Question 101: What factors influence butylene selectivity in the FCC LPG? What is the relative role of feedstocks, catalysts, additives, and operating conditions?
Kenneth Bryden (Grace Catalysts Technologies)
Fundamentals:
A number of factors influence butylene selectivity in the FCC LPG stream. Figure 1 summarizes the fundamentals of butylene selectivity and maximization. The cracking pathways involved can be thought of as four stages. In Figure 1, the desired pathways for maximizing butylenes are in green and the undesired pathways are in red. The first stage is cracking of the feed to naphtha range olefins. These cracking reactions can occur on zeolite or matrix. In the second stage, these naphtha olefins can react to naphtha paraffins by hydrogen transfer (an undesired pathway), or crack to C3 and C4 olefins. The cracking of gasoline range olefins to C3 and C4 olefins is much faster on ZSM-5 zeolite than Y-zeolite. Catalyst factors that influence the selectivity of butylene versus propylene will be discussed later in this answer. The C3 and C4 olefins that are produced in stage 3 can further react by hydrogen transfer to form propane, iso-butane and butane, which are undesired when maximizing butylene. These reactions occur much faster on zeolite than on matrix. Based on this fundamental reaction scheme, butylenes can be maximized by decreasing the hydrogen transfer activity and by minimizing the cracking of naphtha olefins to propylene. The effects of individual factors on butylene selectivity are discussed in detail below.

Feedstock Effects:
The chemical nature of the starting feedstock will affect the products that can be produced from it. As a feed becomes more paraffinic, butylene production increases. As a feed becomes more aromatic, the olefinicity of the LPG stream will drop.1 As a feedstock becomes more naphthenic, LPG olefinproduction drops. This is because naphthenes are good hydrogen donors and react with gasoline range olefins to make aromatics and gasoline range paraffins.2 Since gasoline range olefins are the precursors to LPG olefins, this depletes the pool of available material to make LPG olefins and reduces LPG olefinicity.
Operating Condition Effects:
Typically, total C4 production depends on conversion, regardless of if the conversion is achieved by reactor temperature or catalyst-to-oil ratio.3 However, the ratio of isobutane to butylene is strongly influenced by reactor temperature. Since hydrogen transfer has higher activation energy than cracking, the rate of cracking increases faster with temperature than the rate of hydrogen transfer4. Thus, as reactor temperature increases, the ratio of iC4/C4= is lowered. As a rule of thumb, the ratio of iC4/C4= drops by 0.025 per 10°F increase in reactor temperature.
Changing reactor pressure will also affect the olefinicity of the C4 stream. Since hydrogen transfer is a bi-molecular reaction, decreasing reactor pressure lowers hydrogen transfer and increases the olefinicity of the LPG stream. Data quantifying the effect of reactor pressure on butylene selectivity can be found in Reference 5.
Increased carbon on regenerated catalyst (CRC) reduces the rate of hydrogen transfer reactions and results in a more olefnic LPG stream. Also, increased CRC will usually lower overall conversion.
Catalyst Effects
Base catalyst affects butylene selectivity through both the rate of hydrogen transfer and through the amount of naphtha range olefins produced. Since increased hydrogen transfer reduces LPG olefinicity, butylene olefinicity drops as the amount of rare earth on zeolite increases, as measured by unit cell size (UCS). Figure 2 presents C4 olefinicity as a function of base catalyst unit cell size. Higher matrix activity increases C4 olefinicity. Lowering the zeolite/matrix ratio of the base catalyst increases gasoline range olefins and thus the amount of butylene produced from these precursors.
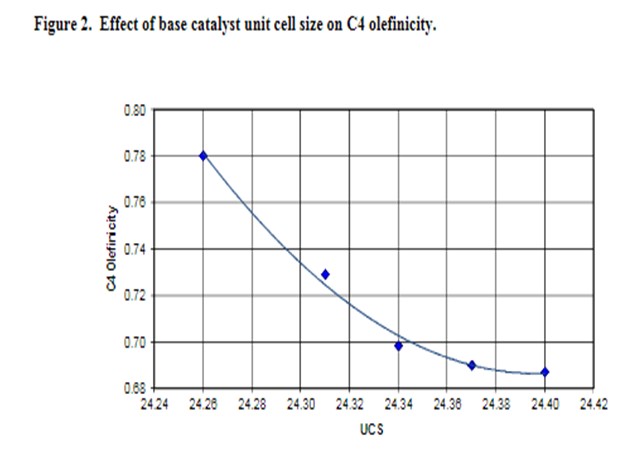
ZSM-5 based additives have a significant effect on the olefinicity of the LPG stream. ZSM-5 cracks the C6+ gasoline range olefins to propylene and butylene. Figure 3 shows the effect of ZSM-5 on the olefins distribution. Adding more ZSM-5 additive will deplete the gasoline range olefins and produce both more propylene and butylene. The increased propylene yield with ZSM-5 additives is not always desirable. A better solution is to boost zeolite isomerization activity within the catalyst to selectively increase the yield of FCC butylene. Grace’s ACHIEVE® 400 catalyst is formulated with multiple zeolites with tailored acidity, to deliver an optimum level of butylenes to keep the alkylation unit full and maintain refinery pool octane. With traditional ZSM-5 technology, cracking of gasoline olefins continues past C7 into the C6 and generates a disproportionate amount of propylene relative to butylenes as shown in Figure 4. The newly developed dual-zeolite technology in ACHIEVE® 400 works synergistically with Grace’s high diffusivity matrix, to selectively enhance olefinicity, preferentially cracking gasoline olefins at C7 and above into butylene. The result is a higher ratio of C4 to C3 olefin yield than separate light olefins additives. Figure 5 illustrates the butylene selectivity improvement of ACHIEVE® 400 catalyst compared to a system using conventional ZSM-5 based additive6. In addition to increasing butylene selectivity, ACHIEVE® 400 has been shown to increase the octane of FCC naphtha.
In summary, butylene selectivity is influenced by a number of complex factors in the FCC. Proper choice of catalysts and additives based on operating objectives and unit constraints is critical in maximizing butylene selectivity. Grace’s technical service team has the experience and resources to help refiners evaluate feed, operating condition and catalyst shifts to maximize butylene selectivity.
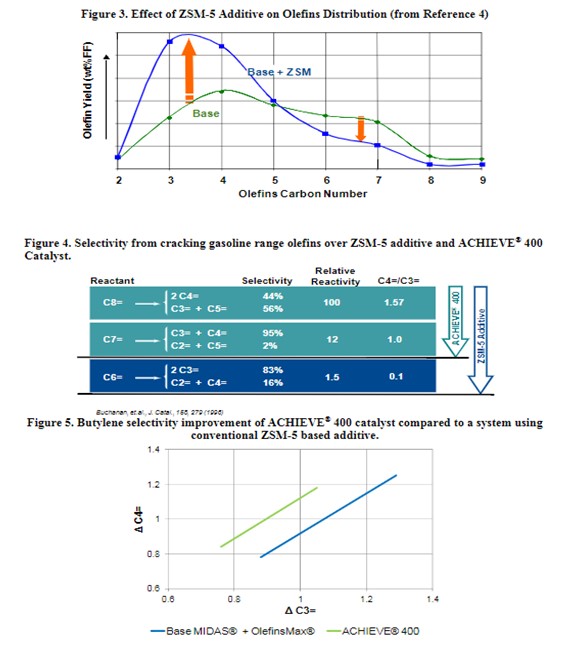