Question 100: What specific changes in yields and product qualities might be expected when processing large percentages of tight oil-derived feeds? What operational changes can be made to address any problems created by these effects?
BULL (Valero Energy Corporation)
We are currently running varying degrees of tight oil at the majority or our refineries. At the refineries that are running a larger percentage of tight oil, the largest field impacts we have identified have been the shift to lighter products. At the same time, it insignificantly increased volume gains and significantly decreased slurry yield. Conversions in the 85 to 90% plus type of yield numbers are really common. The main product impact, as far as the properties, is the decrease in the FCC naphtha octane.
The second half of the question was: What operational changes have we employed? Overall, we have used a staged approach with continuous optimization to combat these challenges resulting from the change in the oil going to the FCC unit. First, we start to decrease the riser temp. In many cases, we have done this so much so that we have to look at where our low temperature unit shutdown trip points are set. Therefore, a first phase is to start taking down riser temperature, so they are not overwhelming our debutanizers and stripping sections downstream.
In many cases, the next phase will be to drop LCO into slurry just to maintain a minimum flow. We have had to do this at one or two plants. After that, we have also started to increase our feed temperature significantly to slow down the cat-to-oil. Finally, throughout this whole process, we have worked with our catalyst vendors to devise a system that will fit within our existing hardware.
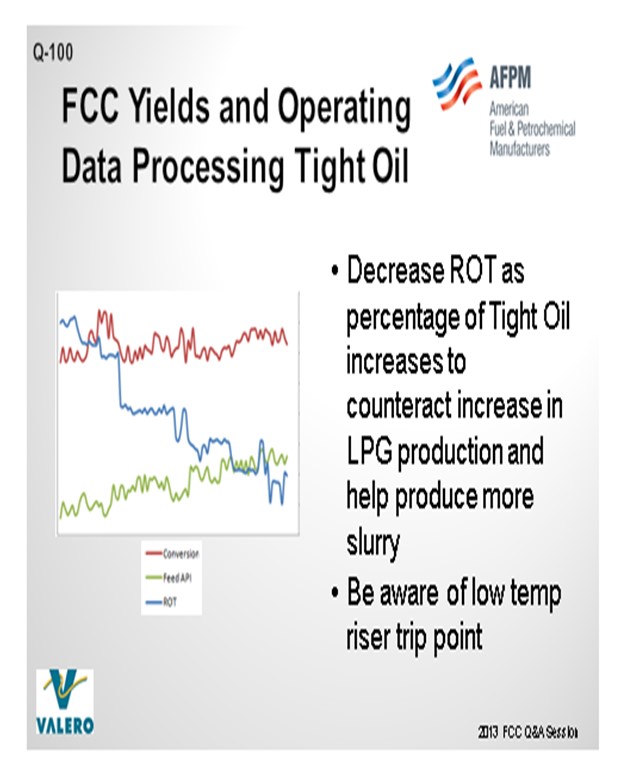
LARSON (KBC Advanced Technologies, Inc.)
The difficulty in this question is the part about specific yields. Your hardware and your specific feed – Bakken, Eagle Ford, and other varieties of that – will all change. To be able to say anything specific is just really not practical. In general, as Jeff has already pointed out, you will see a much bigger increase in conversion. For those of you not yet running large quantities of tight oils, I would suggest using a kinetic model. Begin to step in and see what higher and higher percentages might reveal and what you would expect to see so that you can anticipate the changes you will have to expect; then, you can also add the iron and calcium issues associated with it.
One of the operational considerations that may be a little off the wall is that in the bottom of a coker, you could put fresh feed and take that feed right to the furnace; thus, back into the coker. Well, there is no reason you cannot keep the slurry circuit moving – if you brought fresh feed to the bottom of the fractionator – and then use that as feed back to the riser as a mechanism that keeps down your holding time. That does not do a great job for your slurry circuit. As Jeff already pointed out, you have to keep your pumparound moving. But in effect, you can go to net zero bottoms yield, take your first product off of HCO using feed to the bottom of the fractionator, and put all of it into the riser as a mechanism to get past the holding time. That technique needs to be well-thought out and well-analyzed, but it is possible to look at the fractionator system like a coker.
There is also another idea: You could put in some fresh feed up above the slurry shed deck and strip out any diesel that would be available to you. It is a hot stripping section and would provide some advantage to make sure you do not have any diesel going back into the feed. You could not do 100% of it, but you could do some. So those are just the ideas with which we are still struggling and from which we will still learn.
JEFFREY BULL (Valero Energy Corporation)
We are currently processing tight oil at many of our refineries in varying degrees. For the units running large percentages of tight oil-derived feed, the largest yield impacts are the shift to lighter products, increased overall volume yields, and a significant decrease in slurry yield. Conversions in the 80 to 90%+ range are common. The main product impact is a decrease in FCC naphtha octane.
Overall, we have taken a staged approach with continuous optimization to combat the challenges associated with highly paraffinic feeds containing few contaminants. In general, decreasing riser temperature is the primary handle that you have to attenuate the impact of the higher LPG yield, which often taxes the gas plant. You might have to explore your low temperature trip points as you optimize around reactor temperature. In many cases, you will have to drop LCO to slurry to maintain a minimum flow in the rundown system. We have also increased feed temperature to drive down cat-to-oil. Changes to your catalyst formulation can also help when processing high quantities of tight oil-derived feeds, depending on your operating objectives.
MEL LARSON (KBC Advanced Technologies, Inc.)
The question asks for specific yields and product qualities; and at this point, every unit is unique with hardware design and crude basket being processed, as well as operational targets meeting the market objective; therefore, being specific will revert to being very general.
The yield shift considered is moving from a typical WTI gas oil to tight oil shale with the following feed quality changes:
• Hydrogen wt% on feed increasing from 12 to 13 or higher,
• Total nitrogen content dropping from 2000 to 200 ppm, and
• Conradson carbon wt% of the feed dropping by 0.5 to 0.05.
One method of investigation is to use a kinetic model to review the anticipated changes with various percentages of tight oil feed. Using a kinetic model gives insight when investigating the operational and yields shifts at constant conversion and/or constant severity or riser outlet temperature. As the feed quality improves, the possibility may exist of open capacity in the air blower and wet gas compressor capacity which can be reviewed with a rigorous integrated reaction and fractionation modeling system.
RAUL ARRIAGA (Albemarle Corporation)
The specific changes in yields and product qualities expected when processing large quantities of tight oil-derived feeds (TOs) will greatly depend on the type of catalyst being used in each particular FCCU. In general, TOs will be more crackable than a traditional type of VGO due to the higher amount of paraffins and lower amount of aromatics, based on its PNA (polynuclear aromatics) distribution. Based on this, one would expect a lower FCCU delta coke, a higher circulation rate, and higher FCCU conversion. By the same token, due to the higher amount of hydrogen in these feeds, one would expect lower LPG olefinicity, lower octane, and higher volume expansion. These expectations are presuming that the FCCU can handle the much lower delta coke.
However, the FCCU’s operation and yields would change if there were a higher amount of iron and calcium, as often is present in TOs. Under this situation, an FCCU consuming a high Z/M or low accessibility catalyst may suffer from increased pore mouth blockage and reduced effective activity, manifesting in increased slurry yields and lower conversion. Along the same line, it is worth mentioning that the activity reported in e-cat sheets is typically based on benchscale testing which may not take into account the effects of reduced e-cat accessibility due to testing at long contact and stripping times relative to commercial operations.
When evaluating the economic feasibility of processing TOs, activity by itself may provide only a portion of the information a refiner may need to make a good decision. In these cases, Albemarle recommends measuring the mass transfer character or accessibility of the incumbent and candidate catalysts via the Albemarle Accessibility Index (AAI) to make sure tolerance to pore blocking will be adequate. Last but not least, fresh catalysts that have been deactivated in the lab may not be represented because accessibility and porosity tend to increase with traditional techniques, such as CPS or cyclic deactivation with Ni and V only. In contrast, in a commercial unit, accessibility tends to decline; therefore, when evaluating feasibility for processing of TOs in the lab, it is recommended to apply more advanced deactivation techniques with iron and calcium impregnation as described in our answer to Question 99.
ROBERTSON (AFPM)
That concludes the remarks from the panel. Seeing no additional comments/questions from the audience, this session is now concluded. I want to thank the panelists for all the work they have done since June. And we finished on time. So I thank you all for attending and participating. I would remind you of the FCC P&P (Principles & Practices) occurring tomorrow morning, as well as the Light Tight Oil P&P