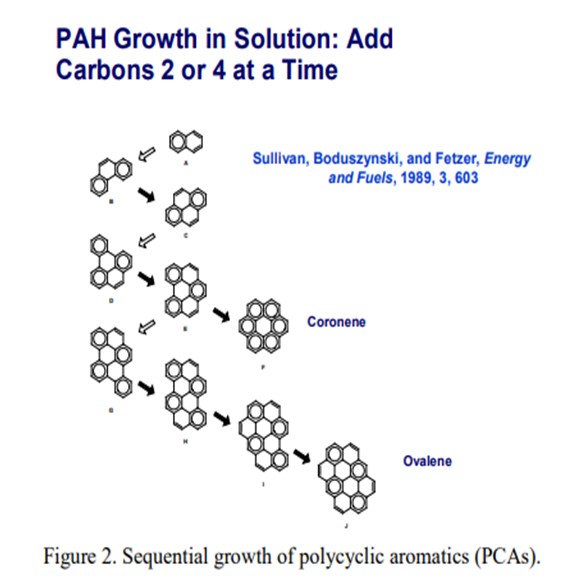
In a high conversion hydrocracker employing a recycle stream, PCAs can accumulate and grow into heavy poly cyclic aromatics (HPCAs) due to a combination of the high residence time provided by recycle and the low reactivity of these species. HPCAs are orange-to-red (hence the name “red death”) and in high concentrations they cause increased catalyst deactivation, deterioration of yield selectivity, and REAC fouling. FCC cycle oils contain high concentrations of HPCA precursor, and when the feed endpoint is increased, more of these HPCA precursors enter the unit. “Red death” can be managed with the appropriate amount of unconverted oil purge and/or endpoint control. You can determine the appropriate amount of purge required by monitoring the amount of coronene and ovalene species in the unconverted oil. The rules of thumb are to keep the coronenes at less than 100 ppm and keep the ovalenes less than 10 ppm.
With unprotected pretreat catalysts, our customers have achieved long cycles with straight run conventional VGOs having endpoints of 1050°F, and with 100% FCC cycle oil feeds having endpoints of 860°F. When the main catalyst is protected with appropriate grading material, the endpoints for straight run feeds can be higher.
Color is an excellent indication of feed quality. Red FCC cycle oils are likely to cause problems. Black VGO is also bad. For such feeds, dilution is not a solution. In one case, mixing just 500 bpd (barrels per day) of black oil into 30,000 bpd of hydrocracker feed did not change the SimDist (simulated distillation) endpoint, but it caused a loss of 40°F of activity in less than two months. In another case, raising the endpoint of an HCO feed from less than 860°F to greater than 900°F doubled the deactivation rate.
LP planning models may not account properly for endpoint effects. A model is wrong if it estimates that a barrel of resid (>1100°F) gives the same yields as a barrel of 650°F to 1050°F material, most likely, that barrel of resid will produce considerable amounts of coke and very little 650°F minus.
OHMES (KBC Advanced Technologies, Inc.)
To supplement the responses given by the other panelists, the outside batter limits (OSBL) implications and impacts should be examined. First, the refiner should clarify how the hydrocracker is being used within the facility. Though the question relates to distillate mode, that mode can be achieved through conventional feedstocks (virgin gas oil and coker gas oil), but may also involve processing other feedstocks (Deasphalted oil, FCC LCO, coker naphtha, etc.). In addition, is the hydrocracker processing relatively “easy” feeds, such as light vacuum gas oil, or “hard” feeds, such as full range heavy coker gas oil?
Also, setting the right endpoint targets depends on the overall conversion level. For instance, if the unit is targeting greater than 95% total conversion, processing high back-end distillation feed can have a dramatic impact on hydrotreating and hydrocracking reactor temperatures. However, if a higher unconverted oil rate is acceptable or even economically desirable, a heavier endpoint can be tolerated. Some good examples of high value unconverted oil dispositions are as FCC feed or Lube Complex feedstock.
Many hydrocrackers operate in multiple modes, depending on unit configuration, unit flexibility, and seasonal economics. Therefore, if the hydrocracker operates in a distillate mode on gas oil feeds and a naphtha mode on distillate feeds, the needs of both modes impact the amount of heavy feed that can be processed. For instance, if the hydrotreating catalyst has “spare” activity and the unit is going into distillate mode on gas oil feed prior to turnaround, the back-end quality targets can be altered to fully consume the catalyst prior to change-out.
Finally, cycle length targets impact the decision on where the hydrocracker feed back-end quality specifications should be set. Depending on marginal cutpoint and stream routing economics, operating the unit at a different cycle length than the standard two years may be economics.
To adjust the back-end specification on hydrocracker feed, an upstream unit cutpoint must be adjusted or stream routing changed. Therefore, to select the right specification, the alternate routing of these streams or cutpoint material must be included. For instance, if the heavy vacuum gas oil cutpoint is lowered to reduce the contaminant load on the hydrocracker treating catalyst, this cutpoint material will now become fuel oil or coker feed, which impacts refinery economics and operability. Adjusting coker heavy gas oil cutpoint affects not only the fractionator’s performance, but also the coker recycle ratio and throughput. Therefore, the hydrocracker backend specifications have to be set in the context of the overall facilities economics and reliable operating targets.
As stated by others, the hydrocracker back-end specifications should be set by contaminants, reliable and reproducible distillation points (i.e., 95%) and methods (simulated distillation or D1160), and impact to polynuclear aromatic (PNA) formation. The refiner should monitor not only blended feed qualities, but also individual feed stream qualities. Monitoring only the blended feed can cause critical contaminants or poor fractionation to be masked or hidden. For example, many hydrocracker units monitor Conradson carbon in the last 10% of the distillation on streams to properly understand the Conradson carbon content, as monitoring Conradson carbon on the bulk stream can dilute the content.
Understanding the distribution of contaminants across the boiling range will influence how the back-end distillation target is set for a given feedstock. The following charts provide some typical examples of how Conradson carbon and vanadium are distributed for different benchmark crudes, based on KBC’s Petro-SIM simulation tool.
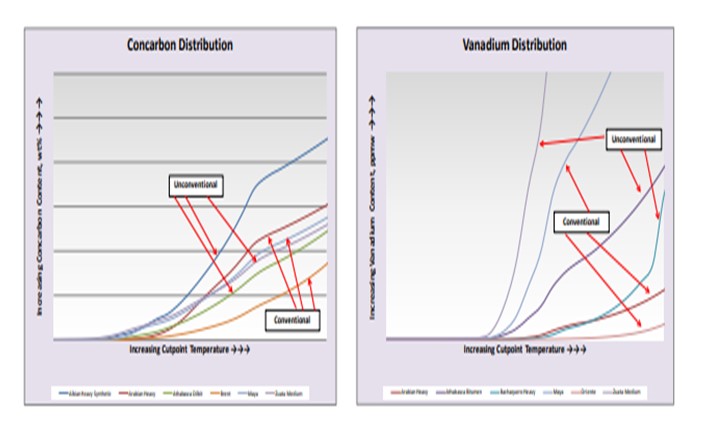
The recommended practice for setting back-end specifications for hydrocracker feed is to use a combination of predictive tools and simulations, such as Linear Program and kinetic model within a process simulator, along with proactive unit monitoring. The tools can help optimize the stream routings and cutpoints to achieve a refinery profitability and operability target, whereas unit monitoring can validate the predicted performance and provide feedback into the analysis, as well as allow for fine tuning of targets against evolving facility and unit limitations. The bottom line is that increasing the back-end distillation of hydrocracker feed will negatively impact the unit operation and cycle length, but the economic benefit must outweigh the penalty. Technical and economic analysis on the specific unit, refinery configuration, and market condition are required to make the proper decision.
SUBHASH SINGHAL (Kuwait National Petroleum Company)
The endpoint of the feed is fixed by the cycle length that the refiner intends to achieve. The higher the endpoint, the more coke on catalyst and the more PNA in feed to the second-stage which may result in exchangers fouling up and catalyst deactivating in the second stage. I have seen HCU operating in diesel mode with feed endpoint of 1020°F and cycle length of two years.